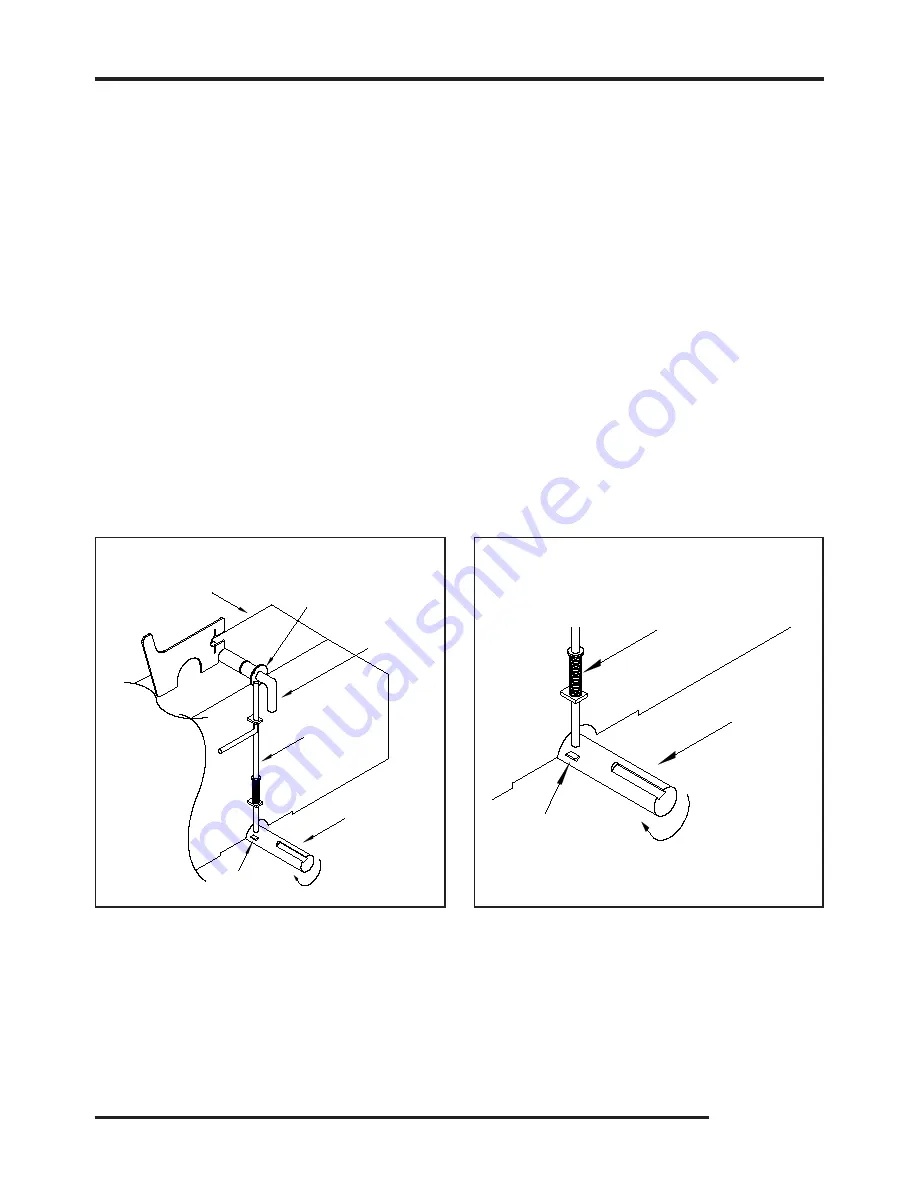
Bandit
Copyright 9/07
PAGE
MODEL 1850
SPRING LOCK FOR HOOD PIN OPERATION
The patented spring lock for hood pin, is installed for safety purposes. It is designed to help keep
the hood pin from being removed if the chipper disc is turning. NEVER ATTEMPT TO PUSH THE
SPRING LOCK FOR HOOD PIN DOWN OR REMOVE THE HOOD PIN, UNTIL AFTER THE ENGINE
AND CHIPPER DISC HAVE BOTH COME TO A COMPLETE STOP.
The spring lock is located on the side of the chipper hood. The top of the spring lock should be
directly behind the hood pin washer when the hood pin is properly installed in place holding the chipper
hood in the closed position (see figure 1).
With the chipper hood shut and hood pin in place the spring lock helps keep the hood pin from
sliding out or from being removed if the chipper disc is turning. There is a shaft cam block installed
on the chipper shaft which will not allow the spring lock to be pulled down if the chipper disc is turning
(see figure 2). When the chipper disc is turning, if the spring lock was to be pulled down or recessed
it would simply hit the shaft cam block bouncing the spring lock back into position not allowing for the
removal of the hood pin.
CONTROLS
Shaft
Shaft Cam Block
Spring Lock For
Hood Pin
Hood Pin
Washer
Feed Direction
Shaft Cam
Block
Shaft
FIGURE
Hood Pin
Spring Lock For
Hood Pin
FIGURE
Содержание 1850
Страница 7: ......
Страница 21: ...Bandit Copyright 9 07 PAGE 19 MODEL 1850 DECALS ...
Страница 22: ...Bandit Copyright 9 07 PAGE 20 MODEL 1850 DECALS ...
Страница 92: ...Bandit Copyright 9 07 PAGE 90 MODEL 1850 CHIPPER COMPONENTS NOTE Parts may not be exactly as shown ...
Страница 94: ...Bandit Copyright 9 07 PAGE 92 MODEL 1850 CHIPPER COMPONENTS NOTE Parts may not be exactly as shown ...
Страница 124: ...Bandit Copyright 9 07 PAGE 122 MODEL 1850 NOTE Parts may not be exactly as shown FRAME ACCESSORY COMPONENTS ...
Страница 126: ...Bandit Copyright 9 07 PAGE 124 MODEL 1850 NOTE Parts may not be exactly as shown FRAME ACCESSORY COMPONENTS ...
Страница 128: ...Bandit Copyright 9 07 PAGE 126 MODEL 1850 FUEL HYDRAULIC TANK COMPONENTS NOTE Parts may not be exactly as shown ...
Страница 138: ...Bandit Copyright 9 07 PAGE 136 MODEL 1850 NOTE Parts may not be exactly as shown GRAPPLE ROTATOR LOADER COMPONENTS ...
Страница 144: ...Bandit Copyright 9 07 PAGE 142 MODEL 1850 CAB COMPONENTS NOTE Parts may not be exactly as shown LEVER STYLE CONTROLS ...
Страница 146: ...Bandit Copyright 9 07 PAGE 144 MODEL 1850 CAB COMPONENTS NOTE Parts may not be exactly as shown LEVER STYLE CONTROLS ...
Страница 148: ...Bandit Copyright 9 07 PAGE 146 MODEL 1850 NOTE Parts may not be exactly as shown OPTIONAL COMPONENTS ...
Страница 152: ...Bandit Copyright 9 07 PAGE 150 MODEL 1850 SERVICE RECORD SERVICE RECORD DATE DESCRIPTION AMOUNT ...