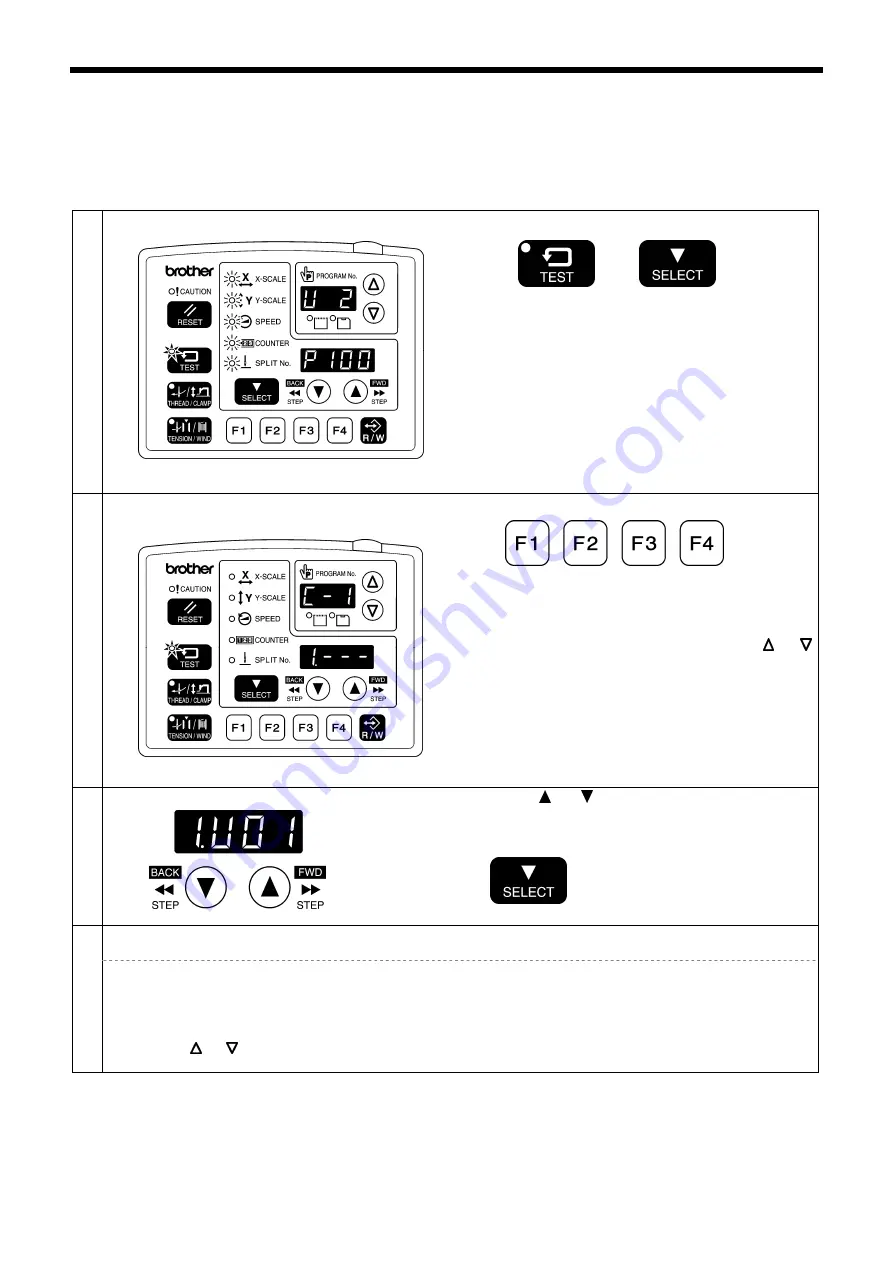
6. USING THE OPERATION PANEL (ADVANCED OPERATIONS)
BAS-300G, BAS-311G, BAS-326G
42
6-8. Using cycle programs
Sewing patterns that have been recorded in user programs can be recorded in up to nine cycle programs (C-1 to C-9).
One cycle program can contain up to a maximum of fifteen steps.
When sewing the sewing patterns in numerical order, it can be useful to record them in a cycle program beforehand.
Cycle programs are enabled when memory switch nos. 400 and 401 are set to "ON".
<Recording method>
1
Switch to user program recording mode.
TEST indicator illuminates, MENU indicator flashes
While pressing the TEST key, press the SELECT key.
•
Check that the menu indicators are flashing.
•
The user program number will appear in the
PROGRAM No. display, and the program number will
appear in the menu display.
Record the sewing pattern that you would like to use in a
cycle program into a user program.
2
Switch to cycle program recording mode, and select
the cycle program number.
MENU indicator switches off
Press a function key from F1 to F4.
•
The cycle program number (C-1 to C-4) will appear in
the PROGRAM No. display, and "1.---" will appear in
the menu display.
Press the function key (F1 to F4) or press the
or
key to select the cycle program number.
3
Set step 1.
Press the or
key to select the user program
number that you would like to record.
Press the SELECT key.
4
Set the rest of the steps in the same way from step 2 onward.
From step 9 onward, "A.---", "b.---", "c.---", "d.---", "E.---" and "F.---" will be displayed.
If you would like to return to a previous step during the setting procedure
<For cycle programs C-1 to C-4>
1. Press the respective function key from F1 to F4 to return to the display for step 1.
2. Press the SELECT key until the desired step is reached.
<For cycle programs C-5 to C-9>
1. Press the or key to switch the cycle program number.
2. Select the desired cycle program number again, and then press the SELECT key until the desired step is reached.
4973Q
4428Q
4444Q