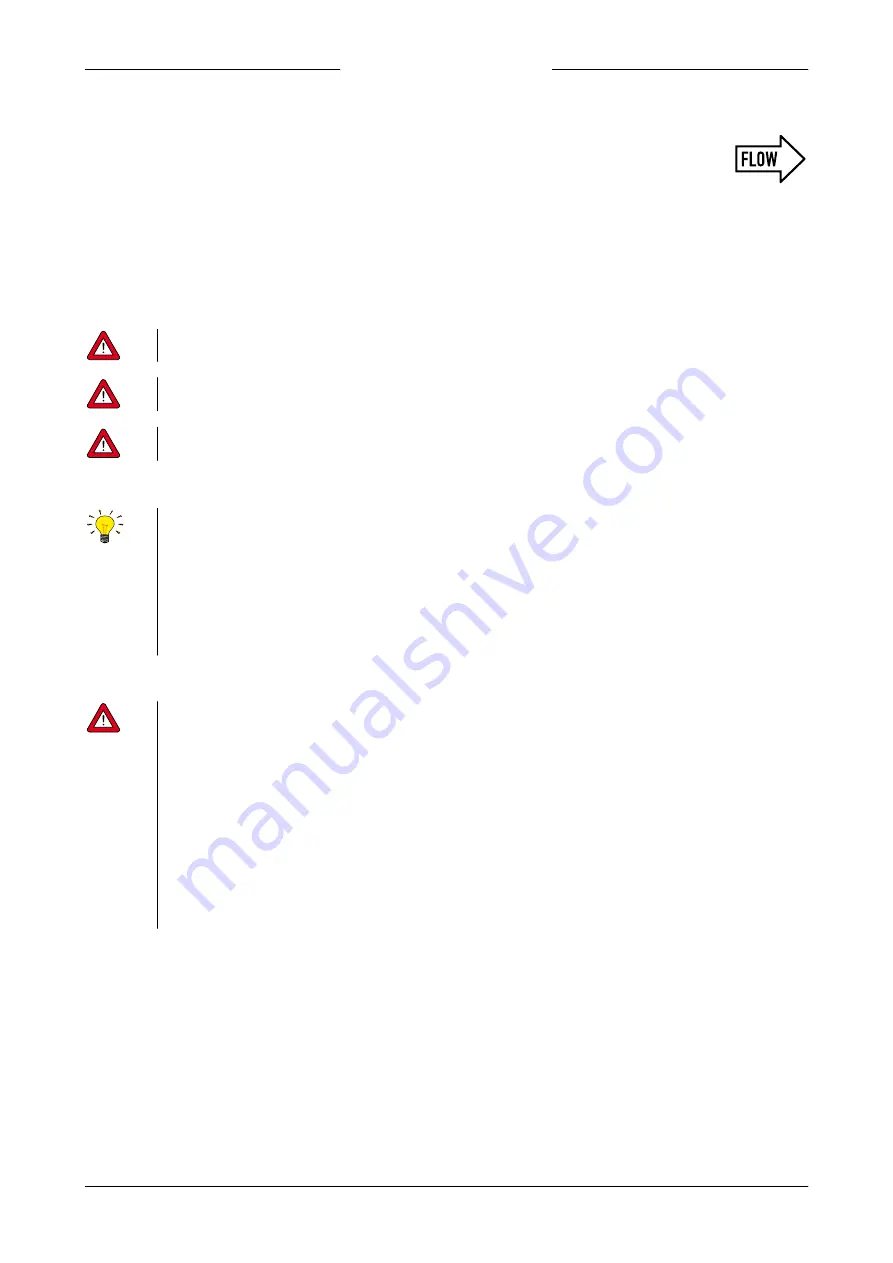
Bronkhorst®
Instruction Manual mini CORI-FLOW™ M1x
9.17.050O
13
2.3.5
Fluid connections
Flow direction
·
Install the mini CORI-FLOW in the process line, in accordance with the direction of the FLOW arrow on the
instrument base.
·
Tighten connections according to the instructions of the supplier of the fittings.
Fittings
Typically, Bronkhorst® mini CORI-FLOW meters/controllers are fitted with compression or face-seal-fittings.
For leak tight installation of compression type fittings, make sure that the tube is inserted to the shoulder in the fitting
body and tube, ferrules and fittings are free of dirt or other particles. Tighten the nut finger-tight while holding the
instrument, then tighten the nut 1 turn.
If applicable follow the guidelines of the supplier of the fittings. Special fitting types are available on request.
Make sure that the instrument is not suspended by the piping.
Check the fluid system for leaks before applying full operating pressure, especially when using hazardous media (e.g. toxic
or flammable).
After using the mini CORI-FLOW for the first time with low temperature media, re-tighten the fluid connections, in order to
prevent leakage.
2.4
Preventing pressure shocks
mini CORI-FLOW instruments handle pressure shocks in the system well, but are not insensitive to pressure fluctuations. For
optimal control stability, observe the following guidelines:
·
Provide a stable (pressure controlled) inlet pressure; put sufficient buffer volume between the pressure regulator and the
instrument. As a rule of thumb, install pressure regulators at a distance of at least 25 times the pipe diameter from the
inlet or outlet of the instrument.
·
When using multiple instruments and/or control valves, prevent interference by putting piping with sufficient buffer
volume between components.
·
Avoid installing multiple instruments or control valves in close proximity to another.
2.5
Preventing hydraulic shocks
In a fluid system where fluid movement (liquid or gas) is forced to stop or start suddenly (by a pump or a shut-off valve), a
hydraulic shock (or fluid hammer) can occur, especially if the fluid velocity is high. This momentum change causes a
pressure surge (spike) traveling repeatedly from one end of the piping to the other. Rapid pressure fluctuations like this can
cause leakage and damage to fluid lines and components, and ultimately damage to the instrument.
The following measures can be taken to prevent or minimize hydraulic shocks:
·
Avoid abrupt fluid acceleration and deceleration.
o
Avoid large pipe diameter transitions by using piping and tubing with an inside diameter that matches that of the
instrument as closely as possible.
o
Keep the fluid velocity through the instrument as small as possible.
·
Install an accumulator to dampen acceleration and deceleration of the fluid flow.
Consult your Bronkhorst representative if you need more information about prevention of hydraulic shocks.