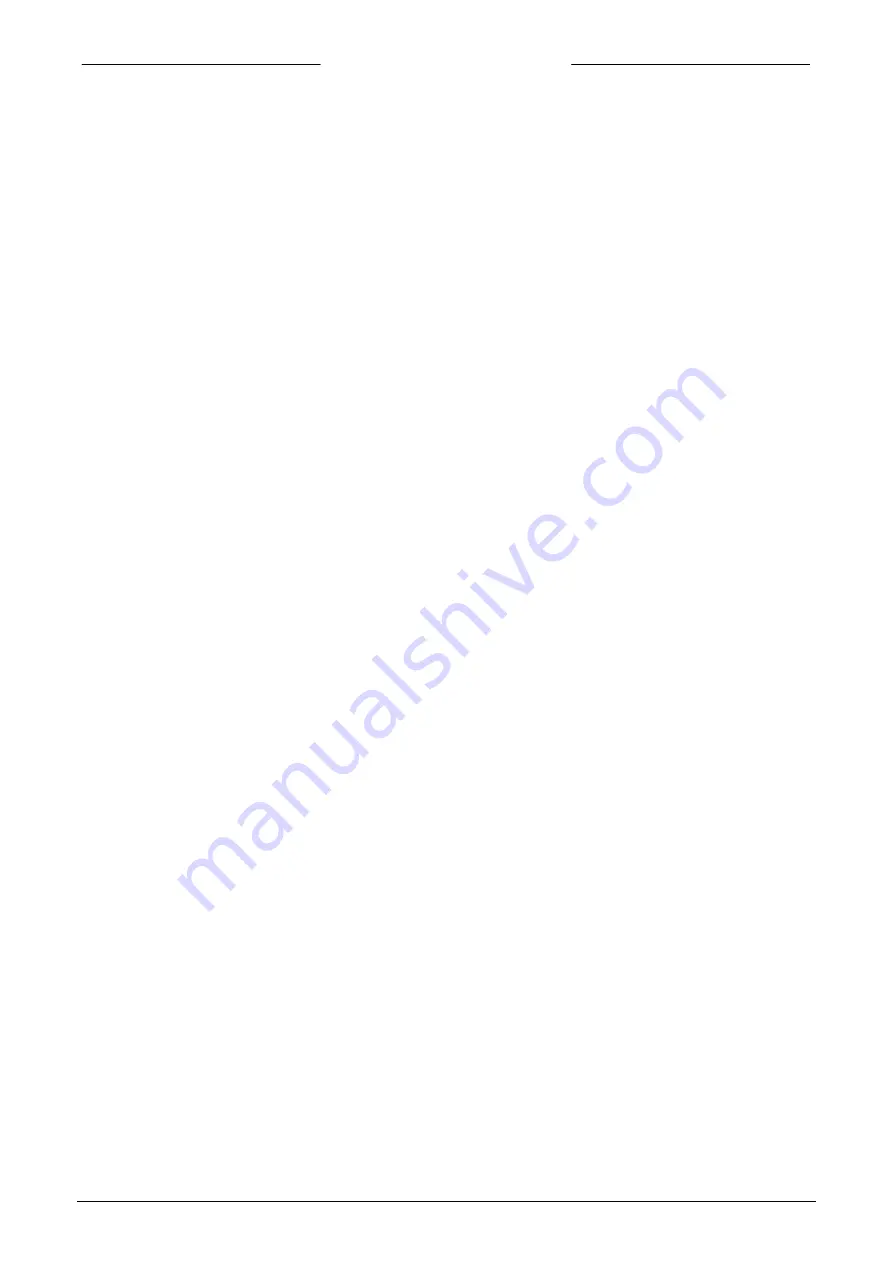
BRONKHORST HIGH-TECH B.V.
9.17.044
page 11
2.6 Piping
BE SURE THAT PIPING IS ABSOLUTELY CLEAN!
DO NOT
install small diameter piping on high flowrates, because the inlet jet-flow will affect the accuracy.
DO NOT
mount abrupt angles direct on in- and outlet, especially not with high flowrates. We recommend at
least 20 pipe diameters distance between the angle and the instrument.
Special care should be taken in regard to reducers placed just in front of the LIQUI-FLOW. High pressure
drop and flow disturbance can occur which can influence the LIQUI-FLOW.
2.7 Electrical
connections
Bronkhorst High-Tech B.V. recommends using their standard cables. These cables have the right connectors
and if loose ends are used, these will be marked to prevent wrong connection.
2.8 Pressure
testing
Each LIQUI-FLOW is pressure tested to at least 1.5 times the working pressure of the process
conditions stipulated by the customer, with a minimum of 8 bar.
The tested pressure is stated on the flow meter/controller with a RED COLOURED sticker. Check test
pressure before installing in the line.
If the sticker is
not
available or the test pressure is incorrect, the instrument should
not
be mounted in the
process line and be returned to the factory.
Each instrument is helium leak tested to at least 2
⋅
10
-9
mbar l/s Helium.
2.9 Supply
pressure
Do not apply pressure until electrical connections are made. When applying pressure to the system, take
care to avoid pressure shocks in the system and increase pressure gradually, especially on high pressure
units incorporating a piston operated control valve.
Make sure in case of a controller that the used valve can withstand the system pressure.
2.10 System purging
If explosive gases are to be used, purge the process with inert dry gas like Nitrogen, Argon etc. for at least 30
minutes at a high enough flow.
In systems with corrosive or reactive fluids, purging with an inert gas is absolutely necessary, because if the
tubing has been exposed to air, introducing these fluids will tend to clog up or corrode the system due to a
chemical reaction with oxygen or moist air.
Complete purging is also required to remove such fluids from the system before exposing the system to air. It
is preferred not to expose the system to air, when working with these corrosive fluids.
2.11 Seals
Bronkhorst High-Tech B.V. has gathered a material compatibility chart from a number of sources believed to
be reliable.
However, it is a general guide only. Operating conditions may substantially change the accuracy of this guide.
Therefore there is no liability for damages accruing from the use of this guide.
The customer’s application will demand its own specific design or test evaluation for optimum reliability.
So check if the seals like O-rings, plunger and packing gland of the capillary are correct for the process.
2.12 Equipment storage
The equipment should be stored in its original packing in a cupboard warehouse or similar. Care should be
taken not to subject the equipment to excessive temperatures or humidity.