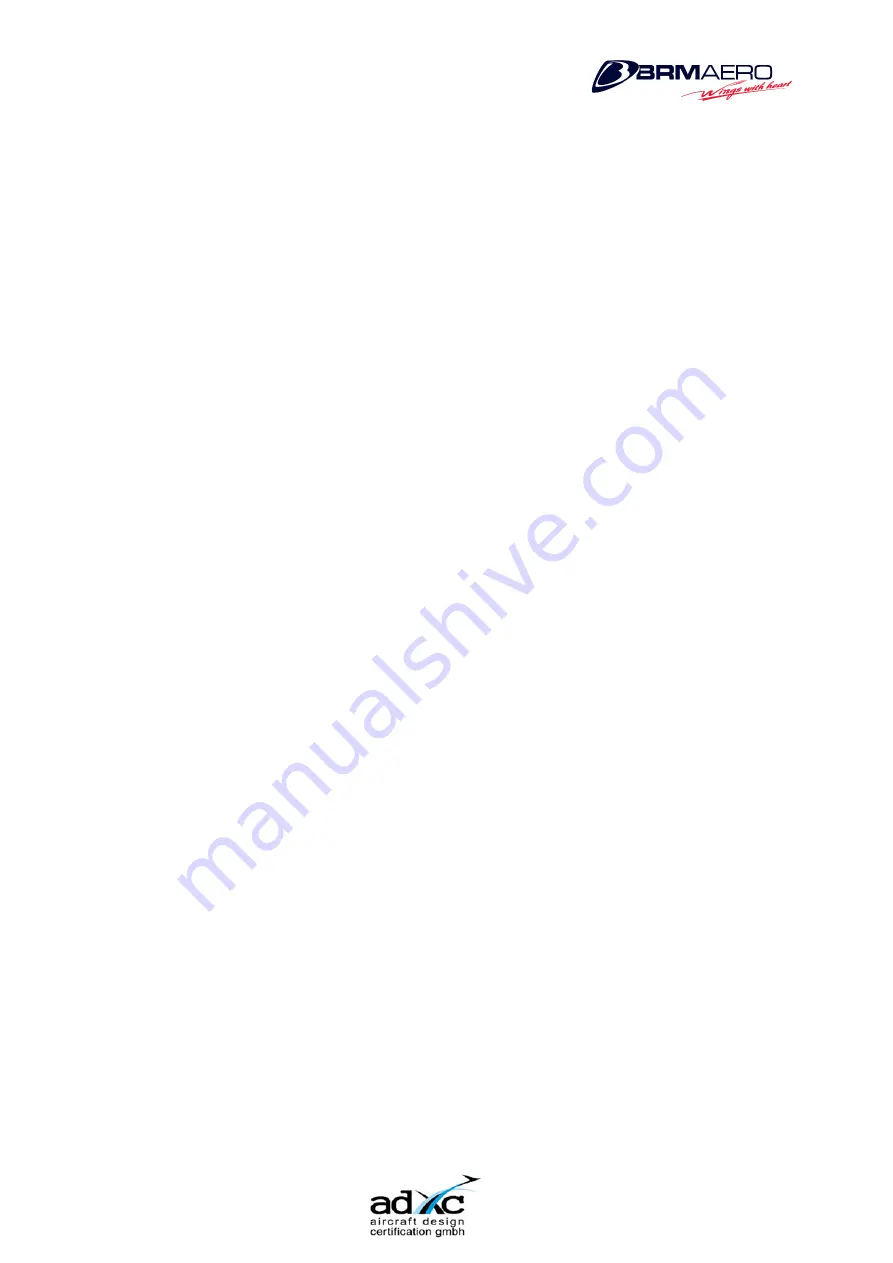
Airplane Maintenance Manual
Bristell
B23
Chapter 08
Chapter 08 Page 6
Issue: 30-Sep-2020
08-20
Leveling
Definitions
The reference line for longitudinal leveling is the fuselage top rivet
row just below the canopy frame.
The identical distances of wing tips to an even floor are the reference
for lateral leveling.
Procedure
▶
Place aircraft on an even floor.
▶
Measure distances of wing tips to an even floor.
▶
Align a spirit level towards the fuselage top rivet row just below the
canopy frame.
▶
Place suitable wooden strips under the respective tires.
Содержание BRMAERO Bristell B23
Страница 152: ...Airplane Maintenance Manual Bristell B23 Chapter 28 Chapter 28 Page 10 Issue 30 Sep 2020 Intentionally left blank ...
Страница 156: ...Airplane Maintenance Manual Bristell B23 Chapter 31 Chapter 31 Page 4 Issue 30 Sep 2020 Intentionally left blank ...
Страница 214: ...Airplane Maintenance Manual Bristell B23 Chapter 55 Chapter 55 Page 8 Issue 30 Sep 2020 Intentionally left blank ...
Страница 222: ...Airplane Maintenance Manual Bristell B23 Chapter 57 Chapter 57 Page 8 Issue 30 Sep 2020 Intentionally left blank ...
Страница 234: ...Airplane Maintenance Manual Bristell B23 Chapter 72 Chapter 72 Page 4 Issue 30 Sep 2020 Fuel Type ...