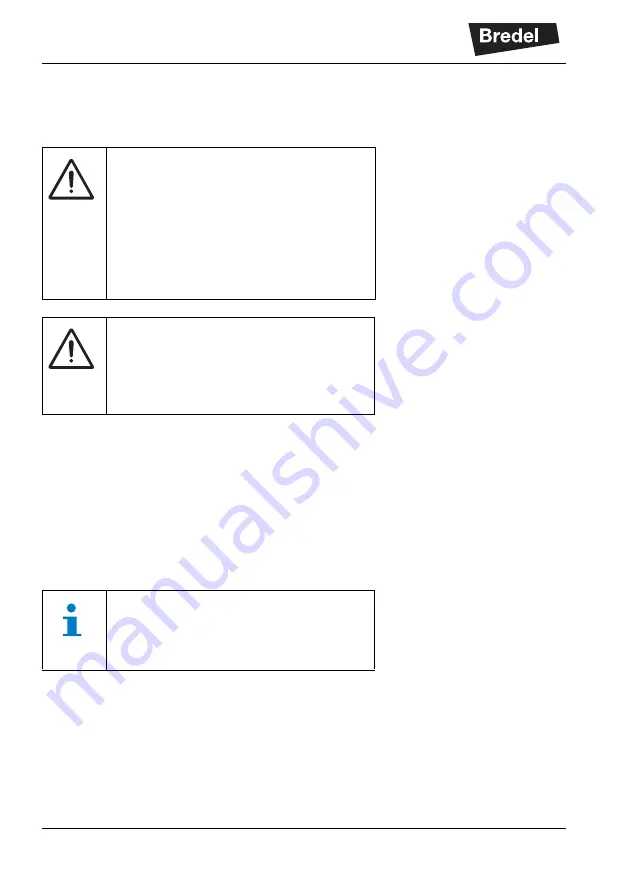
MAINTENANCE
34
8
MAINTENANCE
8.1
General
Only use original Bredel parts when maintaining the
hose pump. Bredel cannot guarantee correct operation
and any consequential damage that occurs from the
use of non-original Bredel components. Also refer to
chapters
and
Check that your delivery of original parts is correct and
check it for any transport damage. If parts are
damaged, consult your Bredel representative.
8.2
Maintenance and periodic inspections
The following diagram shows the maintenance and
periodic inspection that need to be carried out on the
hose pump to guarantee optimal safety, operation and
life of the pump.
WARNING
Disconnect and lock the power supply to
the pump drive before any work is carried
out.
In case the motor is fitted with a frequency
controller and has a single-phase power
supply, wait two minutes to make sure that
the capacitors have discharged.
WARNING
Do not remove the pump cover if the power
cable is connected to the motor. Do not
connect the power cable to the motor if the
pump cover is removed.
Before installation, always check the condi-
tion of the supplied parts. Do not install
damaged parts. In case of doubt, contact
your Bredel representative.