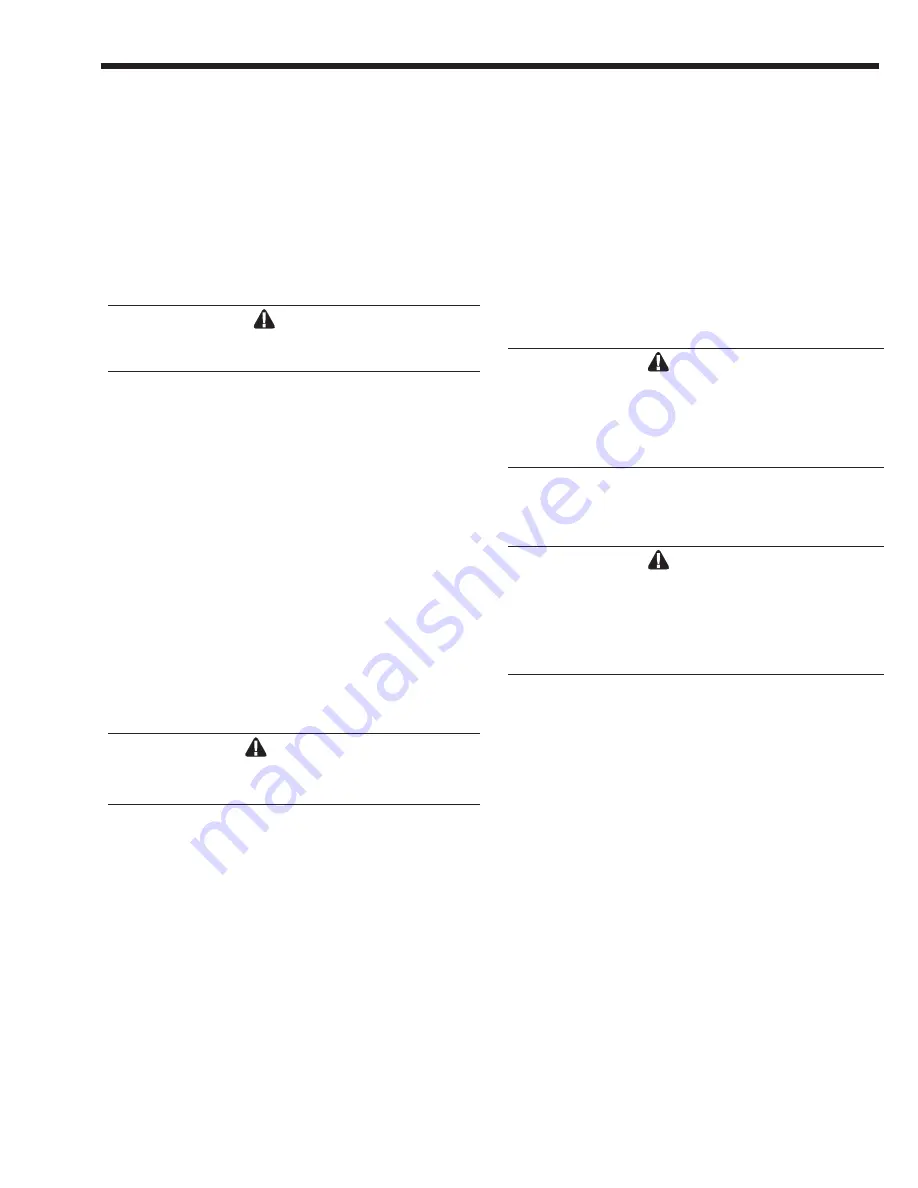
Page 73
Brute
HIGH EFFICIENCY COMMERCIAL BOILERS AND VOLUME WATER HEATERS
Flame Sensor
The flame sensor is a single rod system. To replace the flame
sensor electrode, shut off the 120 Volt power supply to the
boiler. Turn off all manual gas valves connecting the boiler
to the main gas supply line. Remove the front door of the
boiler to gain access to the flame sensor electrode. Remove
the flame sensor wire from the electrode. Remove the two
bolts fastening the electrode to the burner doors. Remove
and replace the old flame sensor gasket. If the old electrode
is determined to be defective, install a new flame sensor
electrode in the reverse order.
Caution
The ignitor and sensor may be hot, and can cause
burns or injury.
Transformer with Integral Circuit Breaker
The appliance has a 24Vac transformer with integral 4 amp
circuit breaker installed to supply the control voltage required
for the appliance. The transformer is sized to provide power
for the Brute unit only, and should not be used to supply
power to additional field devices. If additional loads are
added, or a short occurs during installation, the integral
circuit breaker may trip. If this happens, be sure to reset the
circuit breaker before replacing the transformer.
The transformer is mounted underneath the control panel.
If the transformer must be replaced, turn off the 120Vac
power to the appliance. Remove the transformer wires
from the terminal blocks. Remove the fasteners holding the
transformer, then remove the transformer. Replace with a new
transformer in the reverse order.
If the transformer is replaced with a part other than the OEM
transformer, be sure to add circuit protection if it is not
integral to the new transformer.
WARNING
Failure to include proper circuit protection may lead
to premature component failure, fire, injury or death.
Blower
The combustion air blower is a high-pressure centrifugal
blower with a variable speed motor. The speed of the motor
is determined by the control logic. 120 Volt power remains
on to the blower at all times. If the blower must be changed,
turn off the 120 Volt power and gas supply to the unit. Take
the front panel off. Disconnect the 120 Volt and control
signal connections from the blower. Disconnect the bolts
connecting the Venturi to the blower housing. Disconnect the
fan outlet bolts from the burner door blower arm. If the fan
is determined to be defective, replace the existing fan with a
new one, reversing the steps listed above. Be sure to install
all of the required O-rings and gaskets between the blower
arm and the blower and blower face and venturi flange.
Heat Exchanger Coils
Black carbon soot buildup on the heat exchanger is caused
by one or more of the following; incomplete combustion,
combustion air problems, venting problems, or heater short
cycling. Soot buildup or other debris on the heat exchanger
may restrict the flue passages.
If black carbon soot buildup on the heat exchanger is
suspected, disconnect the electrical supply to the unit, and
turn off the gas supply by closing the manual gas valve on the
unit. Access the heat exchanger through the burner door at the
front of the boiler, and inspect the tubing using a flashlight. If
there is a buildup of black carbon soot or other debris on the
heat exchanger, clean using this procedure:
WARNING
Black carbon soot buildup on a dirty heat exchanger
can be ignited by a random spark or flame. To prevent
this from happening, dampen the soot deposits with
a wet brush or fine water spray before servicing the
heat exchanger.
NOTE: The Warranty does not cover damage caused
by lack of required maintenance, lack of water flow,
or improper operating practices.
WARNING
Failure to rinse the debris from the heat exchanger
and temporary drain line may lead to clogged
condensate lines, traps and neutralizers. Condensate
pumps (if used) may also be damaged by the debris
left behind, possibly causing property damage.
1.
Shut off the 120 Volt power supply to the boiler
2.
Turn off all manual gas valves connecting the boiler to
the main gas supply line.
3.
For NT 600 models only:
(All other sizes please skip to step four)
NT 600 models will require the gas valve to be removed
in order to remove the burner door. To do this, remove
the wiring connections from the gas valve. Remove the
flange bolts from the gas supply pipe connected to the
gas valve (1B). Remove the flange bolts connecting
the gas train to the Venturi (1A). Remove the gas train
assembly, and keep the gaskets and O-rings.
4.
Remove the four bolts connecting the blower flange to
the burner door arm.
5.
Remove the nuts located on the outside diameter of the
burner door to the heat exchanger.
6.
Remove the burner door and burner assembly from the
heat exchanger.
7.
Disconnect the condensate drain line.
8.
Attach a longer hose to the drain and run it to a bucket.
Содержание Copper Brute II BWCH 2000
Страница 4: ...BRADFORD WHITE...
Страница 26: ...Page 22 BRADFORD WHITE 150 285 Figure 23 Minimum Venting Distance...
Страница 32: ...Page 28 BRADFORD WHITE Figure 24 Hydronic Piping Single Boiler Zoning with Circulators Brute TM...
Страница 48: ...Page 44 BRADFORD WHITE Figure 38 Ladder Diagram 7 9 Ladder Diagram...
Страница 96: ...Page 92 BRADFORD WHITE Parts Illustration 4 Internal Components Sizes 750 850...
Страница 98: ...Page 94 BRADFORD WHITE Parts Illustration 6 Gas Train Components Sizes 600 850...
Страница 100: ...Page 96 BRADFORD WHITE Parts Illustration 8 Electrical Components Front Battery CR2032 Touchscreen Back...
Страница 102: ...Page 98 BRADFORD WHITE Notes...
Страница 103: ...Page 99 Brute HIGH EFFICIENCY COMMERCIAL BOILERS AND VOLUME WATER HEATERS Notes...