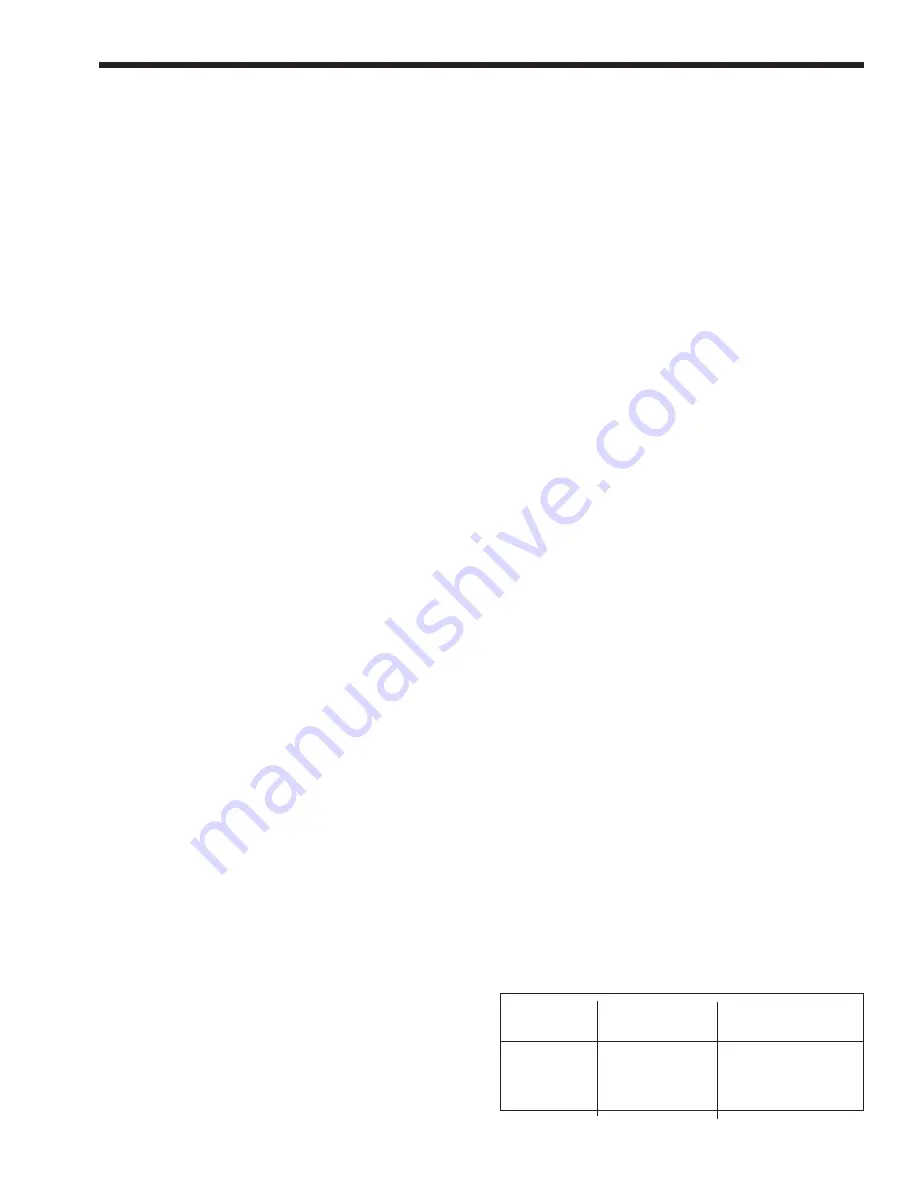
Internet Version for Reference Only
BRADFORD WHITE
Page 10
Copper Brute B4 Volume Water Heaters
Page 11
NOTE:
It is possible to have hard and soft
water in the same city. Check with the local water
companies.
If an installer sees damage to any water handling
equipment at the installation site, it should be repaired
as soon as possible to help reduce maintenance costs.
If there is erosion, resize the pump to reduce water
velocity before the tube ruptures. If scaling is bad,
set up a heat exchanger tube-cleaning maintenance
schedule to prevent heat exchanger tube cracking
and wear. Not fixing the condition will mean serious
damage to the heater and the water system.
NOTES:
• In areas where the water supply is soft or
corrosive, the heater must have cupronickel tubes
in the heat exchanger.
• Bradford White does not warrant heat exchangers
damaged by scaling, corrosion, or erosion.
2.6.3 Freeze Protection
Although Copper Brute heaters are design
certified for outdoor installations, such installations
are not recommended in areas subject to freezing
temperatures unless proper precautions are taken.
Consult the local factory representative or Bradford
White for additional information.
2.6.4 Water Hardness
Consider the water hardness when selecting a
pump for the heater (see Table 3). Hard water needs a
pump which can provide high flow to prevent scaling,
while soft water needs low flow to prevent erosion.
2.6.5 Pump Requirements
The Copper Brute heater has a factory installed
pump which is for heater-to-tank circulation only.
Pump performance is shown in Table 4.
The pump that is mounted on the heater is sized
for the heat exchanger and 30 feet (9.1m) of 1-1/2"
pipe, including six (6) 90° elbows. If more piping is
needed, contact Bradford White for options.
The water temperature entering the Copper Brute
must be at least 110°F (43°C).
Figures 20, 21 and 22 show typical piping
arrangements. For assistance with other piping
methods, contact Bradford White.
24. Fasten the capillary tube(s) by squeezing the
retaining clip together, then tighten the screw.
25. Feed the two brown wires through the top hole
on the left side until the conduit elbow is against
the jacket.
26. Fasten the conduit by sliding the retaining nut
over the two brown wires (inside the control
compartment) then screwing it down finger-tight
on the conduit elbow.
27. Straighten the capillary tubing and fasten it to the
side of the heater under the channel. Use the self-
tapping screws to fasten the channel to the jacket.
28. Feed the two white wires into the control
compartment. Attach one wire to the terminal
in the manual reset hi-limit switch. If one is not
installed, attach it to terminal No. 1. Connect the
other wire to the red wire attached to the fuse
holder.
29. Attach the two brown wires to terminals No. 5
and 6 on the terminal strip. Keep all wiring away
from surfaces that will get hot during heater
operation.
30. Replace the gap closures and tighten the screws
securely.
31. Replace the three grommets and the cap.
32. Reinstall the drain plug and drain valves.
33. Slip the flue collector assembly back down inside
the enclosure.
34. Carefully slip a hand inside to make sure there
are no gaps between the heat exchanger and the
flue collector.
35. Check to make sure the wiring is not pinched
against sharp edges, or resting on the collector
assembly.
36. Replace the two flue collector holddown clamps.
37. Replace the top assembly and fasten it with the
hex-head screws.
38. Replace the front cover.
39. Reinstall the vent cap or drafthood if one was
removed.
40. On indoor installations (sizes 175-250), insert the
draft hood switch plug into the receptacle on the
left side of the heater.
2.6.2 Water Chemistry
Bradford White equipment is designed to be used
in a variety of water conditions. With the proper pump,
the water velocity in the heat exchanger tubes is kept
high enough to prevent scaling from hard water, yet
low enough to avoid erosion by soft water.
Hardness Grains per Parts
Category Gallon per Million
Soft 1 through 7.5 17 through 128
Normal 7.6 through 17 129 through 291
Hard Over 17 Over 291
Table 3. Water Hardness.