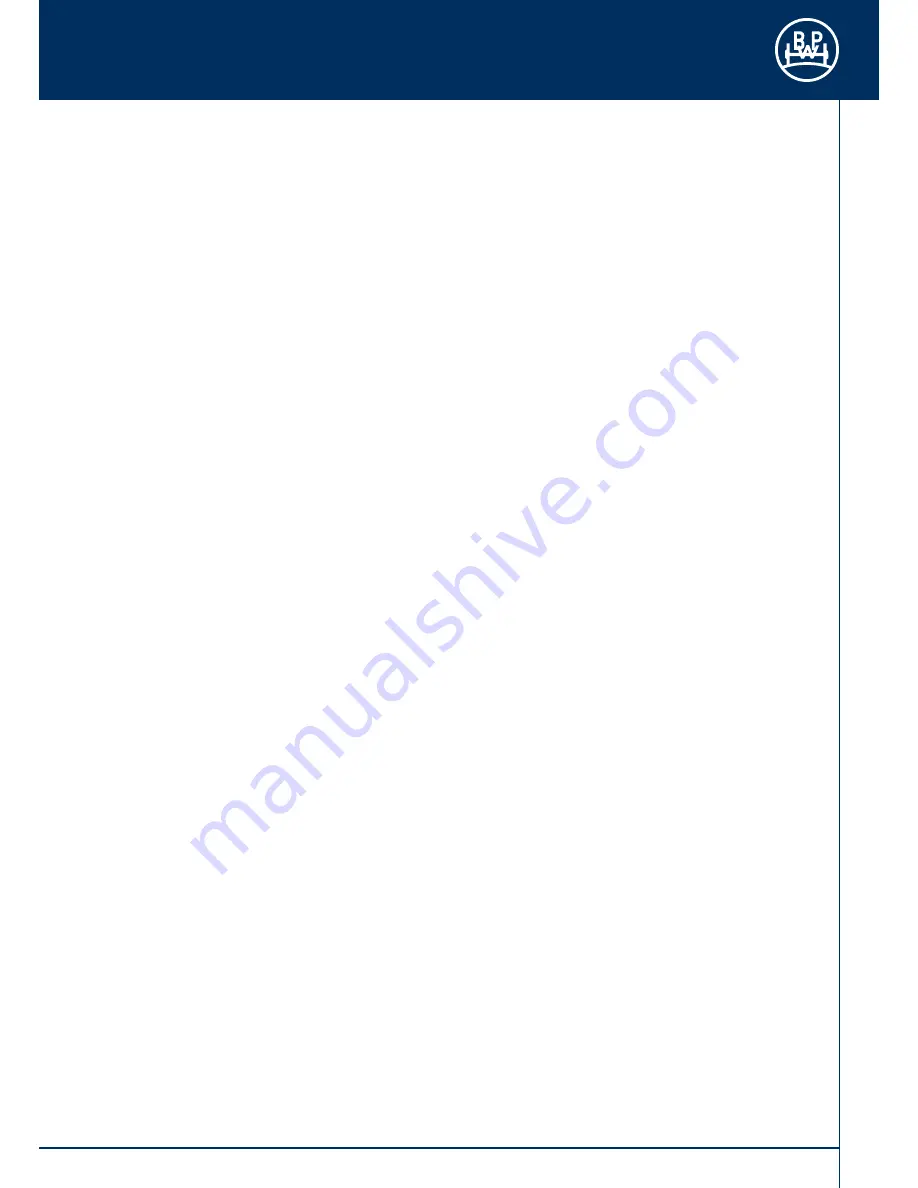
3
Table of Contents
Page
1 Introduction
1.1 ECO Tronic EBS
4
1.2
Abbreviations
7
1.3 Safety information
8
1.4
System
layout
9
1.5
General
components
1.5.1 Location of components in the trailer
10
1.5.2 Primary features of the Modulator
11
1.5.3 ECU connector identifi cation
13
1.5.4 Overview of electrical connections
14
1.5.5 Wiring diagram - 2M
15
1.5.6 Wiring diagram - 3M
16
1.5.7 Overview of pneumatic connections
17
2 Installation options (Confi gurations)
2.1 Semi and centre axle drawbar trailers
2.1.1 2S/2M and 4S/2M, side by side
18
2.1.2
4S/3M
19
2.1.3 2S/2M + SL, side by side
20
2.2 Drawbar trailers (full trailers)
4S/3M
21
3 Chassis installation
3.1 Mounting of the Modulator
3.1.1 Position without Trailer Roll Stability (TRS) 22
function
3.1.2 Position with Trailer Roll Stability (TRS)
23
function
3.1.3
Identifi cation of ECO Tronic EBS ports
24
and
fi xing
- Main Modulator
- Additional Modulator
3.1.4 Painting - protected areas
26
3.1.5
Mounting
27
3.2.
Electrical
wiring
3.2.1
Wiring
schematic
28
3.2.2
Wiring
diagram
29
3.2.3 Auxiliary equipment wiring
30
3.2.4 General installation recommendations
31
-
cabling
3.2.5 General installation recommendations
32
- ISO 7638
3.2.6 General installation recommendations
33
- junction box
3.2.7 POWER / DIAG /Sensor / AUX cabling
34
3.2.8 POWER (ISO 7638) connections
35
3.2.9 POWER (ISO 1185) /
36
Super AUX connections
3.2.10
DIAG
connections
37
3.2.11 DIAG / Side of vehicle connection
38
Page
3.2.12 Connectors / Blanking plugs
39
3.2.13 Sensor / AUX plugs
40
3.2.14 Sensor / AUX connections
41
3.2.15 Sensor connections / cabling
42
3.2.16
COLAS
®
+
/ ILAS
®
-E connections
43
3.2.17 Auxiliary equipment wiring
44
3.2.18
Multimeter
measurements
46
4 Piping
4.1
Pipe
recommendations
48
4.2 Brake piping layout
4.2.1 2M, 3-axle semi trailer, side by side
50
4.2.2 3M, 3-axle semi trailer
51
4.2.3 3M, 2-axle drawbar trailer (full trailer)
52
4.3 Air suspension system piping layout
Air suspension levelling valve, COLAS
®
+
53
and
ILAS
®
-E
5 Operating and installation instructions
5.1 Brake system
54
5.1.1
Coupling
heads
55
5.1.2 Trailer Control Module TrCM
56
5.1.3 Trailer Control Module TrCM+ 59
5.1.4 Brake lining wear sensoring
63
5.2 Air suspension
64
5.2.1 Standard air suspension valve
65
5.2.2 Level adjustable air suspension valve
68
5.2.3 Air suspension valve with zero point
70
adjustment
5.2.4
COLAS
®
+ 72
5.2.5
ILAS
®
-E 75
5.2.6
Shut-off
cock
77
5.2.7 3/2-ways magnetic valve
78
5.2.8 Steering axle lock application
79
5.3 Soft Docking
80
6 Hazardous Goods / ADR Installations
87
7 Programming
89
8 System diagnostics
8.1
System
diagnostics
91
8.1.1
Warning
lamp
92
8.1.2 System check procedure
92
8.1.3 Power up ECO Tronic EBS
93
8.1.4 Other errors shown by the warning lamp
93
8.2 Diagnostic Trouble Codes (DTC)
94
9 Recommended maintenance schedule
97
Содержание ECO Tronic EBS
Страница 2: ...2 BPW Operating and Installation Instructions...
Страница 47: ...47...
Страница 90: ...90...
Страница 98: ...98 Notice...
Страница 99: ...99...