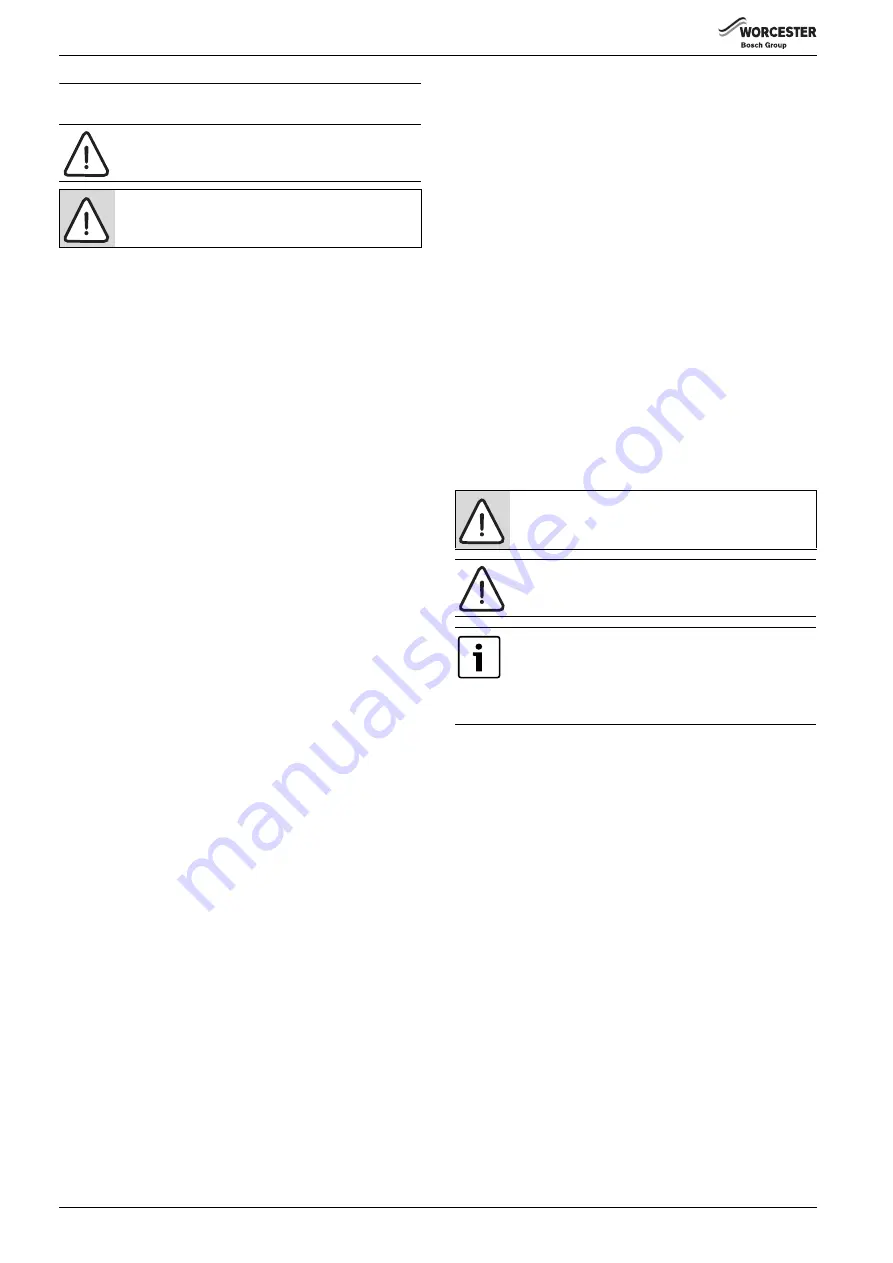
PRE-INSTALLATION
6 720 821 670 (2018/06)
14
4
PRE-INSTALLATION
4.1
MAINS SUPPLY
4.1.1
ELECTRICAL SUPPLY
• Supply: 230V - 50 Hz, 140 Watts
• Cable: PVC insulated 0.75mm
2
(24 x 0.2mm) temp. rated to 90 °C.
• External 3A fuse to BS1362.
• The appliance must be earthed.
• Do not connected the appliance to a 3 phase supply.
• IP20.
• Wiring must comply with the latest edition of BS 7671 (IET wiring
regulations).
4.1.2
GAS SUPPLY
To ensure that the equipment is in good working order and can meet the
gas flow and pressure requirements, in addition to the demand from any
other appliance being served, the following applies:
• Appliances using Natural Gas (NG) must be connected to a governed
meter.
• Liquid Petroleum Gas (LPG) must be connected to a regulator.
• Installation and connection of the gas supply to the appliance must be
in accordance with BS6891.
• Gas pipe sizing should be calculated to ensure no more than the
permitted mbar drop between the meter/governor to the appliance
inlet. (
Commissioning section).
• The meter or regulator and pipe work to the meter must be checked,
preferably by the gas supplier.
4.2
WATER SYSTEMS AND PIPE WORK
PLASTIC PIPE WORK:
• Any plastic pipe work must have a polymeric barrier with 600mm
(minimum) length of copper pipe connected to the appliance.
• Plastic pipe work used for underfloor heating must be correctly
controlled with a thermostatic blending valve limiting the temperature
of the circuits to approximately 50 °C.
PRIMARY SYSTEMS CONNECTIONS/VALVES:
• All system connections, taps and mixing valves must be capable of
sustaining a pressure up to 3 bar.
• Radiator valves should conform to BS2767:10.
• All other valves should conform to BS1010.
• It is best practice to fit Thermostatic Radiator Valves (TRV's) to all
radiators except the area where the room thermostat is sited which
must be fitted with lockshield valves that are left open.
• If the circulating pump speed is fixed and system circulation can be
significantly adjusted or stopped by TRV's or zone valves, a system
bypass should be installed to give at least a 3 metre circuit when
activated. However; any appliance fitted with a modulating pump
may not require a system bypass.
• A drain cock is required at the lowest point in the system.
• An air vent is required at all high points in the system.
OPEN VENT PRIMARY SYSTEM CONSIDERATIONS:
• The open vent pipe and feed and expansion pipe must rise
continuously from the appliance.
• Close coupled feed and expansion pipe maximum separation of
150mm.
• The feed and expansion cistern must be positioned to provide a
minimum static head of 250mm above the highest point in the
heating system to the water level in the feed and expansion cistern.
• Ensure adequate space is left in the expansion cistern for expansion
of the system water.
• No valve shall be fitted in the open vent pipe or the feed and
expansion pipe.
• The open vent pipe must be at least 22mmØ.
•
Do not use galvanised pipes or radiators
.
SEALED PRIMARY SYSTEM CONSIDERATIONS:
• The CH sealed system must be filled using a WRAS approved filling
loop or comply with figure 3 for system fill.
• An expansion vessel, of a size suitable for the system, must be fitted
as close as possible to the appliance in the central heating return.
• Also fit a pressure gauge, a 3 bar pressure relief valve and stop cock
(fixed cylinder type or sealed system approved connection).
• No valve shall be fitted that can isolate the appliance from the
expansion vessel or pressure relief valve.
• An automatic air vent must be fitted.
•
Do not use galvanised pipes or radiators
.
NOTICE:
All the following Pre-Installation sections must
be read and requirements met before starting appliance
or flue installations.
CAUTION:
Isolate the mains supplies before starting any
work and observe all relevant safety precautions.
NOTICE:
To prevent reverse circulation
▶ The cylinder return must be the last connection on the
common return pipe.
NOTICE:
Artificially softened water must not be used to
fill the central heating system.
Pump speed characteristics
▶ In order to save as much energy as possible and the
minimise the possibility of water circulation noise.
The circulating pump should be selected and
adjusted to suit the system resistance.
Содержание Worcester GREENSTAR 12Ri ErP +
Страница 63: ...6 720 821 670 2018 06 63 Notes ...
Страница 64: ...6 720 821 670 2018 06 64 Notes ...
Страница 65: ...6 720 821 670 2018 06 65 Notes ...