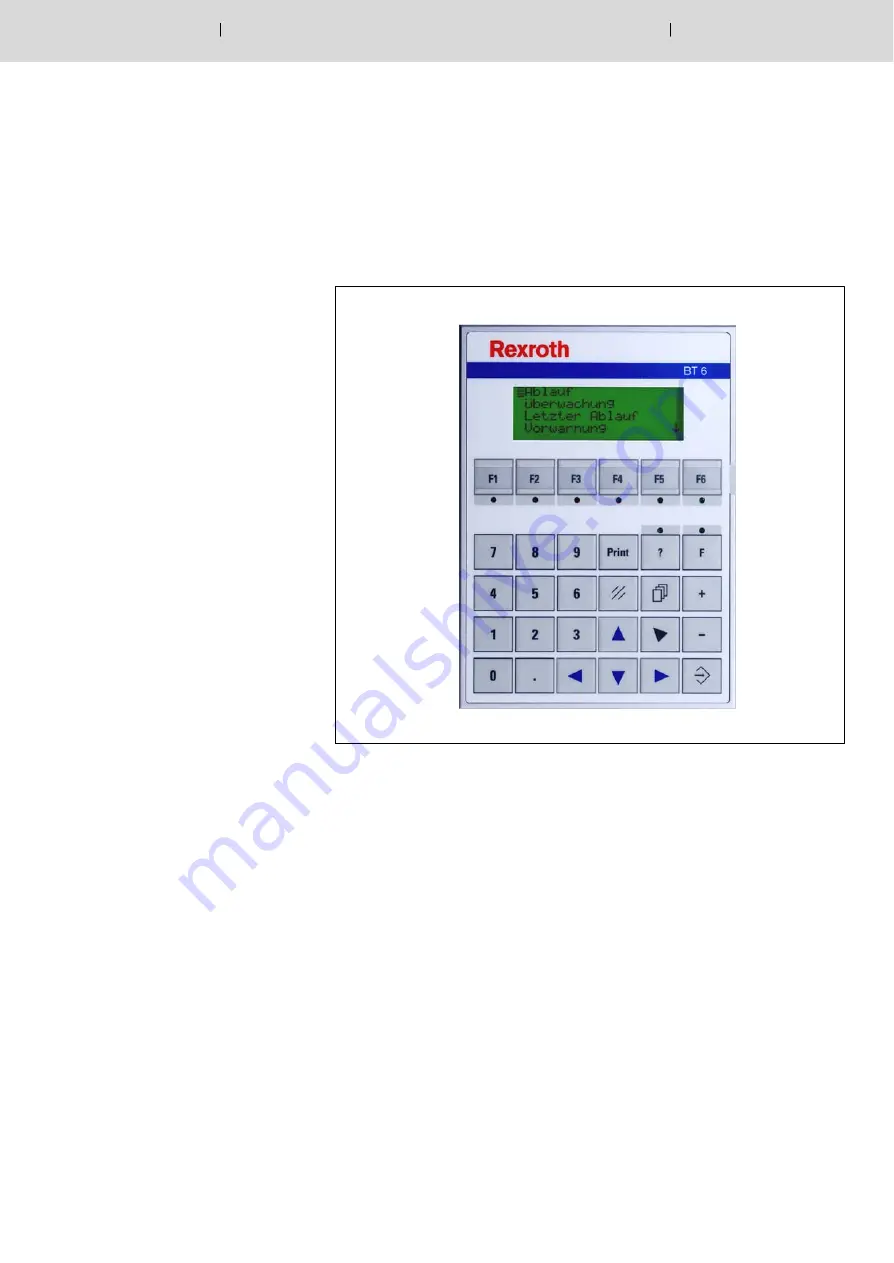
Electric Drives
and Controls
3
−
1
Bosch Rexroth AG
BT 6.00
1070080078 / 03
Assembly and Connection
3
Assembly and Connection
3.1
BT 6.00
−
Built-in unit
3.1.1
Dimensions and assembly
Weight :
ca. 0.6 kg
Location:
desk or hinged frame or control cabi-
net; sealed as per IP 65.
Orientation:
any orientation possible
Degree of protection
(as per EN 60529):
Front face: IP 65
Back face: IP 20
Operating temperature range: 0
_
C to +50
_
C
Storage temperature range:
−
20
_
C to +60
_
C
Climatic category:
Climatic category 3k3 to EN 60721,
condensation is not permitted.
Содержание Rexroth PS5000
Страница 20: ...2 2 Electric Drives and Controls Bosch Rexroth AG BT 6 00 1070080078 03 Overview Notes ...
Страница 30: ...3 10 Electric Drives and Controls Bosch Rexroth AG BT 6 00 1070080078 03 Assembly and Connection Notes ...
Страница 52: ...5 6 Electric Drives and Controls Bosch Rexroth AG BT 6 00 1070080078 03 Maintenance Notes ...