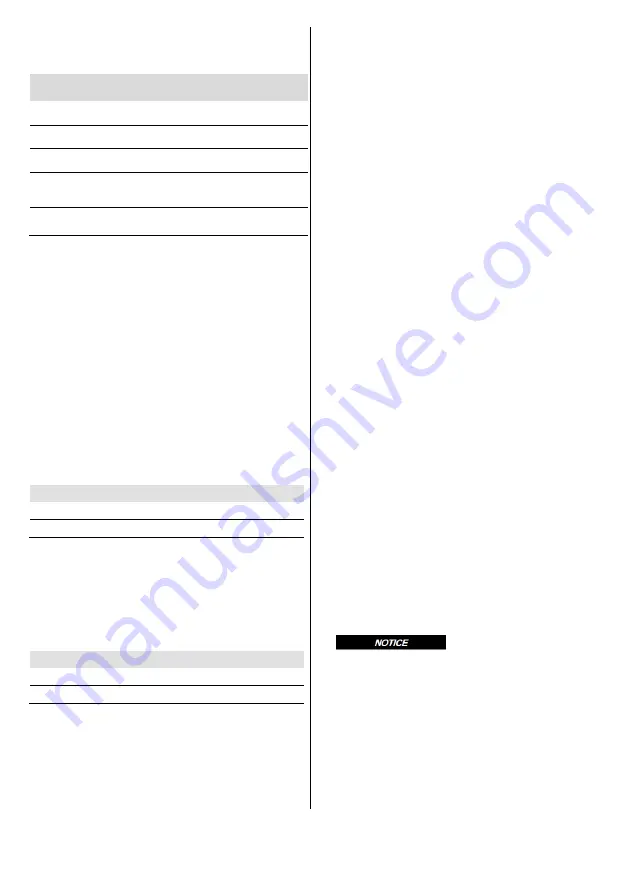
R911336853-07_BAL_DOC
October 21, 2016
Page 5 of 10
9
Interfaces
9.1
Overview
9.2
24V System – Power supply connection
The connector ‘
24V SYSTEM’
connects the
24V power supply to the system housing for all
modules in the module holder.
Connect the minus at the power supply side of
the cable to the housing and/or to protective
earth (if this is not already the case). If the ca-
ble has a shield, connect the shield at the sys-
tem housing side to the shield pin in the con-
nector or the connector housing, and connect
the shield on the other side of the cable to the
housing of the power supply.
Make sure that the power supply cable diame-
ter is suitable for the maximum rated current.
9.3
SE – Service connection
The connector ‘
SE’
are inputs to set the opera-
tion mode of the system to “service mode” and
to execute an as fast as possible shutdown,
called “stop axes”.
9.4
Fan – Fan connection
The connector ‘FAN
’
is a power supply con-
nector for the fan unit that can be installed un-
derneath the module holder for forced cooling.
9.5
MUX – LMS MUX Control connection
These connectors connect the analog output
signals and digital input selection lines to con-
trol the LMS MUX.
•
MUX0 connects analog input 0 and 1.
•
MUX1 connects analog input 2 and 3.
•
MUX2 connects analog input 4 and 5.
•
MUX3 connects analog input 6 and 7.
Always use shielded cables with twisted pairs
for each differential signal. Connect the shield
at the system housing side to the connector
housing. If the equipment on the other end has
metal parts, connect the shield to the equip-
ment housing. If the equipment on the other
end does not have metal parts, connect the
shield to the equipment ground via a 100
Ω
re-
sistor.
Never connect the GND or minus wire of these
signals to other GND connections, otherwise
malfunction of the module is possible.
9.6
Other interfaces
The system housing will always have a Motion
Control Unit (MCU) installed in the leftmost
slot, and a SERCOS III Master module in the
slot at the right side. The MCU has three con-
nections available to connect to other system
housing(s) and/or a PC. Depending on the
MCU type the connection is Ethernet or
IEEE 1394b. On the SERCOS III Master mod-
ule are two RJ45 sockets to connect two SER-
COS III cables to IndraDrives. More infor-
mation can be found in the NYCe 4000 Project
Planning manuals.
10 Installation and Removal
______________________________________
Damage to components
may occur if power is applied during instal-
lation or removal.
•
Make sure power supplies are switched
off before installation or removal of the
system housing.
•
Do not apply power until the system
housing is installed.
______________________________________
Connector data
MC 1,5/ 4-STF-3,5
minimum
maximum
Tightening torque
1,95 lbs*inch (0,22 Nm)
2,21 lbs*inch (0,25 Nm)
Wire diameter
30 AWG (0,14 mm
2
)
14 AWG (1,5 mm
2
)
Connector data
MC 1,5/ 3-STF-3,5
minimum
maximum
Tightening torque
1,95 lbs*inch (0,22 Nm)
2,21 lbs*inch (0,25 Nm)
Wire diameter
30 AWG (0,14 mm
2
)
14 AWG (1,5 mm
2
)
Designation
on base plate
Connection type
Connection
(base plate)
Connection
(cable)
24V System
24V DC system
power supply
3-pin male
Phoenix
MC 1,5/ 3-STF-3,5
SE
Service inputs
4-pin male
Phoenix
MC 1,5/ 4-STF-3,5
Fan
System fan unit
2-pin male
MUX0
MUX1
MUX2
MUX3
LMS MUX
Control
15-pin
Sub-D male
Protective earth
connection
M5 threaded
screw