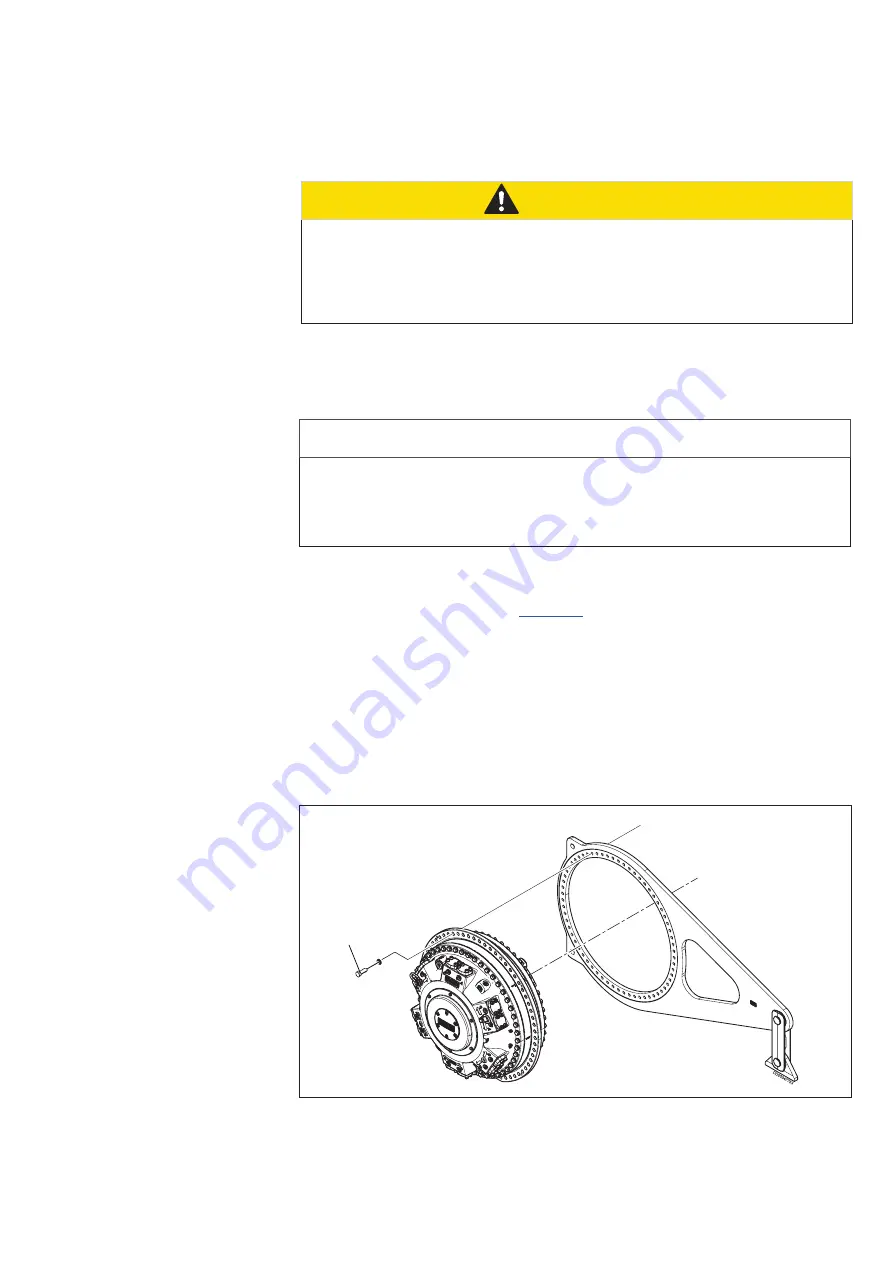
RE 15300-WA, Version 06.2021,
Bosch Rexroth AB
Installation
27/72
Fig. 18: Mounting single ended torque arm TC A 2000 and TC A 4000 for CBm 2000 to CBm 4000
DD00047783
NOTICE
Unauthorized processing of component
Risk of damage equipment
▶ Do not weld, drill, grind or carry out any similar work on the torque arm
without Bosch Rexroth approval.
General information for TC A and DTCBM
The torque arm shall be fitted to the motor before the motor is mounted on the
driven shaft. See also data sheet
1.
Clean the mating surfaces on the torque arm and motor.
2.
Oil the screws (1).
3.
Make sure that the foundation can withstand the forces from the torque arm,
see
,
4.
The motor case must be turned until the drain outlets are positioned according
7.4.6: Draining and venting the motor
.
5.
Mount the torque arm on the motor with the screws and washers.
6.
Tighten the screws (1) to the torque stated in
.
1
7.4 Product installation
Before the installation, drain all fluids from the motor.
CAUTION
Risk for pressurised hydraulic fluid in the motor due to temperature variations!
Risk health hazard, environmental pollution!.
▶ Be careful when opening plugs
▶ Use your personal protective equipment (e.g. safety glasses, safety gloves)
7.4.1 Fitting the torque arm on the motor