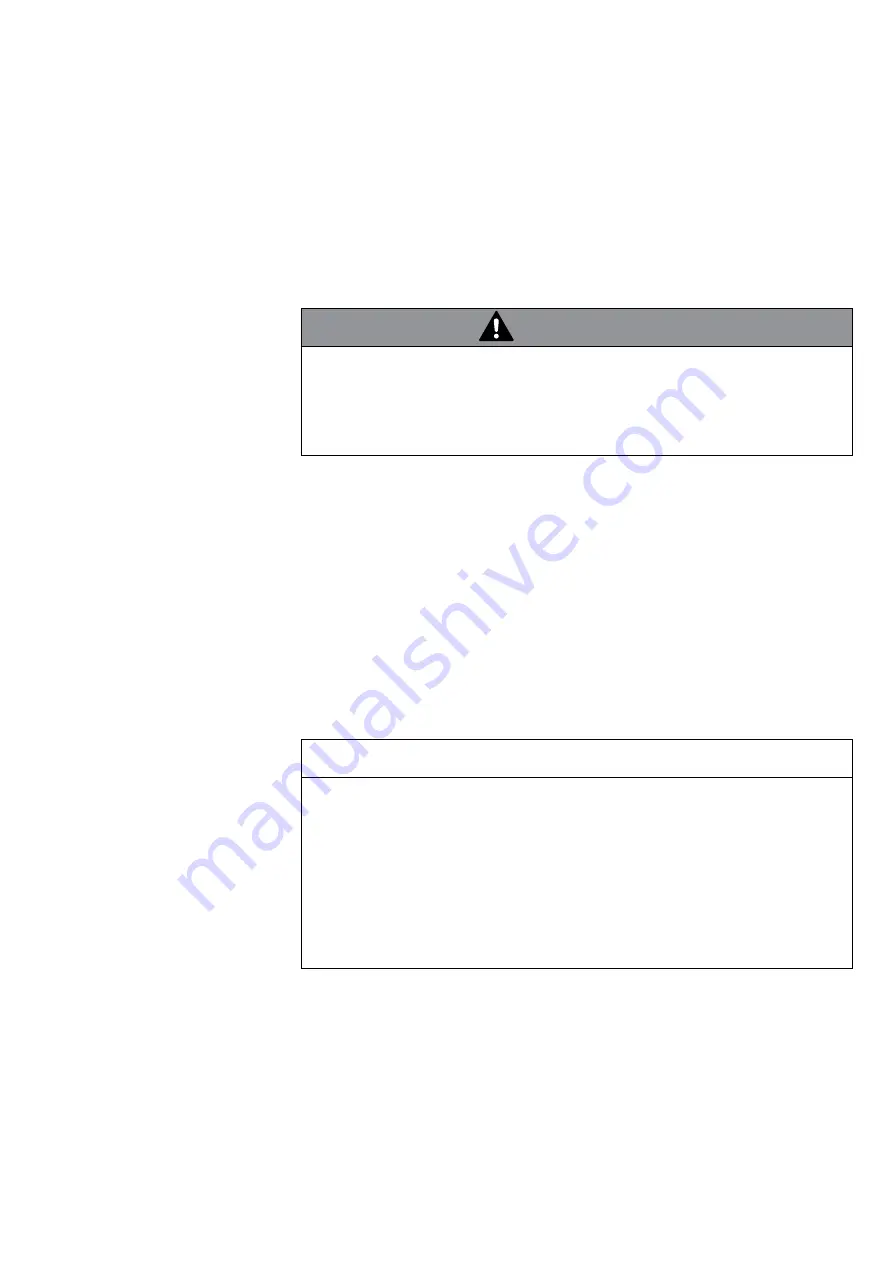
Commissioning 45/60
RE 92701-01-B/04.2018, A10VO, A10VSO Series 31,
Bosch Rexroth AG
4.
Perform a leak test to ensure the hydraulic system is sealed and can withstand
the max. pressure.
5.
Check the suction pressure at port
S
of the axial piston pump at nominal
speed and maximum swivel angle. Refer to data sheet 92701 and 92711 for the
permissible value.
6.
At maximum working pressure, check the case pressure at port
l
, or
l
1
. Refer to
data sheet 92701 and 92711 for the permissible value.
8.1.3 Performing a functional test
wARnInG
Improperly connected axial piston unit!
Mixing up the ports will lead to malfunctions (e.g. lift instead of lower) and
associated hazards to persons and equipment!
▶
Before the functional test, check whether the piping specified in the hydraulic
circuit diagram has been installed.
Once you have tested the hydraulic fluid supply, perform a functional test of
the machine/system. The functional test should be performed according to the
instructions of the machine/system manufacturer.
The axial piston unit is tested for functional capability and performance before
delivery according to the technical data. During commissioning, make sure the axial
piston unit was installed properly in the machine/system.
▶
After starting the drive motor, check in particular the specified pressures,
e.g., working pressure and case pressure.
▶
Perform a leak test without and with load prior to normal operation.
▶
If necessary, disconnect the pressure gage and plug the ports with the specified
threaded plugs.
8.2 Running-in phase
NOTICE
Property damage due to insufficient viscosity!
Elevated hydraulic fluid temperature may excessively reduce viscosity and damage
the product!
▶
Monitor the operating temperature during the running-in phase, e.g. by
measuring the leakage temperature.
▶
Reduce the loading (pressure, rotational speed) of the axial piston unit if
unacceptable operating temperatures and/or viscosities occur.
▶
Excessively high operating temperatures indicate faults that have to be analyzed
and eliminated.
The bearings and sliding surfaces are subject to a running-in phase. The increased
friction at the start of the running-in phase results in increased heat development
which decreases over time. Volumetric and mechanical hydraulic efficiency is also
greater until the running-in phase of about 10 operating hours is concluded.