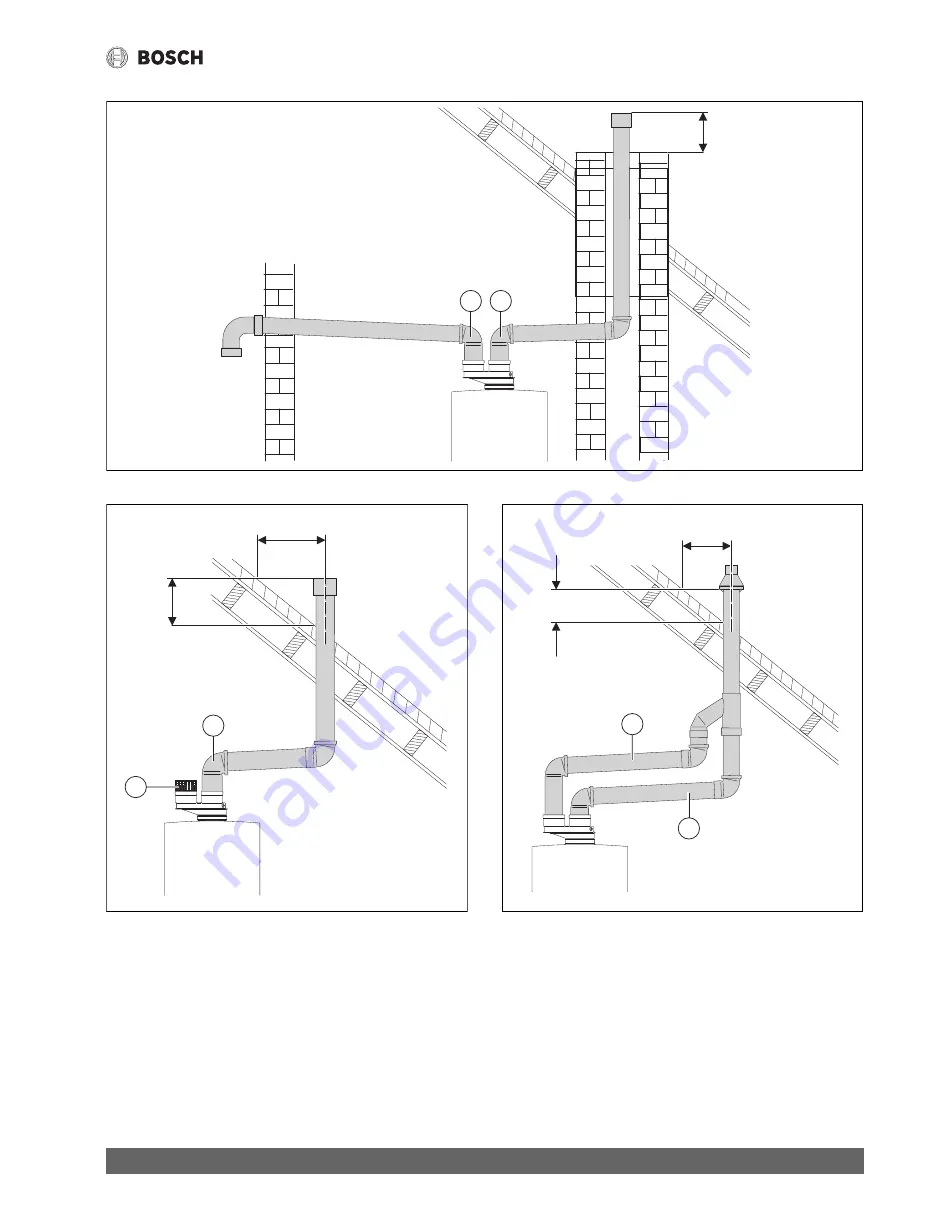
Notes on installation and operation
41
Greenstar – 6721822579 (2021/01)
Fig. 36 Vertical venting system (sealed combustion)
Fig. 37 Vertical venting system (room air only)
Fig. 38 Vertical venting system (sealed combustion)
Key to Fig. 36, Fig. 37 and Fig. 38:
[1]
Intake
[2]
Exhaust
X
Greater than 12 inches (305 mm)
Y
Greater than 12 inches (305 mm)
6 720 641 933-09.2O
Y
1
2
6 720 641 933-07.1O
1
Y
X
2
6 720 641 933-10.1O
1
2
Y
X