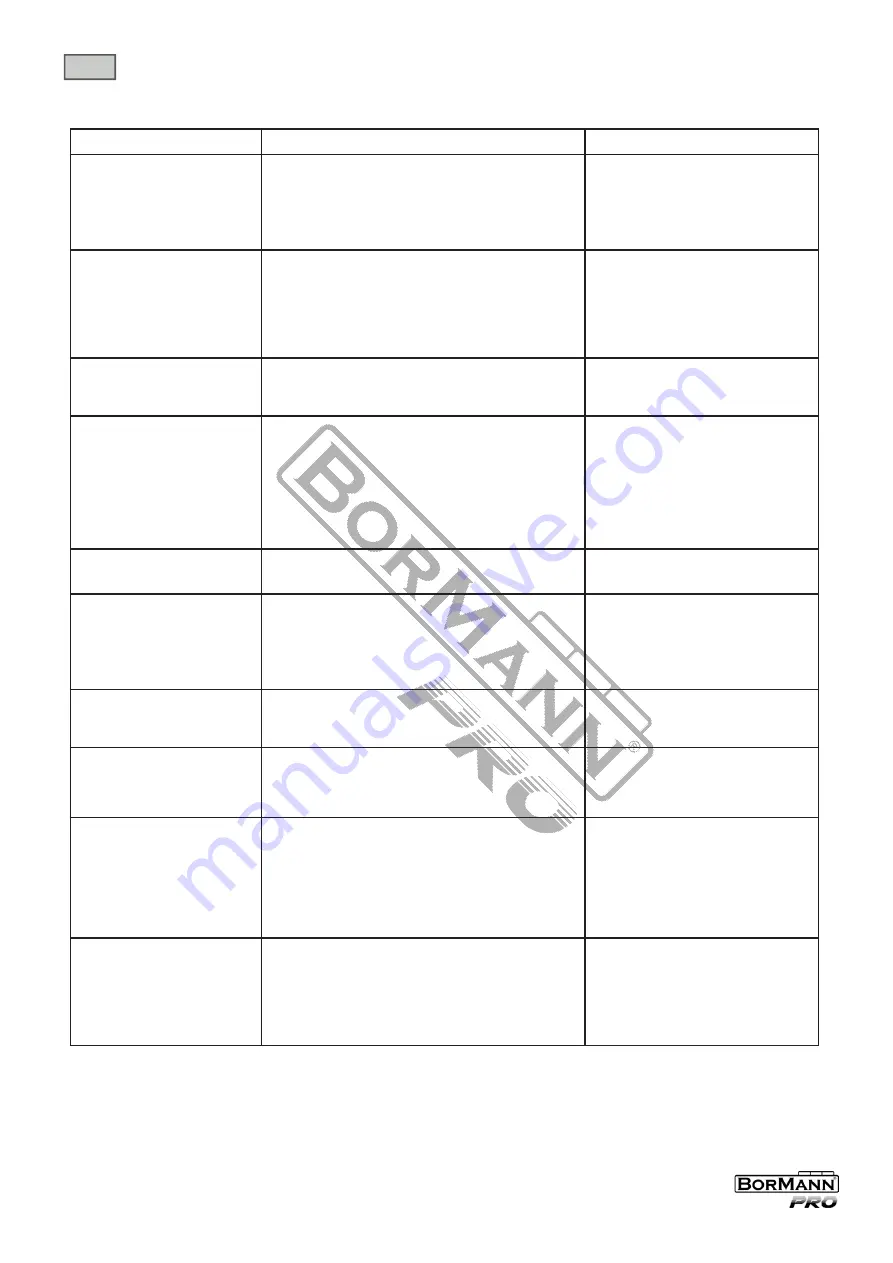
EN
WWW.BORMANNTOOLS.COM
6
Τroubleshooting / Problems
Probable Cause
Remedy
Motor will not start.
1. Low Voltage.
2. Open circuit in motor or loose connections.
3. Blown fuse or breaker.
1. Check power source for proper voltage.
2. Inspect all lead connection on motor for loose or
open connections. (Send for Servicing.)
3. Short circuit. (Send for Servicing.)
4. Improper match between tool
and circuit, fuse or breaker
Motor will not start – fuses or circuit
breakers tripping or blowing.
1. Short circuit in line, cord or plug.
2. Short circuit in motor or loose connections.
3. Incorrect fuses or circuit breakers in power line.
1. Inspect cord or plug for damaged insulation and
shorted wires.
2. Inspect all connections on motor for loose or
shorted terminals and/or worn insulation.
3. Install correct fuses or circuit
breakers or switch tool to an appropriately sized
circuit.
Motor overheats.
1
. Motor overloaded.
2
. Extension cord too long and of insufficient gauge (weight).
1
. Reduce load on motor.
2
. Utilize an extension cord of appropriate gauge
and length or plug tool directly into outlet.
Motor stalls (resulting in blown fuses or
tripped circuit).
1. Short circuit in motor or loose connections.
2. Low voltage.
3. Incorrect fuses or circuit breakers in power line.
4. Motor overload.
1. Inspect connections on motor for loose or
shorted terminals or worn insulation. (Send for
Servicing.)
2. Correct low voltage conditions (for example:
improper extension cord length and/or gauge).
3. Install correct fuses or circuit breakers or plug
tool into an appropriate circuit, matched to an
appropriate fuse or breaker.
4. Reduce the load on the motor.
Machine slows when operating.
1. Feed rate too great.
1. Reduce the rate at which the workpiece is fed
into the working area of the tool (grinding wheel).
Wavy condition on surface of workpiece.
1. Machine vibrating.
2. Workpiece not being held firmly.
3. Wheel face uneven.
4. Wheel is too hard.
1. Ensure machine is securely mounted on a solid
surface.
2. Use a holding device to firmly retain the work
-
piece.
3. Dress the grinding wheel.
4. Use softer wheel, or reduce the feed rate.
Lines on surface of workpiece.
1. Impurity on surface of wheel.
2. Workpiece not being held tightly.
1. Dress the grinding wheel.
2. Use a holding device to more firmly retain the
workpiece.
Burning spots or cracks in the workpiece.
1
. Improper type of grinding wheel.
2
. Improper feed rate.
3
. Coolant required.
1
. Try wheels with softer bond or coarser grit.
2
. Slow down the rate at which the workpiece is fed
into the wheel.
3
. Introduce coolant.
Wheel dulls quickly, grit falls off.
1
. Feed rate is too aggressive.
2
. Wheel is soft.
3
. Wheel diameter too small.
4
. Bad wheel dressing.
5
. Defective wheel bonding.
1
. Decrease feed rate of workpiece into grinding
wheel.
2
. Select a grinding wheel with a harder bond of
material.
3
. Replace wheel.
4
. Dress the wheel.
5
. DO NOT USE – return wheel to point of pur
-
chase.
Wheel clogs and workpiece shows
burn marks.
1. Wheel is too hard.
2
. Feed rate is too slow.
3. Bad wheel dressing.
4. Coolant required.
1. Select a grinding wheel with a softer
bond of material.
2. Increase the feed rate of the workpiece
into the grinding wheel.
3. Dress the wheel.
4. Introduce coolant.