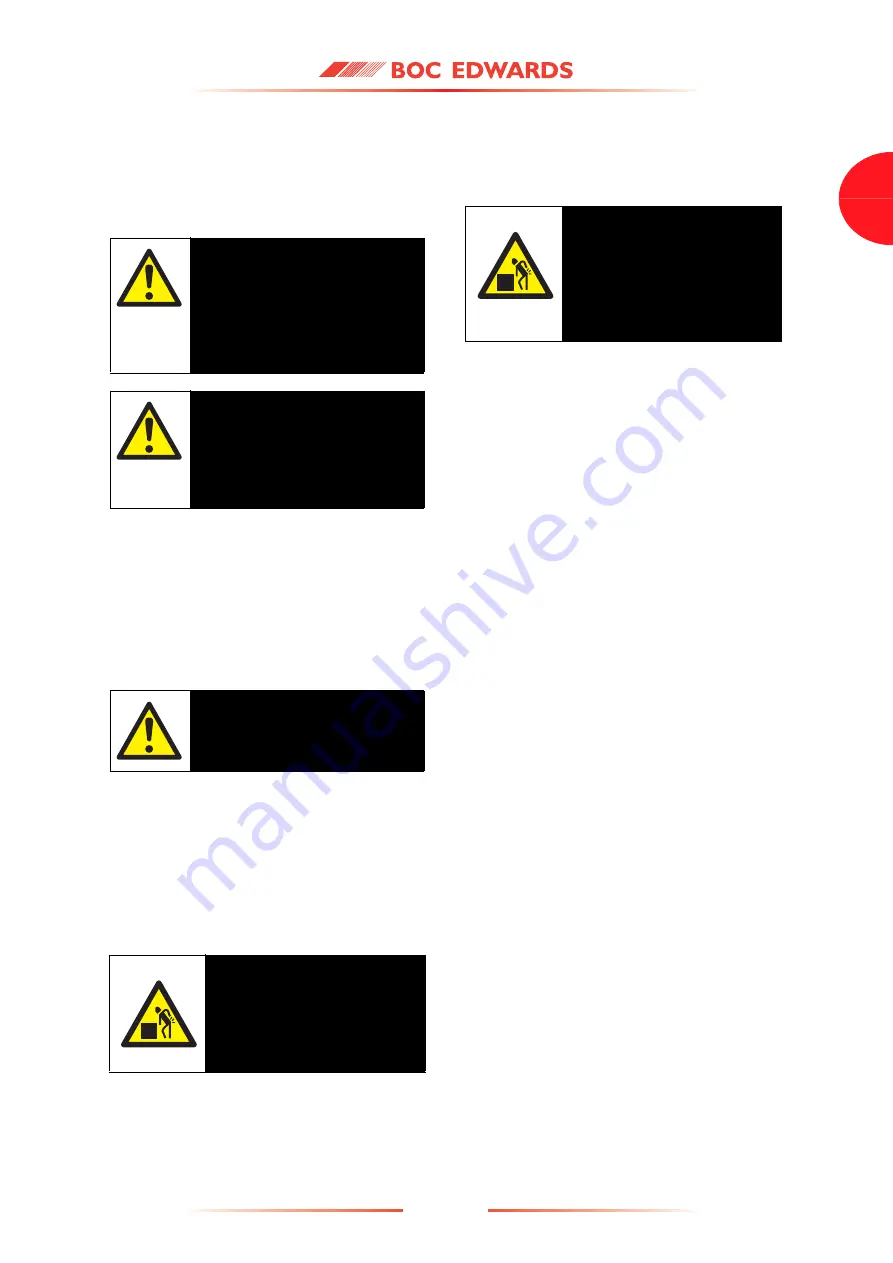
Nov 02
Issue A
XDS Dry Pump
INSTALLATION
PAGE
9
9
3
INSTALLATION
3.1
Safety
You must ensure that the XDS35i pump is suitable
for your application. If you have any doubt about the
suitability of the XDS35i pump for your application,
refer to the BOC Edwards guidelines on vacuum
pump and vacuum system safety (see associated
publications at the end of the contents list at the
front of this manual).
A suitably trained and supervised technician must
perform the installation of the XDS35i pump. Obey
the safety instructions listed below when you install
the XDS pump, especially when you connect the
pump into an existing system. Details of the specific
safety precautions are given at the appropriate point
in the instructions.
• Mechanical lifting equipment should be
attached to the lifting eye on the pump.
WARNING
Obey the safety instructions given
below and take note of appropriate
precautions. If you do not, you can
cause injury to people and damage to
equipment.
WARNING
The BOC Edwards XDS35i pump is
not recommended for pumping
explosive gases or hazardous
substances.
WARNING
Prevent any part of the human body
coming into contact with the vacuum.
WARNING
Use suitable lifting equipment
to move the XDS35i pump.
The mass of the pump is
approximately 48 kg.
• Loose slings should not be used to lift the
XDS35i.
• Wear the appropriate safety clothing when
you come into contact with contaminated
components. Dismantle and clean
contaminated components inside a fume
cupboard.
• Vent and purge your vacuum system before
you start installation work.
• Ensure that the installation technician is
familiar with the safety procedures that relate
to the products handled by the pumping
system.
• Disconnect the other components in the
pumping system from the electrical supply so
that they cannot be operated accidentally.
3.2
System design considerations
Consider the following points when you design your
pumping system:
Use a suitable valve to isolate the pump from your
vacuum system if you need to allow the pump to
warm up before pumping condensable vapours or if
you need to maintain vacuum when the pump is
switched off.
Avoid high levels of heat input into the pump from
the process gases, otherwise the pump may
overheat, and cause the thermal overload device to
open.
If you use the pump in a high ambient temperature
and have a high gas throughput, the temperature of
the pump body may approach 70 ºC and you must
fit suitable guards to prevent contact with hot
surfaces.
WARNING
Take care when moving the pump
into position. The pump's weight
makes it difficult to slide and
movement should be attempted
using two people.
Содержание A730-01-983
Страница 2: ......
Страница 6: ...Issue A Nov 02 XDS Dry Pump PAGE iv iv This page intentionally blank ...
Страница 10: ...Issue A Nov 02 XDS Dry Pump PAGE 4 4 This page intentionally blank ...
Страница 14: ...Issue A Nov 02 XDS Dry Pump PAGE 8 8 This page intentionally blank ...
Страница 16: ...Issue A Nov 02 PAGE 10 XDS Dry Pump INSTALLATION 10 Figure 3 Installation drawing ...
Страница 20: ...Issue A Nov 02 XDS Dry Pump PAGE 14 14 This page intentionally blank ...
Страница 31: ...Nov 02 Issue A XDS Dry Pump MAINTENANCE PAGE 25 25 Figure 10 Tip seal length adjustment 1 Tip seals trim point ...
Страница 34: ...Issue A Nov 02 XDS Dry Pump PAGE 28 28 This page intentionally blank ...
Страница 36: ...Issue A Nov 02 XDS Dry Pump PAGE 30 30 This page intentionally blank ...
Страница 40: ...Issue A Nov 02 XDS Dry Pump PAGE 34 34 This page intentionally blank ...
Страница 43: ...This page intentionally blank ...