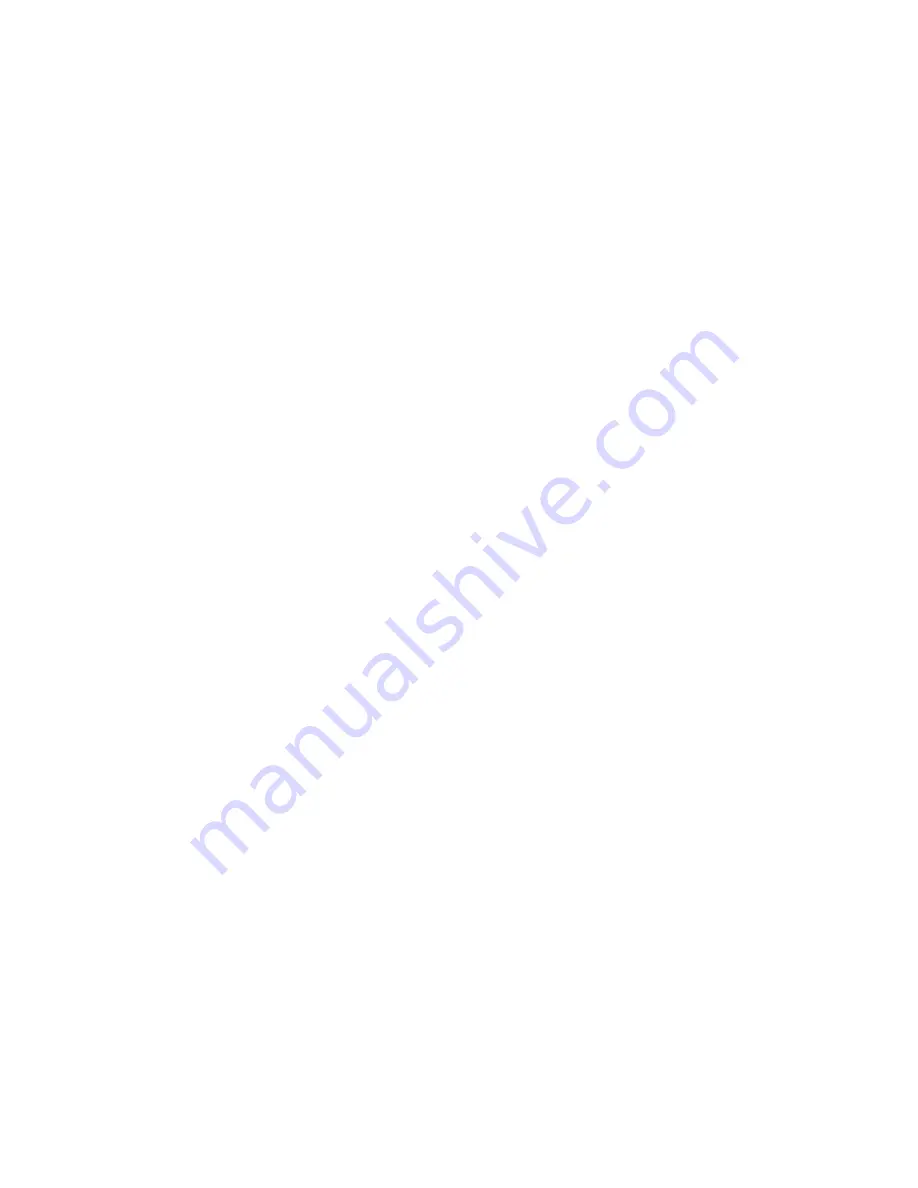
Page 15
To check this pressure:
1. Slide the gas valve switch to the “OFF” position (see
Figure 7).
2. Remove plug on valve marked “OUTLET PRESSURE.”
3. Install a water manometer.
4. Slide the gas valve switch to the “ON” position and
initiate a call for heat. If manifold pressure must be
adjusted, the gas valve has separate adjusting screws
for first stage (LO) and second stage (HI) (see Figure
7). Turn the adjusting screws clockwise to increase
pressure and input; turn counterclockwise to decrease
pressure and input. The pressure regulator adjustment
is sensitive. One turn of the adjusting screw results in
a large change in manifold pressure. Final first-stage
and second-stage manifold pressures must be within
the allowable ranges for the gas being used.
5.
After checking pressure, turn gas off, remove
manometer fitting, and replace pipe plug and regulator
cap.
6. Put furnace in operation and check plug for leaks
using soapy solution.
Burner and Burner Orifice Instructions
To check or change burners or burner orifices:
1.
Close the main manual gas shutoff valve and turn off
all power to unit.
2. Remove the burner access panel.
3. Disconnect the union in the gas supply line upstream
of the gas valve and downstream of the manual shutoff
valve.
4. Label wires going to the gas valve, then disconnect
the wires.
5.
To change orifice:
a. Remove screws that fasten the manifold to the
burner box assembly and remove the manifold.
b.
Remove the orifices, then install replacement
orifices.
c. To reassemble: Reverse above steps, making
sure orifices are inserted into the orifice holders
on the back end of the burners, and that burners
are level and centered on each burner opening in
the vest panel.
6. To remove or service burners:
a. Label and disconnect the wires to the rollout switch
and disconnect the igniter and flame sensor leads
at the ignition control.
b. Remove the screws that secure the burner box
assembly to the vest panel and remove the
assembly from the unit.
c. Remove the screws that fasten the burner rack
and bottom shield assembly to the burner box.
Burners are now accessible for removal.
Operation
Blower Control
Units are equipped with a variable speed motor that is
capable of maintaining a specified CFM throughout the
external static range. A particular CFM can be obtained by
positioning jumpers (COOL, HEAT, and ADJUST) on the
blower control. The HEAT and COOL jumpers are labeled
A, B, C and D. Each of the numbers corresponds with an
air volume (CFM) setting. The ADJUST jumper is labeled
Test, -, +, and Norm. The + and - pin settings are used to
add or subtract a percentage of the CFM selected. The
Test jumper is used to operate the motor in the test mode.
Figure 8 shows the blower control.
The CFM LED located on the blower control flashes one
time per 100 cfm to indicate selected blower speed. For
example, if the unit is operating at 1200 CFM, CFM LED
will flash 12 times. If the CFM is 1150, CFM LED will flash
11 full times plus one fast or half flash. At times the light may
appear to flicker or glow. This takes place when the control
is communicating with the motor between cycles. This is
normal operation.Read through the jumper settings section
before adjusting the jumper to obtain the appropriate blower
speed.To change jumper positions, gently pull the jumper
off the pins and place it on the desired set of pins. The
following section outlines the different jumper selections
available and conditions associated with each one. Refer
to Figure 8.
From the engineering handbook and/or specification
sheet, determine which row most closely matches the
desired CFM. Once a specific row has been chosen (+,
NORMAL, or -), CFM volumes from other rows cannot be
used. Below are descriptions of the jumper selections.
The variable speed motor slowly ramps up to and down
from the selected air flow during both cooling and heating
demand. This minimizes noise and eliminates the initial
blast of air when the blower is initially energized.
ADJUST
The ADJUST pins allow the motor to run at normal speed,
approximately 15 percent higher, or approximately 15
percent lower than normal speed.
The TEST pin is available to bypass the blower control
and run the motor at approximately 70 percent to make
sure that the motor is operational. This is used mainly in
troubleshooting. The G terminal must be energized for the
motor to run.
d. To Reassemble: Reverse above steps.
7. After reassembly of all parts is complete and all wires
are reconnected, open the main manual gas shutoff
valve; check for and correct any gas leaks. Turn
electrical power on, initiate a call for heat, and check
for proper burner operation.
8. Install burner access panel.