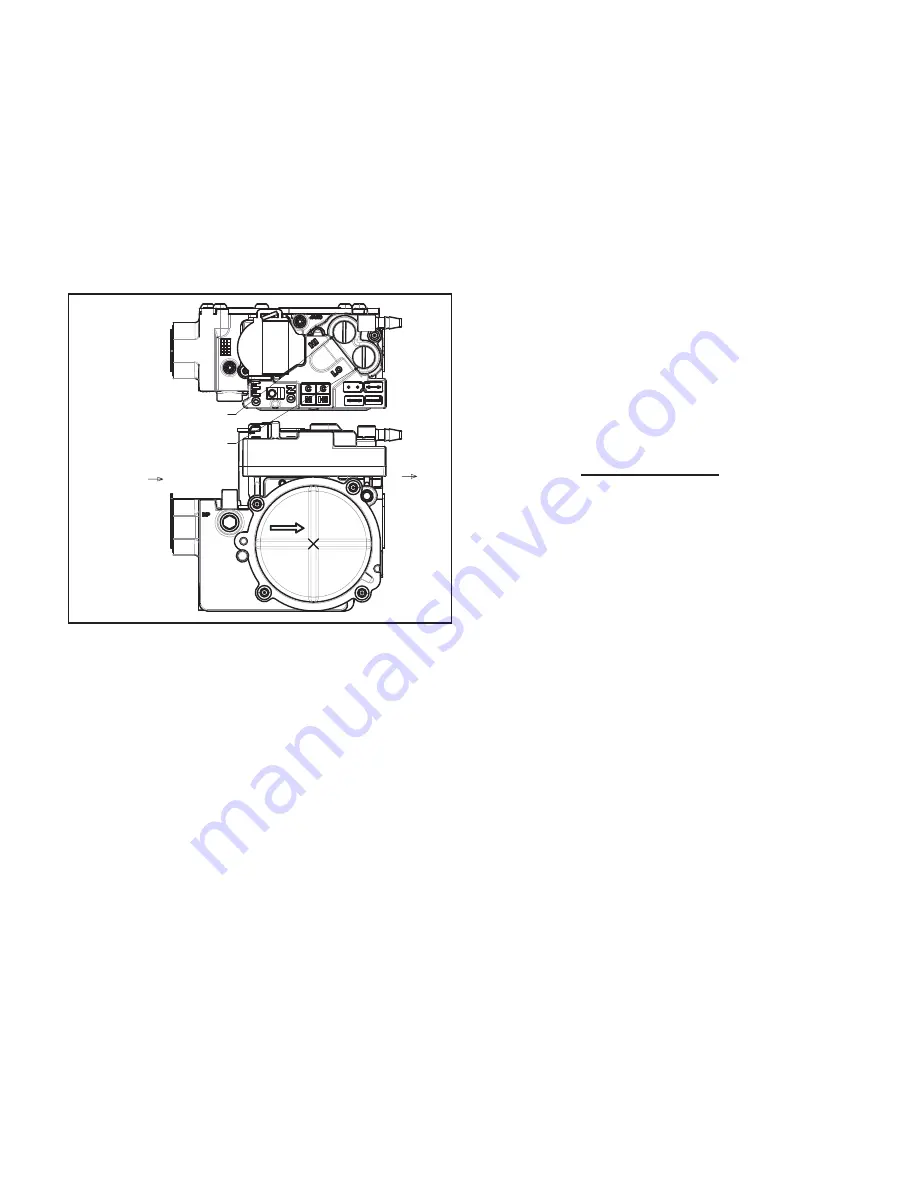
Page 14
3. Slide the gas valve switch to the “ON” position (see
Figure 7).
4. Turn on electrical power to the unit.
5. Set the room thermostat to the desired temperature.
(If the thermostat “set” temperature is above room
temperature after the pre-purge time expires, main
burners will light.)
To Shut Down Main Burners
1.
Turn off electrical power to unit.
2. Slide the gas valve switch to the “OFF” position (see
Figure 7).
Figure 7. Gas Valve
Post-Start Check List
After the entire control circuit has been energized and the
heating section is operating, make the following checks:
1. Check for gas leaks, using soapy solution, in the unit
piping as well as the supply piping.
2. Check for correct manifold gas pressures (see Manifold
Gas Pressure Adjustment Regulator sections).
3. Check the supply gas pressure. It must be within the
limits shown on the rating plate. Supply pressure
should be checked with all gas appliances in the
building at full fire. At no time should the standby gas
pressure exceed 13” w.c., nor the operation pressure
drop below 5” w.c. for natural gas units or 11” w.c. for
propane gas. If gas pressure is outside these limits,
contact the gas supplier for corrective action.
4.
Adjust temperature rise to the range specified on the
rating plate.
Manifold Gas Pressure Adjustment Regulator –
Natural Gas
For purpose of input adjustment, the minimum permissible
gas supply pressure is 5” w.c. for natural gas.
Gas input must never exceed the input capacity shown on
the rating plate.
Units fueled by natural gas are rated for
manifold pressures of 2.0 inches W.C. for first stage
and 3.5 inches W.C. for second stage.
The manifold pressure can be measured by shutting off
the gas, removing the pipe plug in the downstream side
of the gas valve, and connecting a water manometer
or gauge.
Under no circumstances should the final
manifold pressure vary more than 0.3” w.c. from the
above specified pressures.
To adjust the regulator, turn
the adjusting screw on the regulator clockwise to increase
pressure and input or counterclockwise to decrease
pressure and input. See Figure 7 to assist in locating the
regulator on the gas valve.
Check the furnace rate by observing the gas meter, making
sure all other gas appliances are turned off. The test hand
on the meter should be timed for at least one revolution,
noting the number of seconds per revolution. The heating
value of the gas can be obtained from the local utility.
BTU/HR
Input
=
Cubic Feet per
Revolution
x 3600 x Heating
Value
# Seconds per
Revolution
Example
: By actual measurement, it takes 38 seconds for
the hand on the 1-cubic foot dial to make a revolution with
a 100,000 BTU/HR furnace running. The result is 99,750
BTU/HR, which is close to the 100,000 BTU/HR rating of
the furnace.
Manifold Gas Pressure Adjustment Regulator –
LP/Propane Gas
LP/propane units require a LPG regulator on both the gas
valve and on the LP/propane tank.
IMPORTANT
:
For purpose of input adjustment, the
minimum permissible gas supply pressure (inlet side of
gas valve) is 11” w.c. for LP/propane.
If at any time ignition is slow and burner does not seem to
be operating correctly, check manifold pressure (outlet side
of the gas valve).
It should be 10” to 10.5” w.c. pressure
for LP/propane.
Units fueled by LP/propane gas are rated for manifold
pressures of 5.6 inches W.C. for first stage and 10.0
inches
High Altitude
The input rate shown on the rating plate is for elevations
up to 2000 feet. For elevations from 2001 to 4500 feet,
the input rate is reduced by 5%. For elevations above
4500 feet, refer to the National Fuel Gas Code Z223.1
(latest edition) or the Canadian Installation Codes CAN/
CGA-B149.1 & B149.2 for further details.