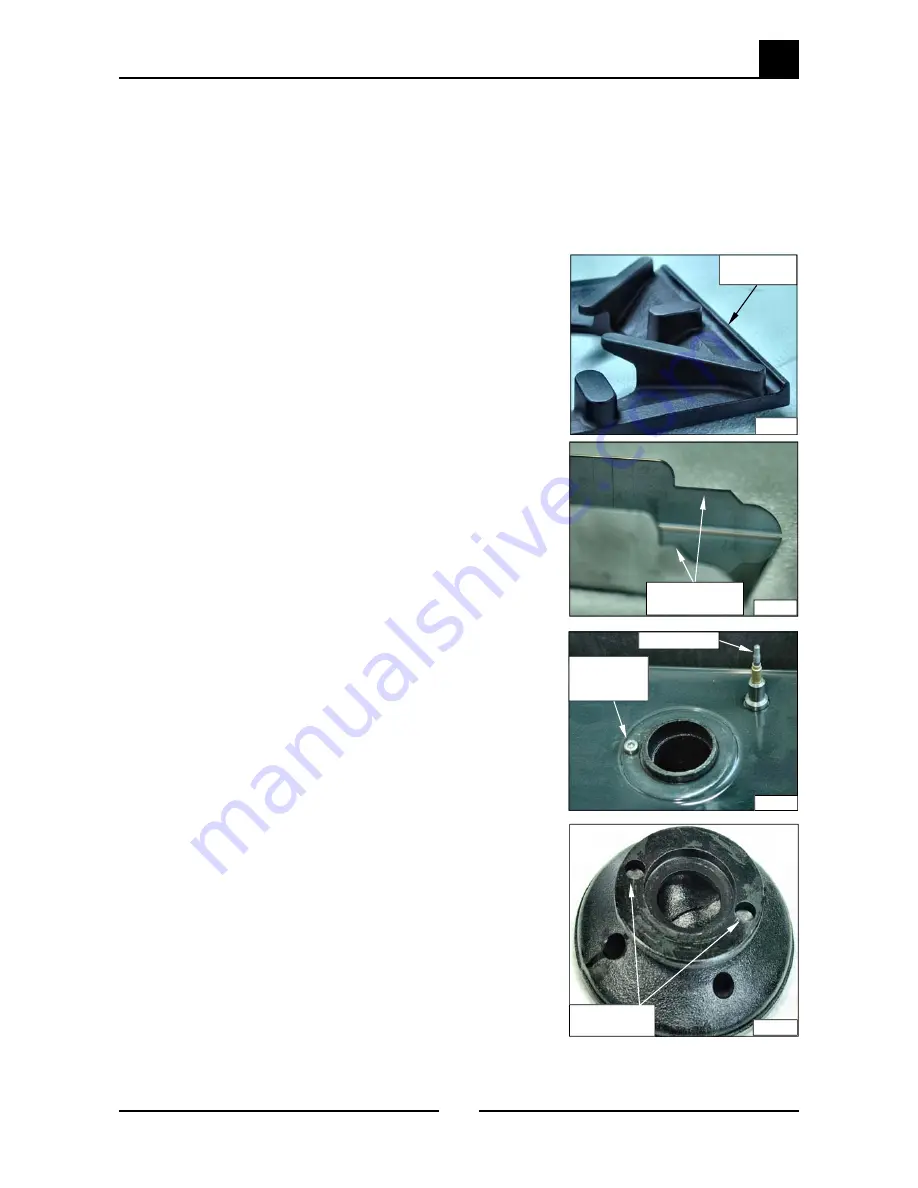
A
Appendix A: Gas Type Conversion
43
© Moffat Ltd, January 2007
Revision 1/
Blue Seal Evolution series G51 Gas Cooktops
Gas type conversion procedure
NOTE:
•
These conversions should only be carried out by qualified persons. All connections must
be checked for leaks before re-commissioning the appliance.
•
For all relevant gas specifications refer to the table at the end of this section.
Open Burners ('F' - Flame Failure Option)
1.
Turn ‘OFF’ the gas supply at the main supply.
2.
Remove the trivets from the top of the appliance, taking note
that the trivets are manufactured with a lip on one edge, the
lip must always be fitted to the outer edge (front and back) of
the cook top.
3.
Remove the burner caps and burner bowls (these are a loose
fit to the manifold) from the top of the gas manifold, taking
care not to damage the thermocouples fitted through the
manifold splash guard.
4.
Remove all the trivet supports from the top of the appliance.
Note the orientation of the trivet supports when removing.
The trivet support front end side rail profiles are different from
the rear end side rail profiles.
5.
Remove the splash guards covering the burner manifolds by
unscrewing the two allan headed screws. Carefully remove
the splash guards taking care not to damage the
thermocouples protruding through the splash guard.
6.
Unscrew and remove the injectors (½ A/F) from the gas
cocks.
7.
Determine the correct injector sizes for the corresponding gas
from the rating plate.
•
For Bench, Cabinet Base and Leg Stand Models, the
Rating Plate is attached to the underside of the right hand
side, front Cook Top lower trim.
•
For the Refrigerated Base Model, the Rating Plate is
located inside the right hand front panel and can be viewed
through the upper grille. Refer to the ‘Gas Connection’
section and the ‘Dimensions’ section.
8.
Replace with the correct size injectors. Refer to the ‘Gas
Specifications table’ at the end of this section, for correct
injector sizes.
9.
Refit the splash guards over the gas cocks taking care not to
damage the thermocouples and secure in position with the 2
allan headed screws. (Refer to Fig 14).
10. Refit the burner caps and burner bowls onto the manifolds
protruding through the splash guards, taking care not to
damage the thermocouple which is close to the manifold.
Take note that the base part of the burner bowl has 2 locating
holes drilled into the base flange, these are to locate the
burner bowl onto the allen headed screws that secure the
splash guard to the gas manifold. (Refer to Fig 15).
11. Turn on the gas supply at the mains, re-light the burners and
check the flame size on the simmer (LOW) position.
NOTE: The right hand gas control valve supplies the rear burner and the left hand gas control valve
supplies the front burner.
Notice Difference
in Edge Profiles
Splash Guard
Retaining Cap
Screw
Thermocouple
Fig 12
Notice Lip on
Trivet Edge
Fig 13
Fig 14
Burner Bowl
Locating Holes
Fig 15