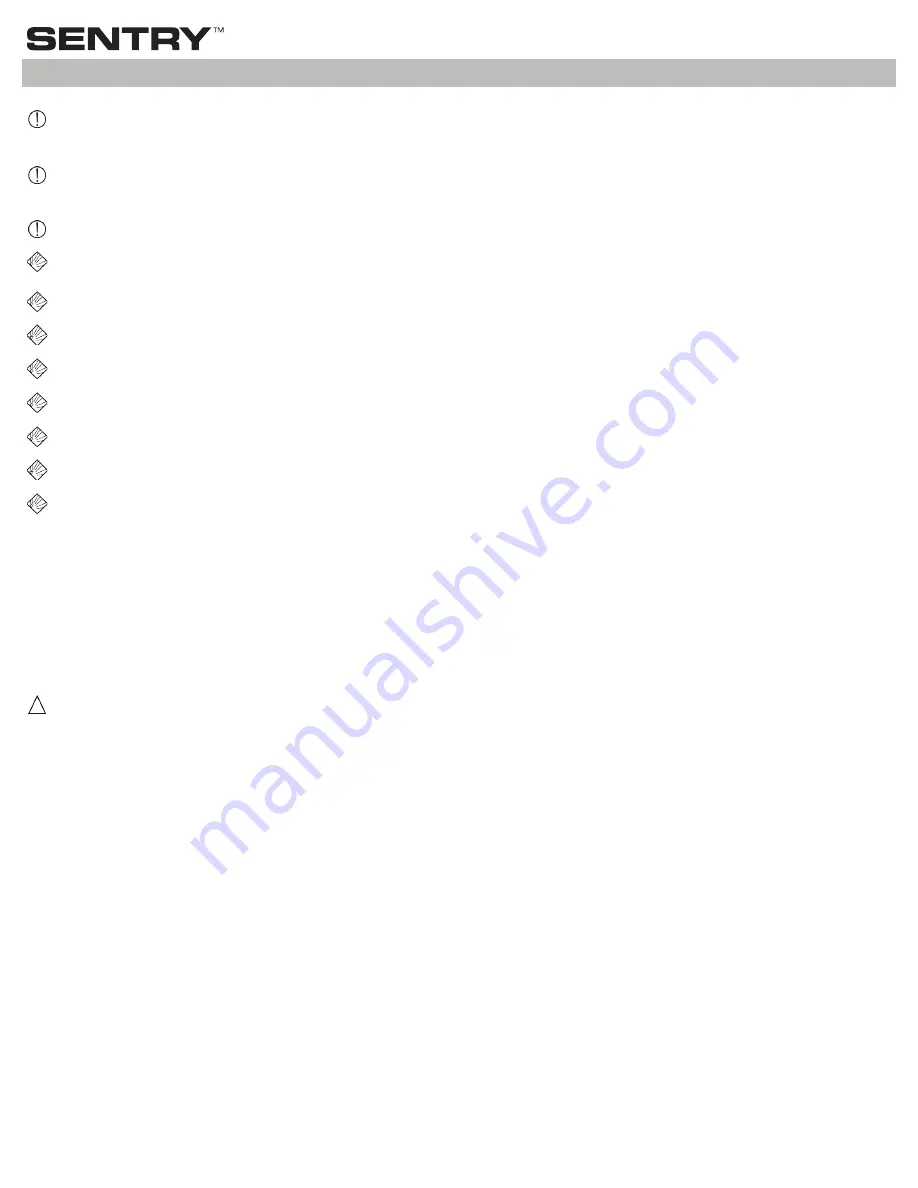
5
BLACOH Industries
Pre-Charge Notes
Pre-charge pressure should be checked at least monthly as gas molecules will diffuse through bladders/bellows, the speed of which depends
on the material, temperature and pressure. Checks must occur when no system pressure is present or inaccurate readings will be recorded.
If temperature is above 72°F (22°C) and/or pressure is over 300 psi (20.6 bar), checks should be performed more frequently.
To prevent
pre-charge loss through the charging valve, always replace the charging valve cap after charging.
A proper gas charge is the key to
dampener effectiveness and bladder/bellows life.
Charging Instructions
Dampener can only be properly charged when fluid pressure is zero.
1.
Point dampener charging valve in a safe direction. To verify dampener is not pressurized, remove charging valve cap and use a suitable
wrench to slowly open charging valve by turning valve opening nut counterclockwise (Figure 1).
2. Use a BLACOH high pressure XP Charging Kit or equivalent to charge dampener.
Note:
The source of Nitrogen (tank or bottle) must be
equipped with a regulator set at no more than the maximum allowable working pressure (MAWP) specified on dampener.
3. Close valve at Nitrogen source and thread charging hose connection securely to dampener charging valve. Make sure charging valve is
completely open by turning valve opening nut counterclockwise as far as it will go (Figure 1).
4. Slowly open valve at Nitrogen source and charge dampener to 100 psi (6.8 bar). Inspect charging valve and cap thread area for leaks by
spraying with a solution of soap and water. If any leaks are observed, remove pressure from dampener by slowly loosening charging hose
connection to charging valve or, if used, slowly open bleed valve on BLACOH charging hose manifold. Determine cause of leaks and repair
before recharging (see
Pressure Seal Checks
section below).
5.
Slowly increase Nitrogen pressure in dampener until desired pressure, usually 80% of system pressure, is stabilized on charging hose gauge.
6. Close charging valve completely by turning valve opening nut clockwise approximately 4-5 revolutions. Use a suitable wrench to tighten
firmly.
7. Turn off valve at Nitrogen source and slowly loosen charging hose connection to charging valve or, if used, slowly open bleed valve on
BLACOH charging hose manifold. Wait to let all pressure in charging hose escape. It will take up to one minute to release all pressure in
charging hose.
8. Remove charging hose connection and reinstall charging valve cap tightly on charging valve. (The charging valve cap seals the charging
valve to prevent slow, long term pressure loss.)
Installation & Operation Instructions
XP High Pressure models are proof tested to 1.3 times maximum allowable working pressure (MAWP). All pressure is removed
from dampener prior to shipment; however, standard models do not have a factory installed pressure gauge – always assume
dampener is pressurized.
IMPORTANT! High pressure is dangerous. Only qualified persons are allowed to charge, install and repair high pressure
models.
Turn pump off and remove all pressure from system prior to dampener installation.
Remove all pressure from dampener AND pumping system before disassembly, removal or maintenance.
Use clean dry Nitrogen to charge dampener.
DO NOT USE OXYGEN.
DO NOT exceed maximum allowable working pressure (MAWP) specified on dampener.
Always wear safety glasses and other appropriate safety equipment when installing, charging or repairing dampener.
Read and observe all safety warnings and instructions in this Manual before installation, operation or repair.
Before performing a system pressure test, dampener must be charged with 80% of system test pressure to avoid possible
damage to bladder/bellows.
Only charging systems with components designed to be used at or above the maximum allowable working pressure (MAWP)
specified on dampener can be used for charging. The source of Nitrogen (tank or bottle) must be equipped with a regulator set
at no more than the MAWP specified on dampener.
ATEX models must be grounded (earthed) before operation.