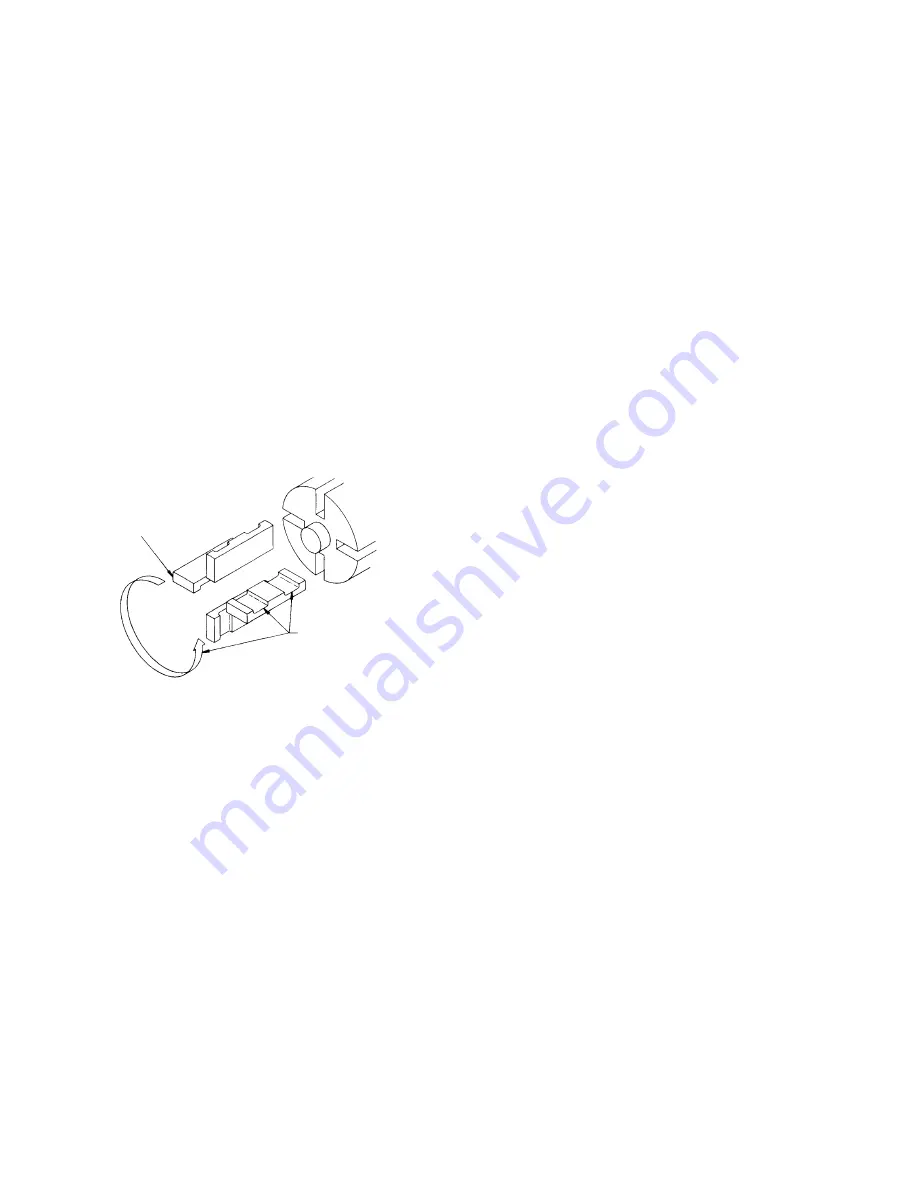
105-A00 Page 7/12
MAINTENANCE
VANE REPLACEMENT
NOTICE:
MAINTENANCE SHALL BE PERFORMED BY QUALIFIED
TECHNICIANS ONLY. FOLLOWING THE APPROPRIATE
PROCEDURES AND WARNINGS AS PRESENTED IN
MANUAL.
1. Relieve pressure, drain and flush the pump and system
as required.
2. Remove the head assembly from the outboard (non-
driven) side of the pump according to steps 4 - 9 in the
"Pump Disassembly" section of this manual.
3. Turn the shaft by hand until a vane (14) comes to the top
(12 o'clock) position of the rotor. Remove the vane.
4. Install a new vane (14), ensuring that the rounded edge
is UP, and the relief grooves are facing towards the
direction of rotation. See Figure 5.
5. Repeat steps 3 and 4 until all vanes have been replaced.
NOTE: The standard rotor & shaft has eight vanes and
no push rods. The optional rotor & shaft has four vanes
and two push rods.
6. Reassemble the pump according to the "Pump
Assembly." section of this manual.
ROUNDED EDGE OUT
RELIEF GROOVES
FACE IN DIRECTION
OF ROTATION
Figure 5 – Vane Replacement
PUMP DISASSEMBLY
NOTICE:
FOLLOW ALL HAZARD WARNINGS AND
INSTRUCTIONS PROVIDED IN THE “MAINTENANCE”
SECTION OF THIS MANUAL.
NOTE:
The numbers in parentheses following individual
parts indicate reference numbers on the Pump Parts List.
1. Relieve pressure, drain and flush the pump and system
as required.
2. Starting on the
inboard
(driven) end of the pump, clean
the pump shaft thoroughly, making sure the shaft is free
of nicks and burrs. This will prevent damage to the
mechanical seal when the inboard head assembly is
removed.
3. Remove the inboard bearing cover capscrews (28) and
slide the inboard bearing cover (27) and gasket (26) off
the shaft. Discard the bearing cover gasket.
NOTE: On flange mounted pumps, a bracket mount
(108) takes the place of the inboard bearing cover. To
disassemble, take apart the coupling (34) and remove
the mounting screws (28A). The bracket and gasket (26)
can then be removed from the head (20).
4. Remove the outboard bearing cover capscrews (28) and
slide the outboard bearing cover (27A) and gasket (26) off
the shaft. Discard the bearing cover gasket.
5. To remove locknuts and lockwashers (24A and 24B):
a. Bend up the engaged lockwasher tang and rotate the
locknut counterclockwise to remove it from the shaft
b. Slide the lockwasher (24B) off the shaft. Inspect the
lockwasher for damage and replace as required.
c. Repeat steps a and b on the opposite shaft end.
6. Remove the head capscrews (21). Each head (20) has a
threaded jackscrew hole to facilitate removal. Insert a
capscrew (21) into the jackscrew hole to easily remove
head from the casing (12).
NOTE: It is a good practice to
attach pump heads to the same ends they were
removed from.
7. Slide the head (20) off the shaft. The bearing (24),
mechanical seal stationary seat and stationary O-ring
(153A & 153D) will come off with the head assembly.
a. Pull the bearing (24) from the housing in the head.
b. To remove the mechanical seal stationary seat (153A),
use the blunt end of a screw driver to gently push the
backside of the stationary seat from the head. Place a
cloth under the seal to avoid damage. Be careful not to
contact the polished face of the seal during removal.
Remove and discard mechanical seal stationary O-ring.
8. Carefully pull the rotating seal assembly, consisting of seal
jacket (153C), rotating seal face and rotating O-ring (153B
& 153E) from the shaft. Remove and discard the rotating
O-ring (153E).
9. Carefully remove the disc (71) and head O-ring (72).
10. Pull the rotor and shaft (13) from the casing (12). While one
hand is pulling the shaft, the other hand should be cupped
underneath the rotor to prevent the vanes (14) from falling
out. Carefully set the rotor and shaft (13) aside for future
vane replacement and reassembly.
11. Lay the pump flat with the remaining head facing upward to
remove the head assembly, mechanical seal, and disc from
the outboard side of the pump, as instructed in steps 6 - 9
above.
12. If necessary, remove the liner (41) by tapping around the
outside diameter of the liner with a hard wood drift and a
hammer until it is driven from the casing (12).
PARTS REPLACEMENT
1. If any of the O-rings have been removed or disturbed
during disassembly, they be replaced with new O-rings.
2. Excessive or continuous leakage from the tell-tale hole in
the bearing cover may be an indication of a damaged
mechanical seal. If a mechanical seal has been leaking, it is
recommended the entire seal be replaced. Refer to
"General Pump Troubleshooting" for possible causes of
seal leakage.
Содержание XLW1 1/2
Страница 11: ...105 A00 Page 11 12 NOTES...