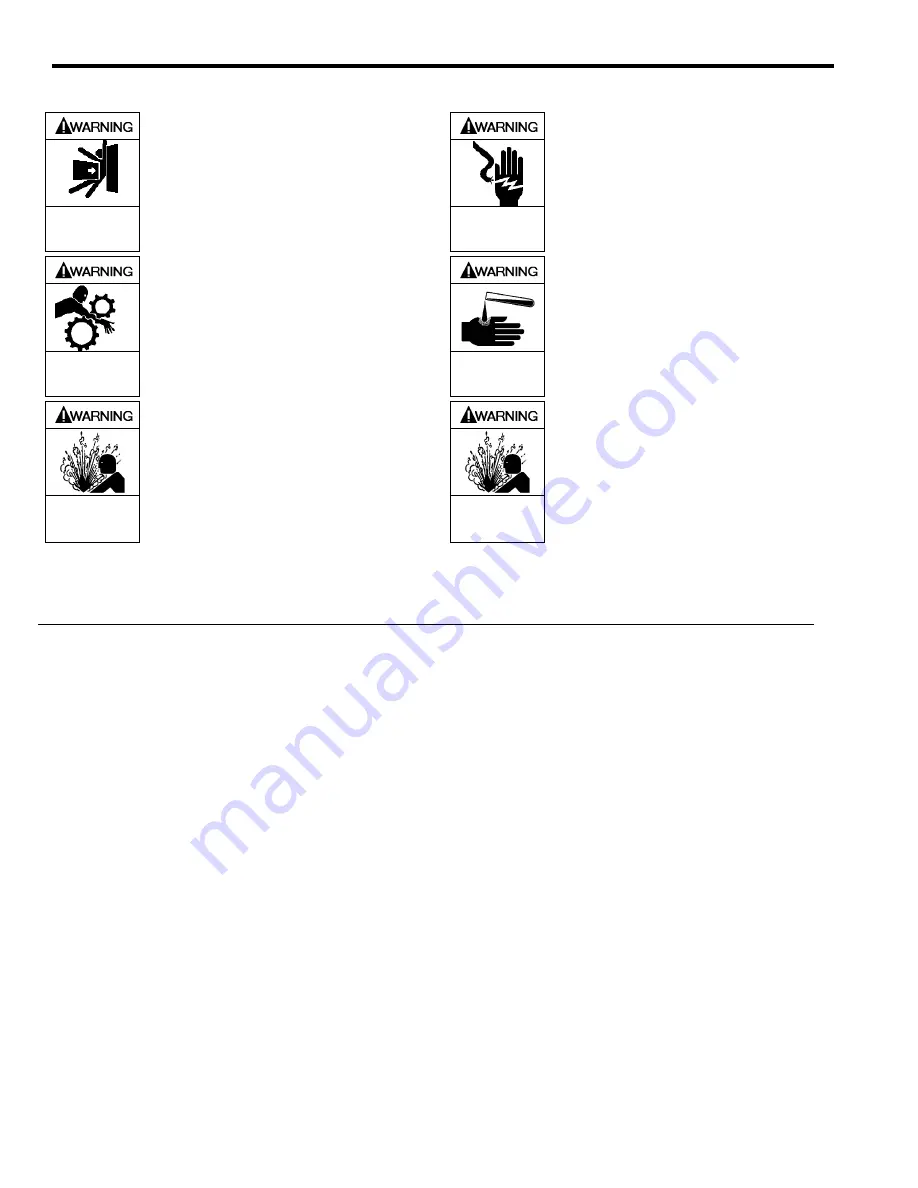
801-B00 Page 12/24
MAINTENANCE
Failure to set the vehicle emergency
brake and chock wheels before
performing service can cause severe
personal injury or property damage.
Failure to disconnect and lockout
electrical power before attempting
maintenance can cause shock, burns or
death.
Hazardous
machinery can
cause serious
personal injury.
Hazardous voltage.
Can shock, burn or
cause death.
Failure to disconnect and lockout
electrical power or engine drive before
attempting maintenance can cause
severe personal injury or death.
If pumping hazardous or toxic fluids,
system must be flushed and
decontaminated, inside and out, prior to
performing service or maintenance.
Hazardous
machinery can
cause serious
personal injury.
Hazardous or toxic
fluids can cause
serious injury.
Disconnecting fluid or pressure
containment components during pump
operation can cause serious personal
injury or property damage.
Failure to relieve system pressure prior
to performing pump service can cause
serious personal injury or property
damage.
Systems with meters will still
be pressurized even after the hose is
emptied.
Hazardous pressure
can cause personal
injury or property
damage
Hazardous pressure
can cause serious
personal injury or
property damage
Notice:
Maintenance shall be performed by qualified technicians only,
following the appropriate procedures and warnings as presented in this manual.
STRAINERS
Strainers must be cleaned regularly to avoid pump starvation.
Schedule will depend upon the application and conditions.
LUBRICATION
NOTICE:
To avoid possible entanglement in moving parts do not
lubricate pump bearings, hydraulic adapter coupling,
gear reducer or any other parts while pump is running.
NOTICE:
If pumps are repainted in the field, ensure that the grease
relief fittings (76A) are functioning properly after
painting. Do NOT paint them closed. Remove any
excess paint from the fittings.
Pump bearings and hydraulic motor couplings (if equipped)
must be lubricated every three months at a minimum. More
frequent lubrication may be required, depending on the
application and the operating conditions.
Pumps outfitted with dual seals should have their oil changed
after either 500 hours of operation or after any pressure event
that may have caused contamination. More frequent oil
changes may be required depending on application.
Recommended Grease:
Mobil® - Mobilgrease XHP222,
Exxon® - Ronnex MP Grease
or equivalent Lithium grease.
Recommended Barrier Oil
Conoco® Syncon Barrier Oil ISO grade 5
Greasing Procedure:
1. Remove the grease relief fittings (76A) from the bearing
covers (27) or hydraulic motor adapter (135).
2. SLOWLY apply grease with a hand gun until grease
begins to escape from the grease relief fitting port.
Discard excess grease in accordance with the proper
codes and regulations.
3. Replace the grease relief fittings (76A).
DO NOT over grease pump bearings. While it is normal for
some grease to escape from the grease tell-tale hole after
lubrication, excessive grease can cause mechanical seal
failure. The tell-tale hole is located in the head (20) between
the bearing (24) and the mechanical seal (153).
Barrier Oil Change Procedure
1. Evacuate pump of any fluid/vapor until a pressure of
0 psig is read in the pump.
2. Vent the barrier fluid tank until a pressure of 0 psig is
achieved.
Notice: A small amount of pumping fluid/gas
may have leaked into the barrier oil. Take the
proper precautions when venting.
3. Remove seal drain plugs from bottom of seal
cartridges (153)
4. Allow oil to drain from each seal and barrier pot.
5. Replace plugs and fill barrier pot, with new barrier
oil, to the seal pot manufacturer recommended
volume.