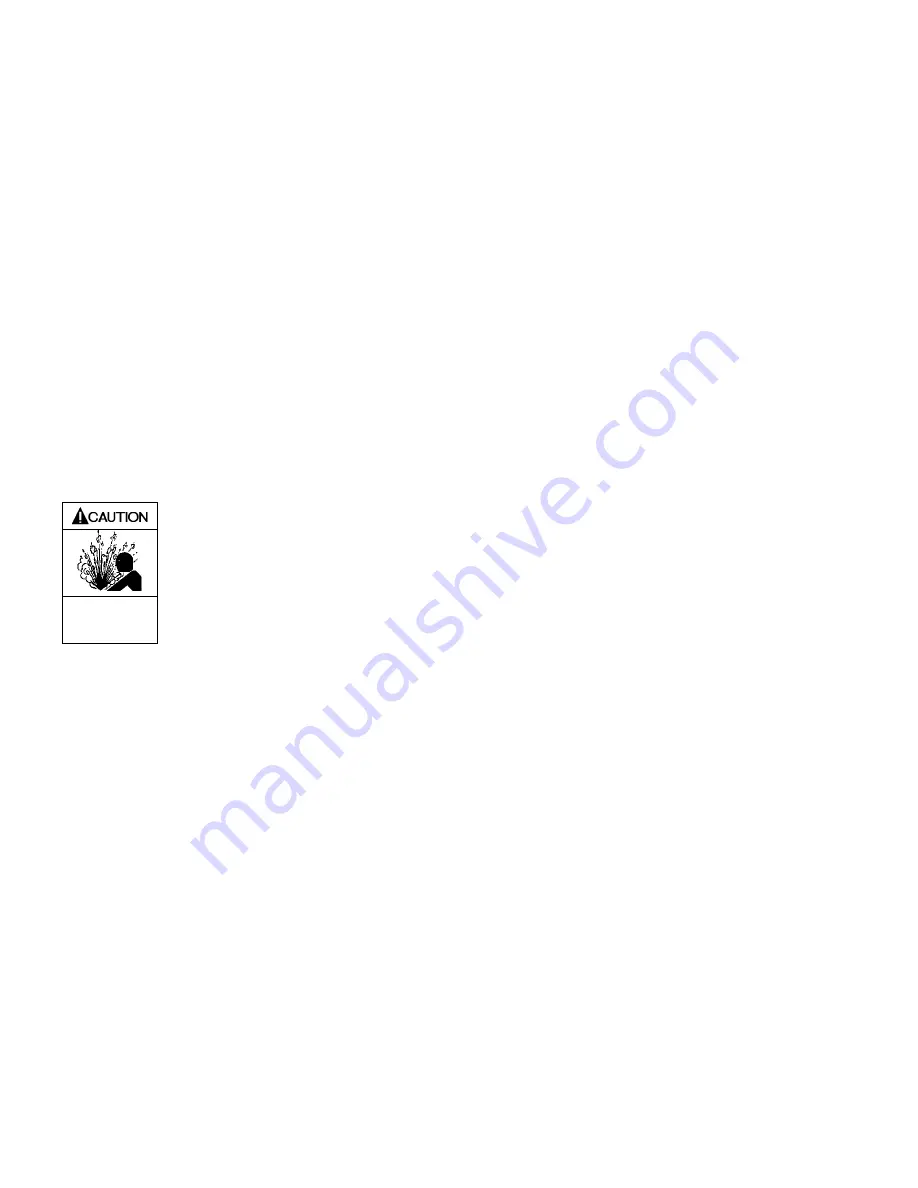
101-C00 Page 8/20
START UP PROCEDURES
NOTICE:
Consult the "General Pump Troubleshooting" section of
this manual if difficulties during start up are
experienced.
1. Start the motor. Priming should occur within one minute.
2. Check the suction and discharge pressure to see if the
pump is operating within the expected conditions.
Record pressures in the ‘Initial Start Up Information’
section.
3. Check for leakage from the piping and equipment.
4. Check for overheating, excessive noise or vibration of the
pump, reducer, and motor.
5. Check the flow rate to ensure the pump is operating
within the expected parameters. Record flow rate in the
‘Initial Start Up Information’ section.
6. Check the pressure setting of the relief valve by briefly
closing a valve in the discharge line and reading the
pressure gauge. This pressure should be 20 psi (1.4 bar)
higher than the maximum operating pressure.
Do not run the pump for more than 15 seconds with
the discharge valve completely closed.
If adjustments need to be made, refer to "Relief Valve
Setting & Adjustment."
Incorrect settings of the pressure relief
valve can cause pump component
failure, personal injury, and property
damage.
Hazardous pressure
can cause personal
injury or property
damage