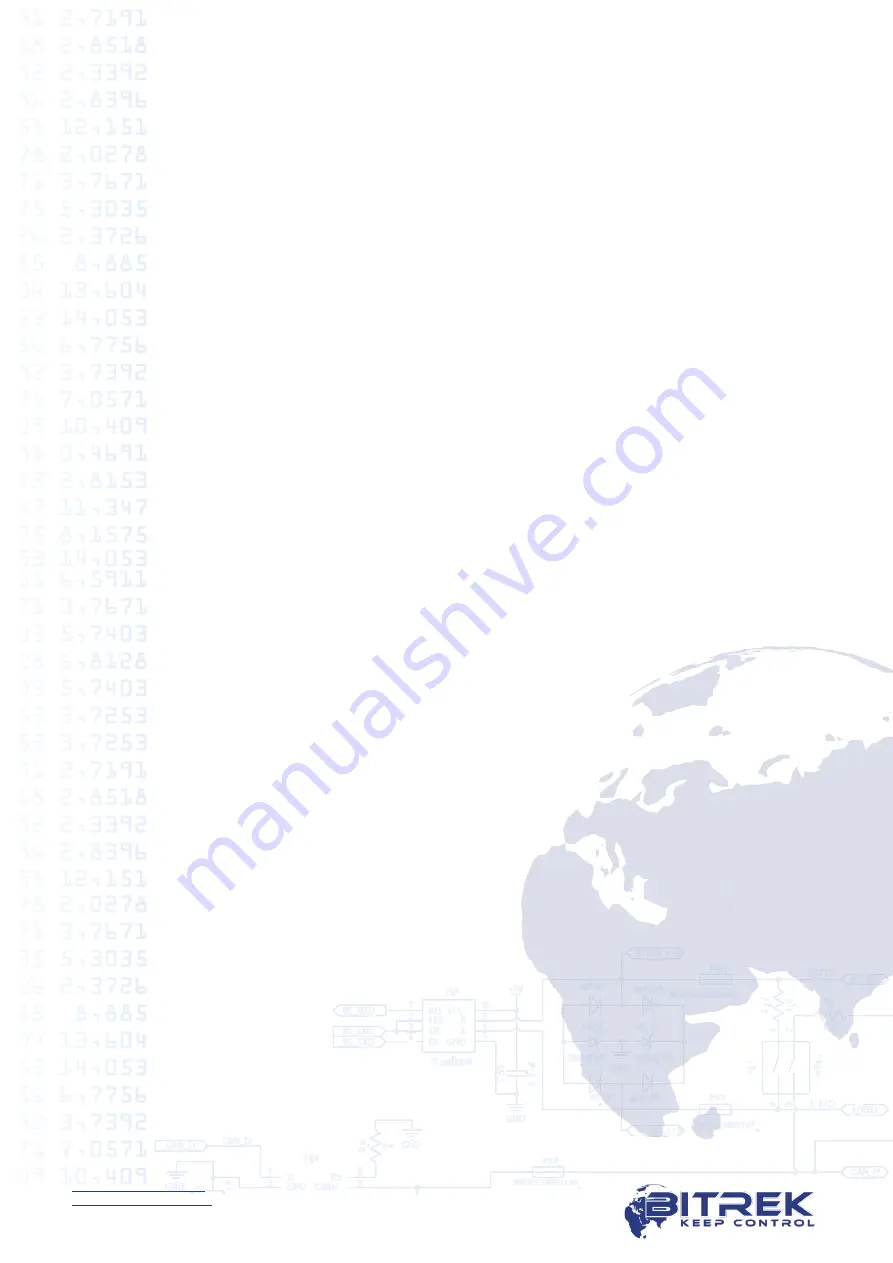
31
+380 44 507 02 07
setparam 0650 1; setparam 0651 0; setparam 0652 0; setparam 0653
0; setparam 0654 3; setparam 0655 10;
Readings from thermometer 3, when transmitted to server
ID 109
setparam 0660 1; setparam 0661 0; setparam 0662 0; setparam 0663
0; setparam 0664 3; setparam 0665 10;
Readings from thermometer 4, when transmitted to server
ID 110
setparam 0670 1; setparam 0671 0; setparam 0672 0; setparam 0673
0; setparam 0674 3; setparam 0675 10;
Configuring the Device for Operation with Fuel Meter
RS-485
The BI-910 TREK Tracking Device is compatible with fuel meter
supporting RS-485 bus. In total, up to four fuel meters can be connected.
Respective I/O component must be enabled in the configuration
settings of the device.
Besides, the fuel meters must be pre-configured with respective
network address. Network addresses 1, 2, 5, and 6 are reserved on the
BI-910 TREK Tracking Device for operation with fuel meters.
The tracking device has a feature of transmitting unprocessed
(raw) data from the level meters, as well as the data processed with
Kalman filter. Optimal filtration factors for Kalman filter are set by
default.
Filtered and non-filtered values are transmitted by different I/O
components.
Moreover, if the level meters are equipped with an in-built
temperature sensor, data from it can be retrieved and transmitted to a
server.
Also, when fuel level meters are used on special machinery with
GND conductor that can be switched off, a situation may occur when fuel
level readings are reset to zero if the chassis GND conductor is switched
off, which results in false fuel level drop being registered in the
monitoring software. In order to avoid this situation, the ID=0819
parameter must be enabled, which is disabled by default.
Enabling the use of values of the last valid fuel level:
setparam 0819 1;
If the cable length from the fuel meter to the tracker is over 12
meters, which, ultimately, results in failure to transmit the data from the
sensor, the device circuit board has switch No.1 (Figure 10) that is
intended for enabling pull-up resistor and 'А' & 'В' lines conditioning.
Switch No.2 is used for enabling the pull-up for CAN-bus.
Fig. 10. Line Conditioning Switch