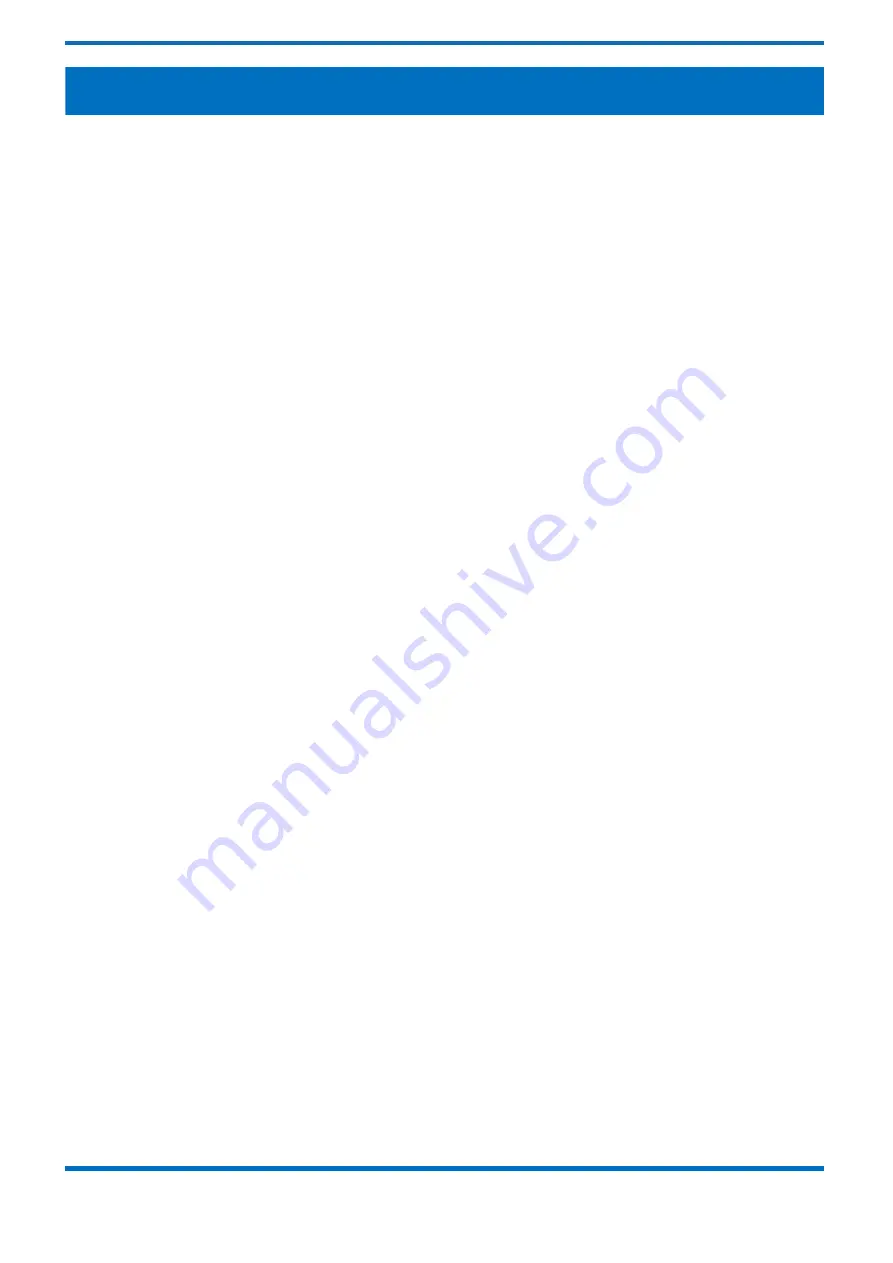
EN
• The outlet connection is not blocked or isolated by any valves.
• Suitable material for pumping is available at the suction hose.
• All required interlocks are tested and operational.
• Ensure all electrical and mechanical connections are correctly made.
• Check the gearbox oil level, please note the the gearbox is supplied with life lubricant and does not need any
maintenance.
Before starting:-
Set the pump speed to the minimum frequency 20 Hz and start the pump to remove any air from the circuit.
Inspect for any system leaks.
Set the pump cycle rate to achieve the required paint volume and then adjust the system back pressure
regulator to achieve the desired system fluid pressure.
Smart Mode:
The return line ‘back pressure’ regulator responds to the changes in system fluid flow demand, (due to variable
paint usage) by dynamically adjusting the paint flow rate returning to the system paint tank, thus maintaining
the set pressure.
SYSTEM OPERATION
77-3228 R3.3
9/36
www.carlisleft.com