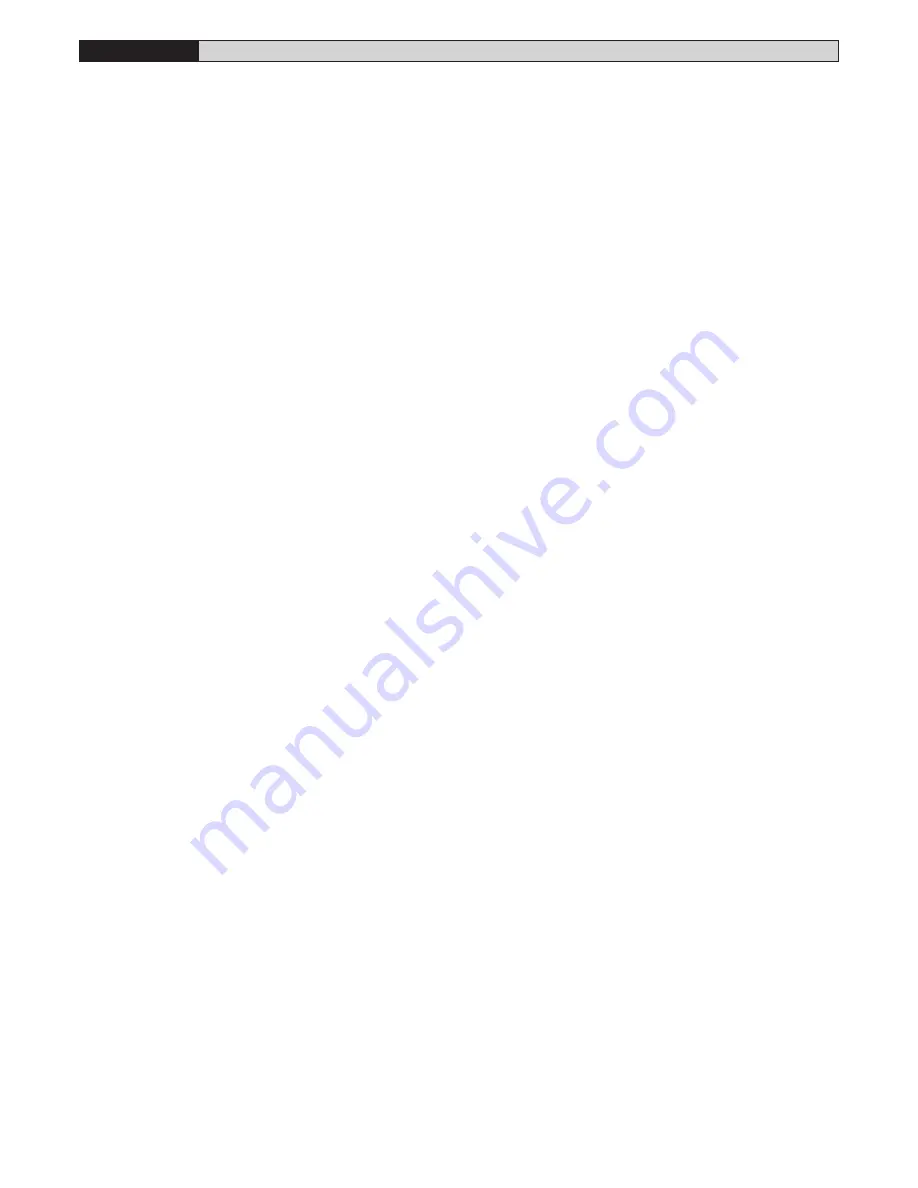
INSTALLATION MANUAL
ENGLISH
horizontal closed position on the “F” fork.
- If necessary, adjust the position of the “C” cams (fig.13) which control
the end-of-stroke devices.
16) EMERGENCY RELEASE (Fig.14)
The emergency release allows the bar to be manoeuvred manually. It is
activated from the outside of the box by inserting the personalised key
into the lock placed under the bar and rotating it anticlockwise by 180°.
WARNING! When an actuator without bar needs to be released, ensure
that the balancing spring is not compressed (bar in the opening position).
17) USE OF AUTOMATION
As automation can be remotely controlled and therefore not within sight, it
is essential to frequently check that all safety devices are perfectly efficient.
WARNING! In case of any malfunction in the safety devices, take imme-
diate action and require the assistance of a specialised technician.
It is recommended to keep children at a safe distance from the automa-
tion field of action.
18) CONTROL
The automation system is used to obtain motorised access control.
There are different types of control (manual, remote, magnetic badge,
mass detector etc.) depending on the installation requirements and
characteri-stics. For the various control systems, see the relevant
instructions.
19) MAINTENANCE
WARNING: before opening the door, make sure that the spring
has been unloaded (rod at 43°). WARNING: Before carrying out any
maintenance to the installation, disconnect the mains power supply. The
following points need checking and maintenance:
- Photocell optics. Clean occasionally.
- Electric edge. Carry out a periodical manual check to ensure that the
edge stops the bar in case of obstacles.
- Dismantle the gearmotor and replace the lubricating grease every two
years.
- When any operational malfunction is found, and not resolved, disconnect
the mains power supply and require the assistance of a specialised
tech-nician (installer). When automation is out of order, activate the
emergency release (see paragraph “11”) so as torelease the manual
bar opening and closing operations.
20) SCRAPPING
Materials must be disposed of in conformity with the current regulations.
In case of scrapping, the automation devices do not entail any particular
risks or danger. In case of recovered materials, these should be sorted
out by type (electrical components, copper, aluminium, plastic etc.).
21) DISMANTLING
WARNING: before opening the door, make sure that the spring has
been unloaded (rod at 43°). When the automation system is disassembled
to be reassembled on another site, proceed as follows:
- Disconnect the power supply and the entire electrical installation.
- Remove the actuator from its fixing base.
- Disassemble all the installation components.
- In the case where some of the components cannot be removed or are
damaged, they must be replaced.
22) MALFUNCTION: CAUSES and REMEDIES
22.1) The bar does not open. The motor does not turn.
WARNING: before opening the door, make sure that the spring has
been unloaded (rod at 43°).
1) Check that the photocells are not dirty, or engaged, or not aligned.
Proceed accordingly. Check the electric edge.
2) If the engine is overheated, the thermal protection might have been
acti-vated. Wait for it to be reset.
3) Check the correct connection of the drive motor and capacitor.
4) Check that the electronic appliance is correctly supplied. Check the
integrity of the fuses.
5) Use the control unit self-diagnosis (see par. 11.6), to check whether
the functions are correct. Identify any possible cause for the fault. If
self-diagnosis indicates that a start command persists, check that
there are no radio transmitters, start buttons or other control devices
keeping the start contact activated (closed).
6) If the control unit does not work, it must be replaced.
7) Check the movement of the cam-holder bars (fig. 13), if it is not smooth,
the bars must be lubricated.
22.2) The bar does not open. The motor turns but there is no movement.
1) The manual release was left engaged. Reset the motorised operation.
2) If the release is in the motorised operation position, check the gearmo-
tor for integrity.
WARNINGS
Correct controller operation is only ensured when the data contained
in the present manual are observed. The company is not to be held
responsible for any damage resulting from failure to observe the
installation standards and the instructions contained in the pres-
ent manual.
The descriptions and illustrations contained in the present manual
are not binding. The Company reserves the right to make any al-
terations deemed appropriate for the technical, manufacturing and
commercial improvement of the product, while leaving the essential
product features unchanged, at any time and without undertaking
to update the present publication.
22
- MOOVI 30S-30RMM-50RMM Ver. 06
D81
1480_07
Содержание MOOVI 30S
Страница 2: ...2 MOOVI 30S 30RMM 50RMM Ver 06 D811480_07 ...
Страница 10: ...MOOVI 30S 30RMM 50RMM Ver 06 23 D811480_07 ...
Страница 11: ...24 MOOVI 30S 30RMM 50RMM Ver 06 D811480_07 ...
Страница 13: ...Fig 7 Fig 5 Fig 6 Fig 4 1 2 6 3 SX DX 80Nm 4 5 58 MOOVI 30S 30RMM 50RMM Ver 06 D811480_07 ...
Страница 14: ...MOOVI 30S 30RMM 50RMM Ver 06 59 D811480_07 ...
Страница 15: ...Fig 13 Fig 14 2 G C Fig 11 Fig 12 SWC SWO SWC SWO 60 MOOVI 30S 30RMM 50RMM Ver 06 D811480_07 ...
Страница 17: ...62 MOOVI 30S 30RMM 50RMM Ver 06 D811480_07 ...
Страница 18: ...MOOVI 30S 30RMM 50RMM Ver 06 63 D811480_07 ...
Страница 19: ...64 MOOVI 30S 30RMM 50RMM Ver 06 D811480_07 ...
Страница 22: ...MOOVI 30S 30RMM 50RMM Ver 06 67 D811480_07 ...
Страница 23: ......