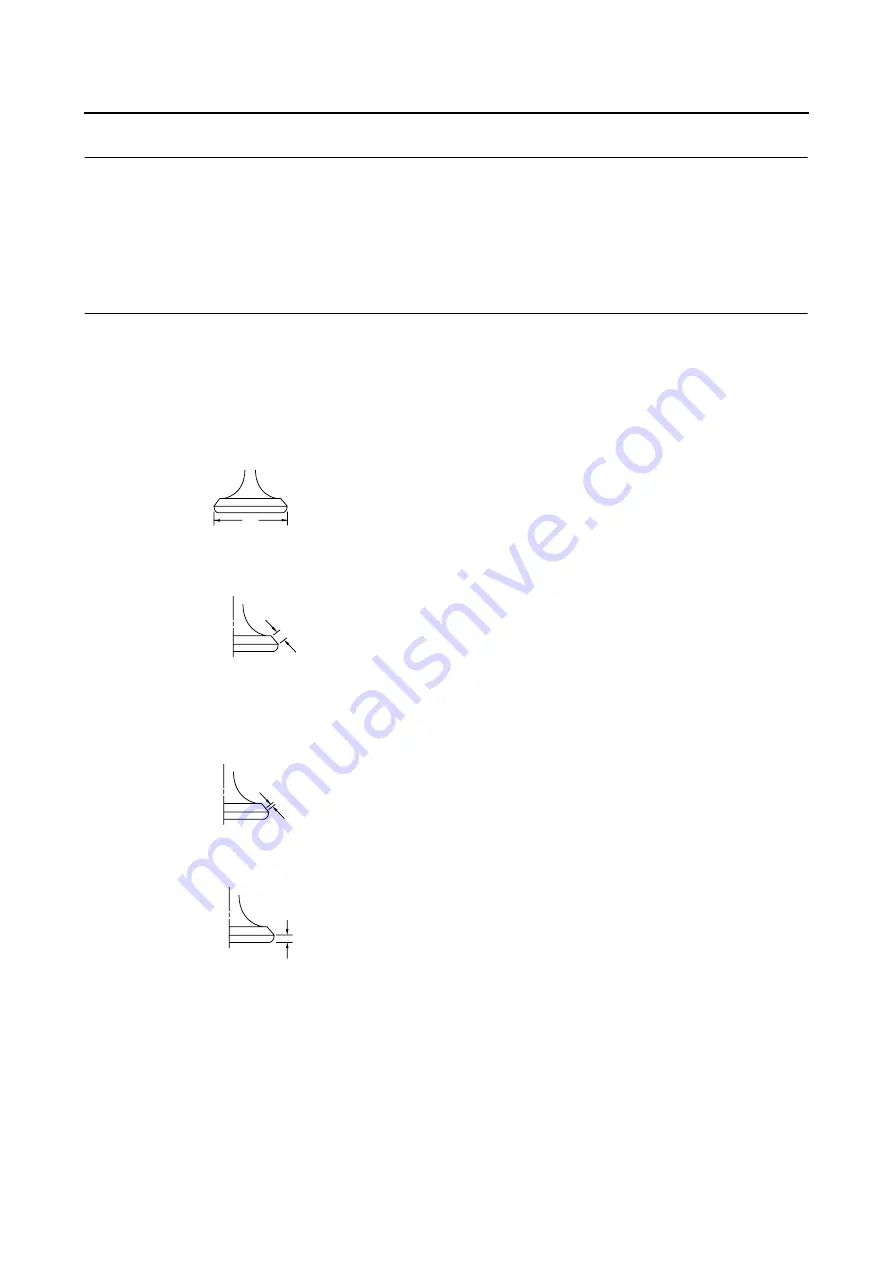
ENGINE SPECIFICATIONS
2-4
Tensioning system
Automatic
Rocker arm/rocker arm shaft
Rocker arm inside diameter
9.985
–
10.000 mm (0.3931
–
0.3937 in)
Limit
10.015 mm (0.3943 in)
Rocker arm shaft outside diameter
9.966
–
9.976 mm (0.3924
–
0.3928 in)
Limit
9.941 mm (0.3914 in)
Rocker-arm-to-rocker-arm-shaft clearance
0.009
–
0.034 mm (0.0004
–
0.0013 in)
Limit
0.074 mm (0.0029 in)
Valve, valve seat, valve guide
Valve clearance (cold)
Intake
0.10
–
0.14 mm (0.0039
–
0.0055 in)
Exhaust
0.20
–
0.24 mm (0.0079
–
0.0094 in)
Valve dimensions
Valve head diameter A (intake)
19.40
–
19.60 mm (0.7638
–
0.7717 in)
Valve head diameter A (exhaust)
16.90
–
17.10 mm (0.6654
–
0.6732 in)
Valve face width B (intake)
1.538
–
2.138 mm (0.0606
–
0.0842 in)
Valve face width B (exhaust)
1.538
–
2.138 mm (0.0606
–
0.0842 in)
Valve seat width C (intake)
0.90
–
1.10 mm (0.0354
–
0.0433 in)
Limit
1.6 mm (0.06 in)
Valve seat width C (exhaust)
0.90
–
1.10 mm (0.0354
–
0.0433 in)
Limit
1.6 mm (0.06 in)
Valve margin thickness D (intake)
0.50
–
0.90 mm (0.0197
–
0.0354 in)
Valve margin thickness D (exhaust)
0.50
–
0.90 mm (0.0197
–
0.0354 in)
Valve stem diameter (intake)
4.475
–
4.490 mm (0.1762
–
0.1768 in)
Limit
4.445 mm (0.1750 in)
Valve stem diameter (exhaust)
4.460
–
4.475 mm (0.1756
–
0.1762 in)
Limit
4.430 mm (0.1744 in)
Valve guide inside diameter (intake)
4.500
–
4.512 mm (0.1772
–
0.1776 in)
Limit
4.550 mm (0.1791 in)
Valve guide inside diameter (exhaust)
4.500
–
4.512 mm (0.1772
–
0.1776 in)
Limit
4.550 mm (0.1791 in)
Valve-stem-to-valve-guide clearance (intake)
0.010
–
0.037 mm (0.0004
–
0.0015 in)
Limit
0.080 mm (0.0032 in)
A
B
C
D