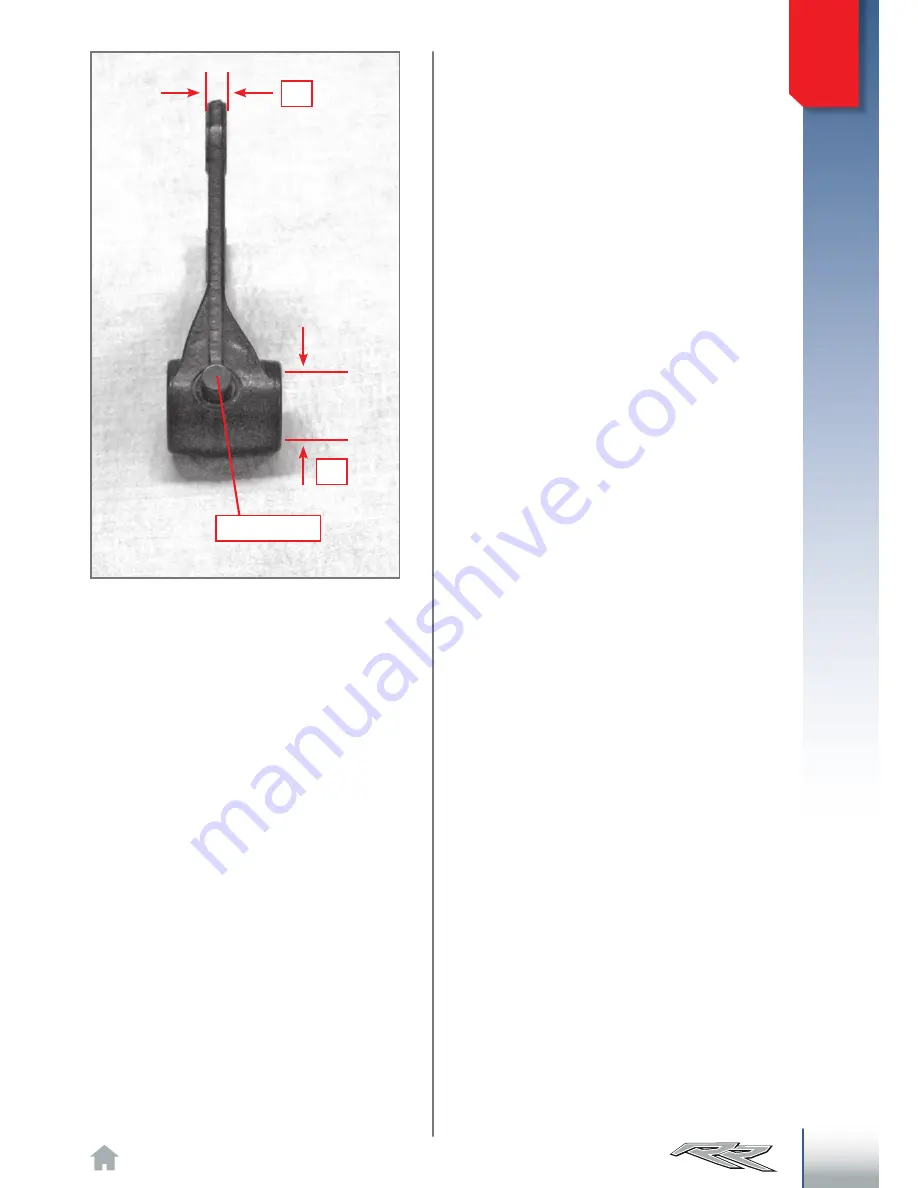
3
51
M
O
TO
R C
H
EC
K
S AN
D ASS
E
M
B
LY
A
Di
Drive pin
Make sure the distance
A
between the outer faces
of the fork is not less than that indicated below:
Minimum acceptable distance: 4,25mm
Check to make sure that the inside diameter D of
the fork pin seats is below the limit:
Fork inside diameter limit: 13,83mm
Make sure that the fork pins upon which they
slide have an outside diameter above the limit
(to be measured in the sliding areas of the forks
and in the housing areas of the crankcases):
Fork pin outside diameter limit: 13,75mm
Make sure that the desmodromic control device
has no corroded or worn areas especially in the
grooves in which the drive pins of the forks are
engaged.
Check the bearing on the desmodromic. Replace
it in the event of signs of meshing or jams during
motion.
Содержание Enduro RR 250 2016
Страница 1: ...COD 026 44 018 00 00 ...
Страница 110: ......