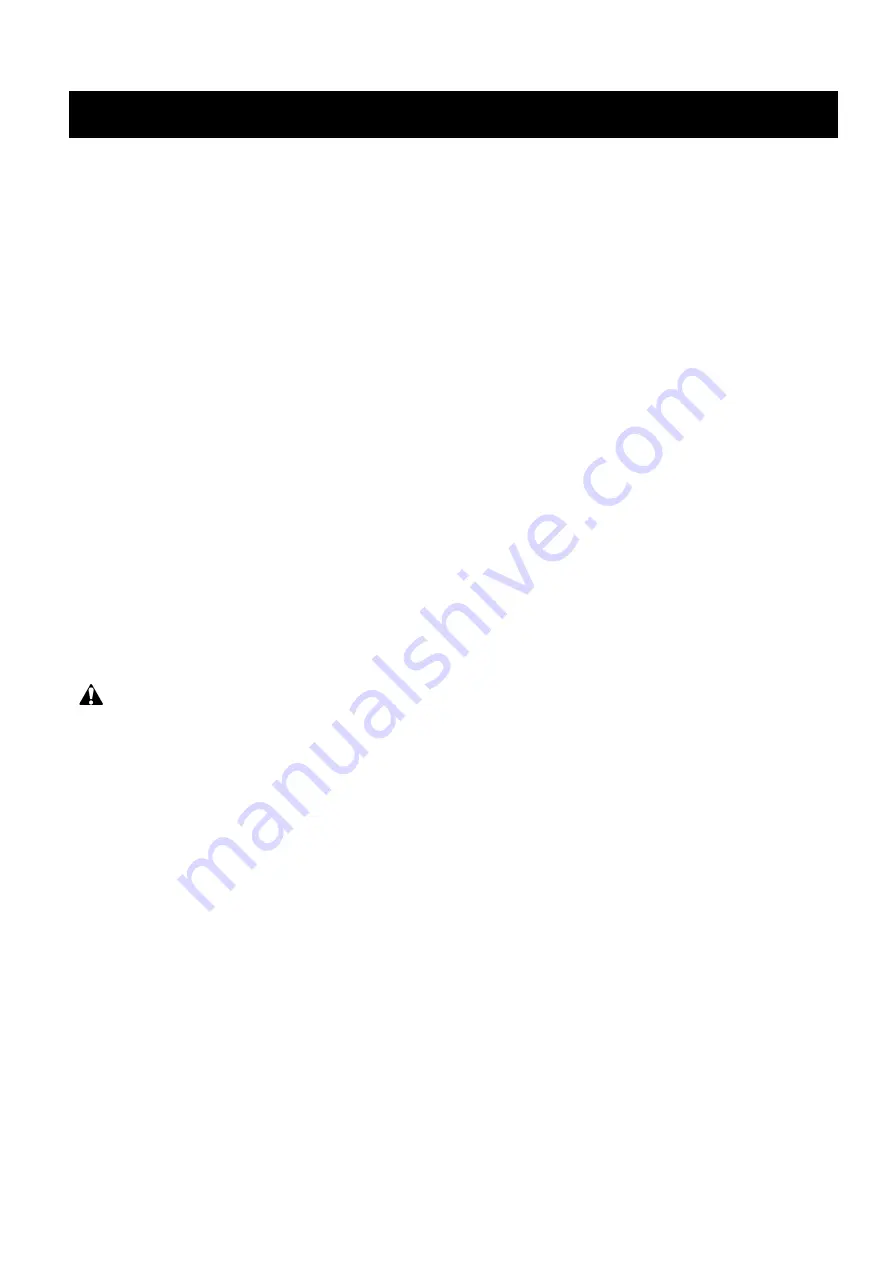
22
Preliminary inspections
•
Make sure that the feeding line is connected and hermetically sealed.
•
Make sure that the filter is clean.
•
Check that all the on-off valves (if any) along the feeding line are open and that water
flows freely to the pump.
The pump must never run dry.
•
Check that all the delivery pipes are connected to a user.
•
The coupling tolerances between pump shaft and transmission (misalignment of half-
couplings, cardan shaft angle, shaft-pulley play, belt tensioning, etc.) must be within the
limits established by the transmission manufacturer.
•
Install the oil plug with dipsticks in place of the non-vented oil plug (red). This operation
may have already been performed by the manufacturer of the machine in which the
pump is installed.
•
Check that when the pump is at a standstill, the oil level reaches the center-line of the oil
telltale. The oil level can also be checked by unscrewing the vented plug: the correct
level is between the two notches on the dipstick. Remember that the oil level must
always be checked when the pump is at a standstill and completely cooled.
•
Before starting the pump, carefully read the instructions in this manual and in the manual
of the machine in which the pump is installed.
•
Make sure that the moving parts of the pump are adequately protected and that they
cannot be accessed by unauthorized persons.
•
Make sure that ice does not form inside the pump if it is used at very low temperatures.
•
Perform the preliminary operations required by the manufacturer of the machine in which
the pump is installed.
WARNING
•
The pump cannot be put into service unless the machine in which it is installed
conforms to the safety requirements established by the European Directives.
This fact is guaranteed by the CE marking applied and by the Declaration of
Conformity of the manufacturer of the machine in which the pump is installed.
•
Do not use the pump if:
- it has been subjected to shocks and impact;
- there are evident oil leaks;
- there are evident water leaks;
In these cases, have the pump checked by a
Specialized Technician.
•
Supplementary maintenance inspections have to be performed by a
Specialized
Technician
.
7- PUTTING INTO SERVICE
Содержание 74.1030.97.3
Страница 39: ...39...
Страница 40: ...40 PART No 74 0066 99 2 REV 00...