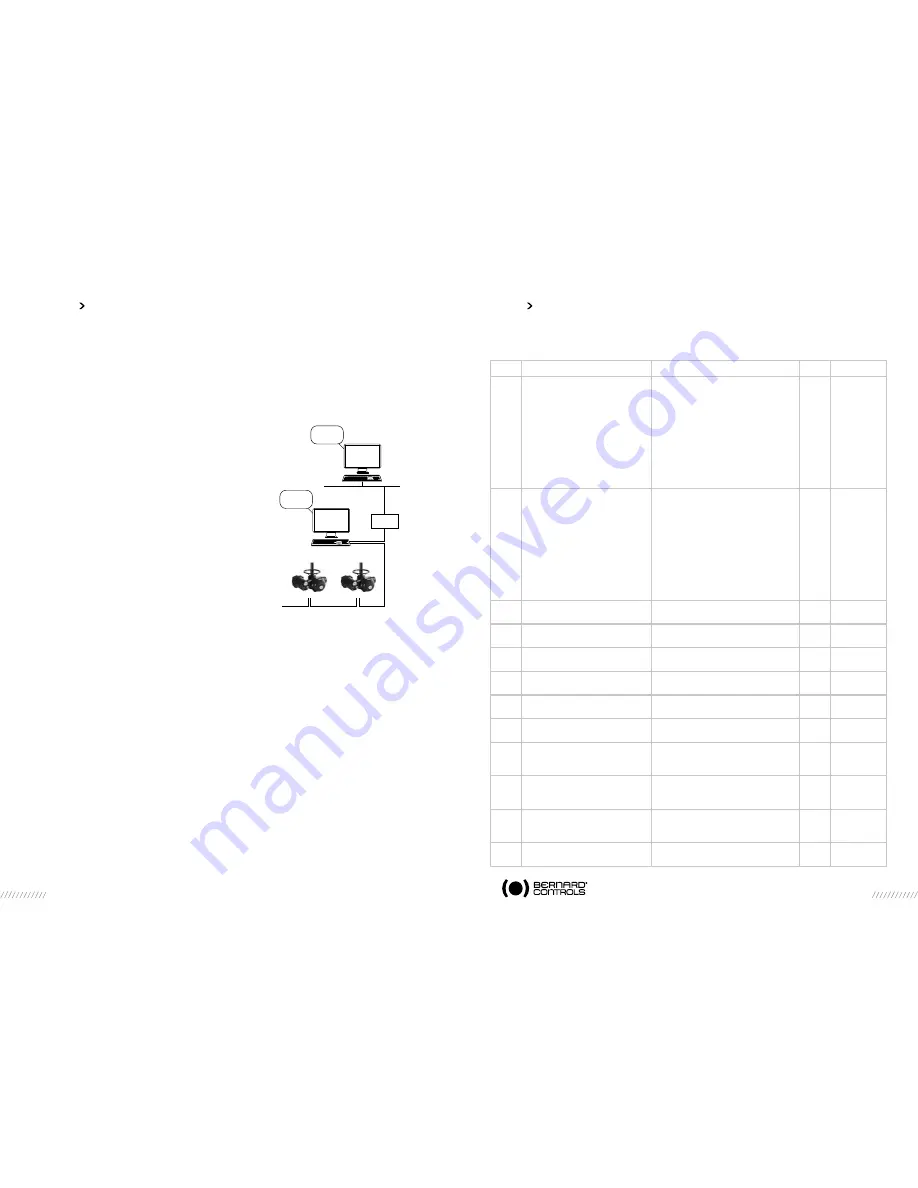
18
19
5
ACyCLIC COmmUNICATION
The INTELLIBUS supports acyclic communication (extension V1 of the Profibus protocol) which
allows to read the actuator’s state, to read all its configuration. It can be also reconfigured through
the V1 extension.
There is two type of master in the acyclic communication:
- The master class1 which supports cyclic communication. It is normally the same PLC which
manages the actuators.
- The master class2 supports all the acyclic communication. It can be included to Profibus
without interference. A laptop equipped with a Profibus module and PDM software may be used
as a master class2 anywhere on the line.
The INTELLIBUS supports the Read and Write messages
of the master class1 (MSAC1_Read, MSAC1_Write).
For master class 2, this interface supports Initiate,
Abort, Read and Write services. Interface board supports
a maximum of 2 simultaneous class2 master connections.
We advise to use PDM Siemens software to read and
configurate the actuators with a master class2. We can
give you an Electronic Device Description (EDD) which
allows you to manage our actuators with PDM.
With PDM and this EDD you can configure and parameterise
the actuators and also recover information for diagnostics
and maintenance.
For example, alarms, activity, torque curves…
To use PDM, not straight to the fieldbus but above
the PLC then the PLC must be Siemens S7 400 series.
In case of a redundant system, the connection of PDM
to one fieldbus line, will collect all data including those
communicating on the other line.
AvAILABLE DATA THROUgH PROFIBUS ACyCLIC COmmUNICATION
Data is organised in slot and index:
Slot = 0
Indexes (0 to 61)are listed below.
Index
Data
Description
Byte
Read/write
0
Set-up for auxiliary
command 1
0: not used
1:local(0) / remote(1)
2:local+remote(0) / remote(1)
3:local command inhibit(1)
4:open inhibit(1)
5:close inhibit(1)
6:ON-OFF(0) / AUTO(1)
7:fieldbus emergency closing (1)
8: fieldbus emergency opening (1)
9: fieldbus emergency stop (1)
10: partial stroke (1)
1
read / write
1
Set-up for auxiliary
command 2 coming
through the fieldbus
but for emergency commands
wired separately from
the fieldbus.
0: not used
1:local(0) / remote(1)
2:local+remote(0) / remote(1)
3:local command inhibit(1)
4:open inhibit(1)
5:close inhibit(1)
6:ON-OFF(0) / AUTO(1)
7: wired emergency closing (1)
8: wired emergency opening (1)
9: wired emergency stop (1)
10: partial stroke (1)
1
read / write
2
Local stop also inhibited
with a local command inhibit
0: no, local stop is possible
1: yes, local stop and off inhibited
1
read / write
3
Timing control
0: no timing control
1: timing control
1
read / write
4
no local stop in remote mode
0= local stop possible
1= no local stop
1
read / write
5
open priority
0= no priority
1= open priority
1
read / write
6
close priority
0= no priority
1= close priority
1
read / write
7
In case of emergency
command, torque limit is 100% 0= no, 1= yes
1
read / write
8
In case of emergency
command, thermal overload
is by- passed
0= no, 1= yes
1
read / write
9
Fail safe position in case
of loss of communication
0= stayput
1= closing
2= opening
1
read / write
10
Dead band for positioner
function
Unit 0.1%
mini value: 2 (0.2%)
maxi value: 50 (5%)
1
read / write
11
Start of closing
temporised zone
0 to100 %
1
read / write
Profibus
DPV1
Ethernet
PLC
PDM
PDM