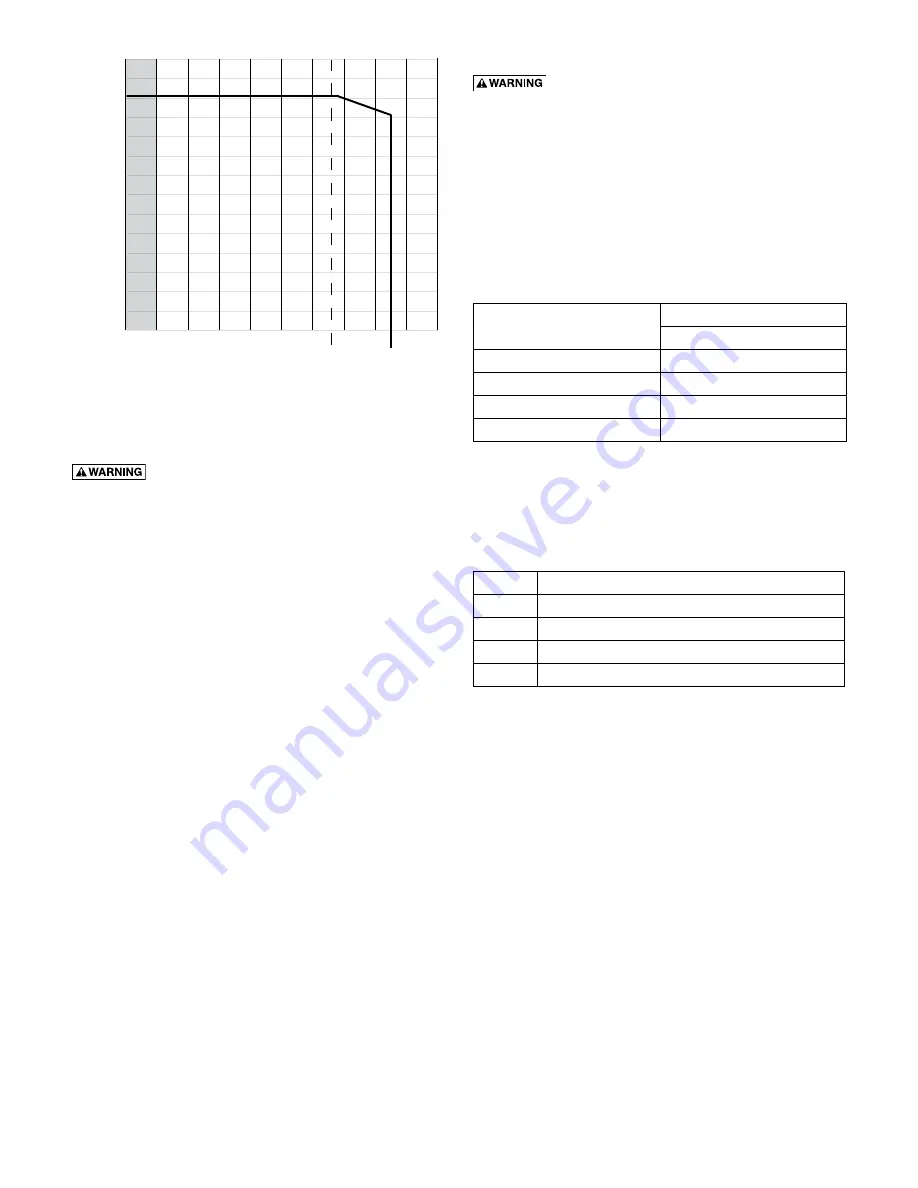
5
Installation
Risk of electric shock. Can shock, burn or
kill. Ground pump motor correctly before connecting
to power supply, per article 250-80 of the National
Electrical Code (NEC) in the U.S., or the Canadian
Electrical Code (CEC), as applicable.
Location
Locate pump in a dry, well ventilated area, not subject to
freezing or extreme variations in temperature.
Mount pump a minimum of 6” from any obstruction
or hot surface. Install the pump with the motor shaft
vertical. Make sure that an adequate supply of cool air
reaches the motor cooling fan. Maximum ambient air
temperature is 104° F (40° C).
For open systems requiring suction lift, locate the pump
as close to the water source as possible.
Foundation
Foundation should be concrete or a similarly rigid
foundation to provide a secure, stable mounting base for
the pump.
Secure pump to foundation using all bolt holes. Refer to
Figures 2 and 3 for bolt plate dimensions. Be sure that all
four pads on the base are properly supported.
Shim pump base to make sure that pump is level.
Piping
Risk of explosion and scalding. Do not run
pump with discharge valve closed; the water in the
pump may boil, with risk of explosion and steam burns
to anyone near.
If there is any danger of the pump running against a
closed discharge valve, install a pressure relief or by-pass
valve in the discharge pipe to allow for minimum liquid
flow through the pump. Minimum liquid flow through
the pump is needed for cooling and lubrication of the
pump (See Table IV). Run the bypass/relief valve and
discharge pipe to a floor drain or a tank for collection.
Suction pipe should be adequately sized (See Table V)
and run as straight and as short as possible to keep
friction losses to a minimum. Pipes, valves, and fittings
must have a pressure rating equal to or greater than the
maximum system pressure.
Pressure check the discharge piping as required by codes
or local regulations.
“Inlet” and “Outlet” are marked on the pump base to
show the direction of the liquid flow through the pump.
Install anti-vibration mountings on either side of the
pump if a minimum noise level is desired.
Install isolation valves in both inlet and outlet pipes near
the pump (see Figure 5). This allows for removal of pump
for service without draining the system and isolation of
the pump in case of a flooded suction condition.
TABLE IV – Minimum Pumping Rates
Type
Liquid Temperature
+5° F to +250° F
BVM2
1 GPM
BVM4
2 GPM
BVM8
4 GPM
BVM16
8 GPM
TABLE V – Minimum Suction Pipe Sizes
Type
Pipe Size
BVM2
1-1/4” Nominal Diameter, Schedule 40 Pipe
BVM4
1-1/4” Nominal Diameter, Schedule 40 Pipe
BVM8
2” Nominal Diameter, Schedule 40 Pipe
BVM16 2” Nominal Diameter, Schedule 40 Pipe
Figure 4 - Maximum Permissible Operating Pressure - all
BVM models
0
30
60
90
120
150
180
210
240
270
300
330
360
390
420
212
0 to100 120 140 160 180 200 220 240
250
260 280
Pressure in PSI
Temperature in Degrees F
3 98