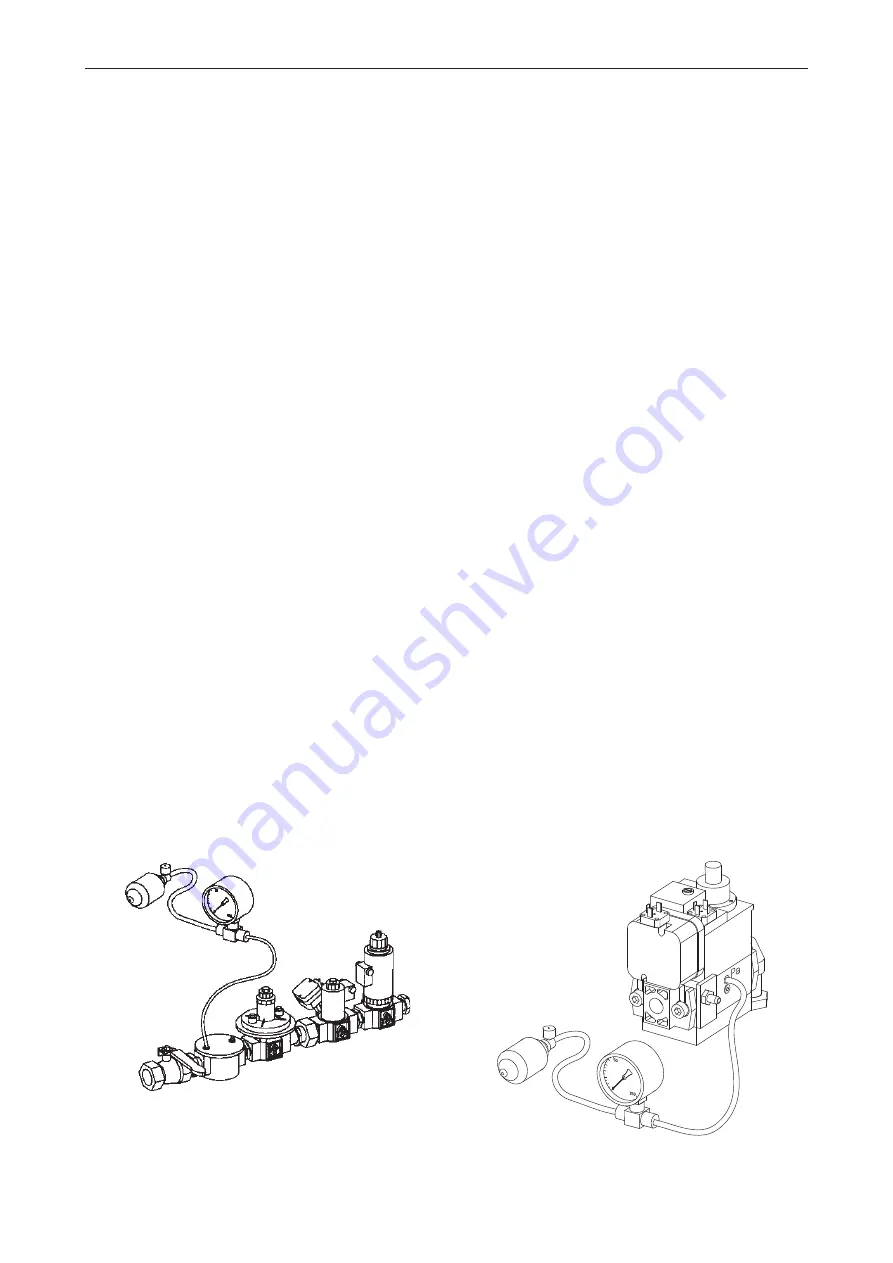
22
172 205 34 07-01
MEASURES AND CHECKS BEFORE START-UP
2-Stage or modulating burners
General rules
Care should be taken by the installer to ensure that no electrical cables or
fuel/gas pipes are trapped or damaged during installation or service/
maintenance.
Inner assembly
Ensure that the ignition and ionisation electrodes are correctly adjusted.
The sketch (see separate page) shows the correct measurements.
Gas quality
Ensure that the burner head is meant for the gas quality to be used
(see fig.).
Venting
The gas line is vented by loosening the screw on the test nipple for the inlet
pressure. Connect a plastic hose and conduct the gas into the open air.
After having vented the gas line tighten the screw again.
Electric function test:
Ensure that phase and neutral are not reversed. The gas shut-off cock
should be closed.To prevent the gas pressure switch from locking out,
it should be linked temporarily.
After the main switch has been switched on and the thermostats have
been adjusted, the pre-purging period begins (30-35sec.). At the end of
this period the pre-ignition period starts (0,5-2,5 sec. depending on the
design of the gas control). The gas valve is energized and opens and flame
is established. At the end of the safety time (2-3 sec.) the gas control
locks out. The solenoid valve and the motor will be "dead". Remove the link
from the gas pressure switch after the test is finished.
Note on 2-stage and modulating burners that during the pre-purging period
the damper opens to the set value for air on stage 2 and just before the end
of the pre-purging period it goes down to the air setting for stage 1. On
some burners under 350kW the pre-purging mainly takes place with the air
damper set for stage 1.
NOTE! Applies only to gas burner control LFL1.
When using LPG (Propane) the burner should be connected for post-purging.
Move the connection on terminal 6 to terminal 7 in the base of LFL1.
Leakage control
When making a leakage control of the gas supply system, the solenoid
valve should be closed. Connect a pressure gauge to the test nipple Pa,
see fig. The test pressure in the system should be 1,5x max. inlet pressure
or min. 150 mbar. If any leakage, locate the source by means of soapy
water or a leak location spray. After tightening repeat the test.
Gas train
Multibloc
Содержание BG 300LN
Страница 2: ......
Страница 13: ...14 172 155 05 01 01 EASURES AND CHECKS BEFORE START UP BG300 400LN Gas nozzle assembly Natural gas 4 5 12 14 2...
Страница 29: ......
Страница 32: ......
Страница 33: ......
Страница 34: ......
Страница 35: ......
Страница 36: ...Enertech AB P O Box 309 SE 341 26 Ljungby www bentone se www bentone com...