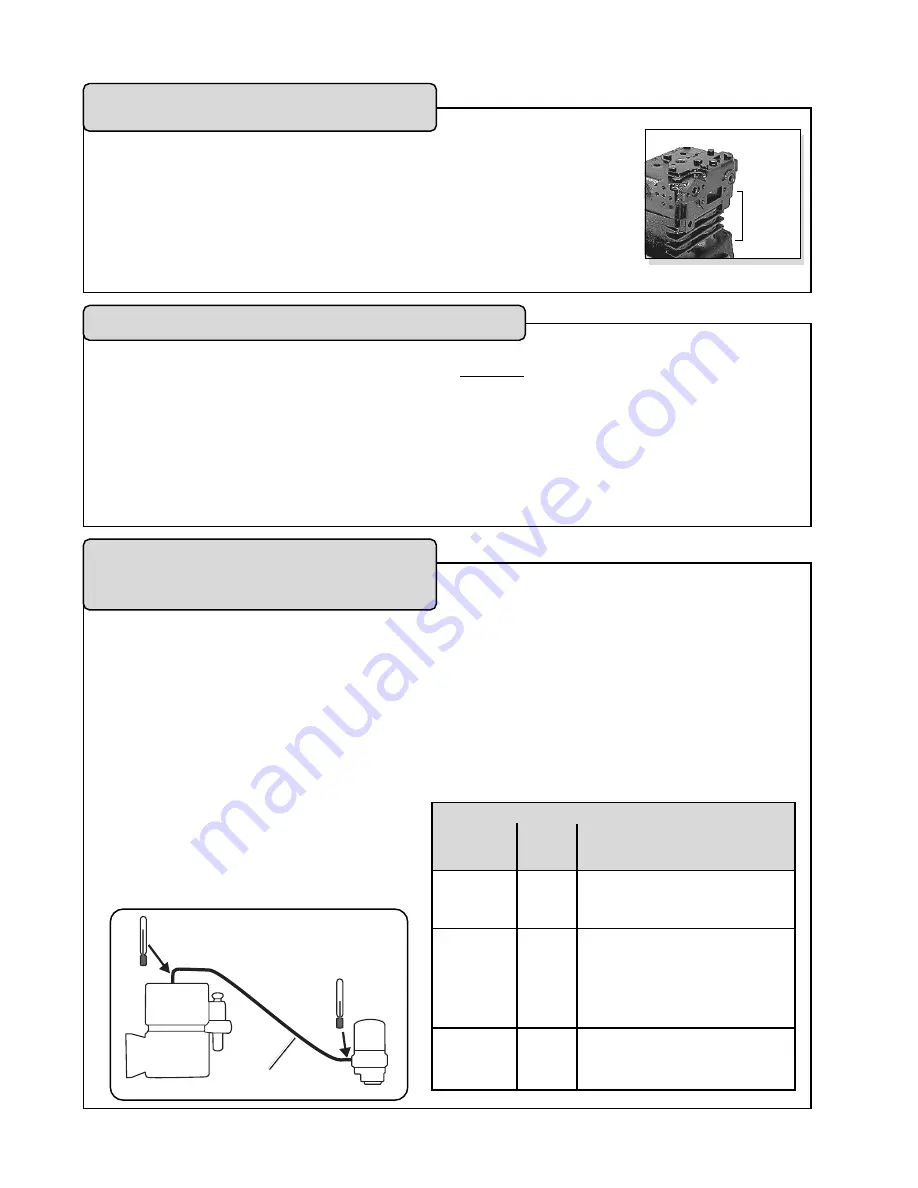
28
Tests
Exterior leaks at the head gasket are not a sign that oil is being passed
into the air charging system. Oil weepage at the head gasket does not
prevent the compressor from building air.
Observe the amount of weepage from the head gasket.
If the oil is only around the cylinder head area, it is acceptable (return the
vehicle to service), but, if the oil weepage extends down to the nameplate area
of the compressor, the gasket can be replaced.
Test 1: Excessive Oil Leakage at the
Head Gasket
Inspect for air leaks when working on a vehicle and
repair them promptly.
Park the vehicle on level ground and chock wheels.
Build system pressure to governor cut-out and allow
the pressure to stabilize for one minute.
Step 1: Observe the dash gauges for two additional
minutes without the service brakes applied.
Step 2: Apply the service brakes and allow the
pressure to stabilize. Continue holding for two
minutes (you may use a block of wood to hold the
pedal in position.) Observe the dash gauges.
If you see any noticeable decrease of the dash air
gauge readings (i.e. more than 4 psi, plus two psi
for each additional trailer) during either two minute
test, repair the leaks and repeat this test to confirm
that they have been repaired.
Air leaks can also be found in the charging system,
parking brakes, and/or other components - inspect
and repair as necessary.
Test 2: Air Brake System and Accessory Leakage
Caution: The temperatures used in this test
are not normal vehicle conditions.
Above normal temperatures can cause oil (as
vapor) to pass through the air dryer into the
air brake system.
This test is run with the engine at normal
operating temperature, with engine at max. rpm.
If available, a dyno may be used.
1.
Allow the compressor to build the air system
pressure to governor cut-in.
2.
Pump the brakes to bring the dash gauge
pressure to 90 psi.
3.
Allow the compressor to build pressure from
95 to 105 psi gauge pressure and maintain
this pressure range by cycling the brakes for
five (5) minutes.
4.
Then, while maintaining max rpm and
pressure range, measure and record the
surface temperature of the fittings:
ð
at the compressor discharge port. (T1).
ð
at the air dryer inlet fitting. (T2).
Use a touch probe thermocouple for
measuring the temperature.
5.
See table below.
6.
Retest before returning the vehicle to service.
Test 3: Air Compressor Discharge
Temperature and Air Dryer Inlet
Temperature*
Discharge Line
T1
T2
Compressor Air Dryer
Discharge
Inlet
Fitting
Fitting
Action
under
under
Temperatures are within
360°F
200°F
normal range for this test, check
other symptoms. Go to 4.0 (h).
under
over
This could indicate a discharge
360°F
200°F
line problem (e.g. restriction).
Call 1-800-AIR-BRAKE
(1-800-247-2725)
and speak with our Tech Team.
over
__
Compressor is running hot.
360°F
Check coolant 4(f) and/or
discharge line 4(g).
T1
T2
(* Note that only vehicles that have passed Test 2
would be candidates for this test.)
LOOK
FOR
WEEPAGE