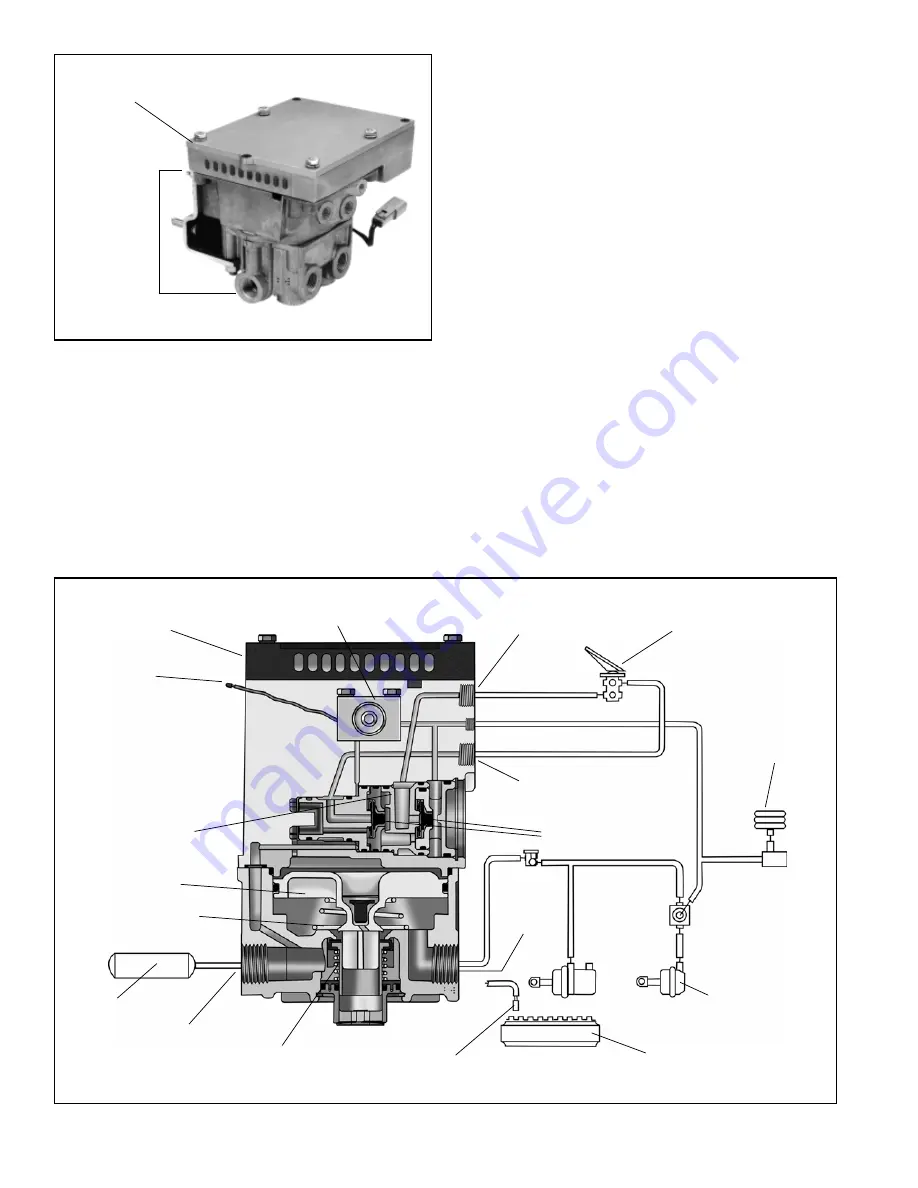
2
ATR-1DC
™
ANTILOCK
TRACTION
RELAY
VALVE
EC-16
™
CONTROLLER
FIGURE 2 - TYPICAL AT-1DC
™
ANTILOCK TRACTION ASSY.
FIGURE 3 - SECTIONAL AT-1DC
™
ANTILOCK TRACTION ASSEMBLY
The ATR-1DC
™
valve is part of the R-12
™
family of relay valves
which includes the R-12
™
, R-14
™
, BP-R1
™
, AR-1
™
& ATR-1
™
valves. The internal components of the relay portion of all of
these valves are similar and in many cases interchangeable
with the R-12
™
valve and therefore the same basic
components are used to service all of them. The ATR-1DC
™
valve is available with various crack pressures to
accommodate specific applications, however the standard
is 4 psi, achieved without any added spring.
OPERATION
GENERAL
While the ATR-1DC
™
valve is an antilock-traction relay valve
its true function is that of an air brake relay valve. Because
the ATR-1DC
™
is essentially a relay valve, with a traction
control function, the following description of operation
describes its operation as a relay valve and its function in
the traction control system. The full operation of the
antilock system and separate antilock components and their
operation is not addressed in this publication. For a
description of antilock operation, refer to the appropriate
Service Data Sheet covering the electronic controller used
with the ATR-1DC
™
valve (e.g. SD-13-4785 for the EC-16
™
electronic controller, or SD-13-4788 for the EC-17
™
electronic
controller). Other useful information on antilock system
components may be downloaded from www.bendix.com. For
example: SD-13-4793 (M-21
™
and M-22
™
antilock
modulators), SD-13-4870 (M-32
™
and M-32QR
™
antilock
modulators), SD-13-4754 (WS-20
™
wheel speed sensors),
and SD-13-4860 (WS-24
™
wheel speed sensors).
SERVICE BRAKES - APPLYING
Reservoir air pressure is present at the supply port (SUP)
and at the relay inlet and exhaust valve. Reservoir air
pressure also flows from the supply port through internal
TRACTION CONTROL SOLENOID
SUPPLY PORT
SECONDARY
SERVICE PORT
DOUBLE
CHECK VALVES
DELIVERY
PORT
EXHAUST PORT
RELAY PISTON
INLET-EXHAUST
VALVE
BLEND BACK
PISTON
SOLENOID
CONNECTOR
BRAKE VALVE
(SHOWING
DELIVERY AIR
LINES ONLY)
AIR BAG
BRAKE
CHAMBER
TONE RING
EC-16
™
OR EC-17
™
CONTROLLER
WHEEL SPEED
SENSOR
PRIMARY
SERVICE PORT
RELAY PISTON
SPRING
(IF USED)
RESERVOIR