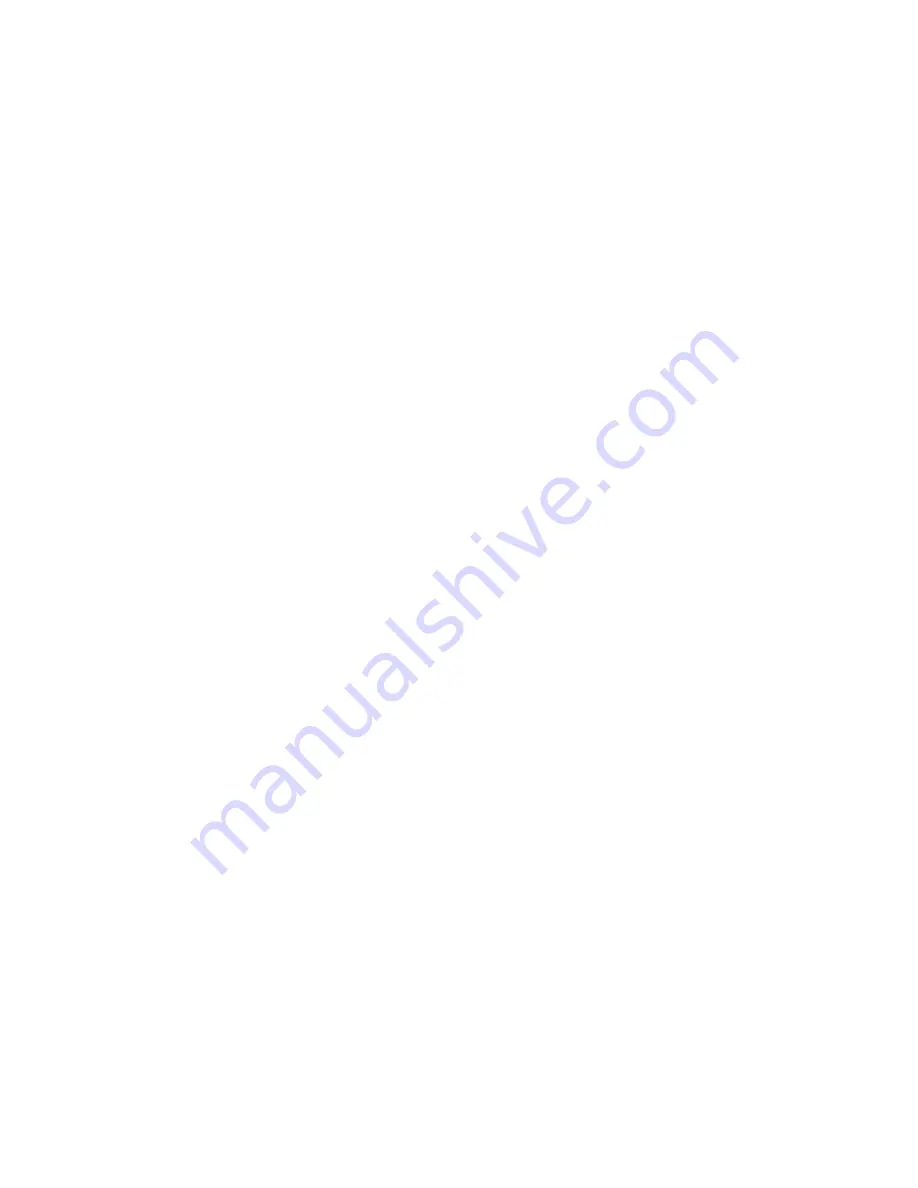
9
2. Install a gauge at the ATR-2
™
valve service port and at
one of the delivery ports, then install a gauge in each.
3. Connect the tractor service and emergency “glad hands”
(hose couplings) to hose couplings that have been
plugged, or alternatively, to a trailer. Build the tractor
system air pressure to governor cut-out and make 4 to 5
full brake applications. Check the air fittings at the
ATR-2
™
valve for leakage. Tighten as needed.
4. With the trailer supply valve (dash control w/red octagonal
button) and system park control (dash control w/yellow
diamond button) activated for tractor/trailer operation,
apply and release the brakes several times and check
for prompt application and release at each wheel. If
prompt reaction is noted at some, but not all wheels,
test the antilock modulator between the ATR-2
™
valve
and the brake chamber for proper operation. If a
“sluggish” response is noted at all wheels, inspect for a
kinked or obstructed air line leading to or from the
ATR-2
™
valve. If a complete release of the brakes is
noted at some, but not all wheels, test the antilock
modulator between the ATR-2
™
valve and the brake
chamber for proper operation. If an incomplete release
is noted at all wheels, inspect for a kinked or obstructed
air line leading to or from the ATR-2
™
valve.
5. Check the ATR-2
™
valve differential pressure by applying
10 psi to the service port and noting the pressure
registered at the delivery port. Subtract delivery port
pressure from the 10 psi service pressure to obtain the
differential. Compare the measured differential with the
pressure specified for the ATR-2
™
valve part number (see
the I.D. washer also for the differential). NOTE: For
ATR-2
™
valves not incorporating a relay piston return
spring(14) the measured differential should be
approximately 4 psi. When a spring is in use, the
differential will be higher.
6. Make and hold a full (100 psi or greater) brake application
and note that full pressure is delivered to the chambers.
7. Activate the dash mounted trailer supply valve for bobtail
tractor operation. Then make a slow brake application,
increasing the pressure at the ATR-2
™
valve’s service
port to 20 psi while watching the reaction at the delivery
port gauge. Note that delivery pressure rises to
approximately 5 to 10 psi and remains constant while
service pressure continues to rise to 20 psi. Release
the application.
8. Make another brake application and slowly increase the
pressure at the ATR-2
™
valve’s service port to between
60 and 70 psi while observing the gauge installed at the
delivery port. Note that when service port pressure rises
to between 20 and 30 psi, delivery pressure begins to
rise above the initial pressure noted in step 6. The rise
of delivery pressure should be at a proportioned rate of
approximately 3 to 1. At 70 psi service pressure, delivered
pressure should be 15 to 25 psi.
9. Make a full brake application and note that both test
gauges register the same pressure. IMPORTANT: If
during testing, the service port pressure is SLOWLY
increased from approximately 70 psi to a full (100 psi or
greater) brake application, the ATR-2
™
valve MAY begin
to cycle between an apply and exhaust mode. This
condition is normal while the ATR-2
™
valve is transitioning
from the proportioning mode to the full delivery mode
and will only occur if the service application is SLOWLY
increased as described. Cycling will not occur or can
be stopped by increasing or decreasing service port
pressure.
10. Disconnect the ATR-2
™
valve’s two pin solenoid connector
from the wire harness. Apply the probes of a volt-ohm
meter to the connector leading to the solenoid and note
the resistance of the solenoid is between 10 and 12
ohms.
11. Apply and remove vehicle power (12 vdc) to the two pin
connector half leading to the ATR-2
™
valve (solenoid)
while observing the brake chamber gauges. Note that a
full brake application is made and held while power is
applied to the ATR-2
™
valve’s solenoid and that it is
released when power is removed.
12. Remove the test gauges from the ATR-2
™
valve.
LEAKAGE TESTS
1. Build the air system pressure to governor cut-out. With
the dash mounted trailer supply valve activated for tractor/
trailer operation, apply a soap solution to all three exhaust
ports (two in cover and one in body). The leakage noted
should not exceed a 1” bubble in less than 3 seconds at
any exhaust port.
2. Make and hold a full brake application and apply a soap
solution to all three exhaust ports and around the cover
where it joins the body. The leakage noted should not
exceed a 1” bubble in less than 3 seconds at any exhaust
port.
If the ATR-2
™
valve fails to function as described, or leakage
is excessive, it should be replaced with a new or genuine
Bendix remanufactured unit or repair using maintenance
kit piece number 109359, available at any Bendix authorized
parts outlet.
VEHICLE PREPARATION
1. Park the vehicle on a level surface and block the wheels
and/or hold the vehicle by means other than the air
brakes.
2. Drain the air pressure from all vehicle reservoirs.
REMOVAL
1. Identify and mark or label all electrical wiring harnesses
and air lines and their respective connections on the
assembly to facilitate ease of installation.
2. Disconnect the air lines and wire harnesses.
3. Remove the controller and valve assembly (ATR-2
™
valve)
from the vehicle.
INSTALLATION
1. Install the assembled unit on the vehicle.
2. Reconnect all air lines and wire harnesses to the unit
using the identification made during REMOVAL step 1.