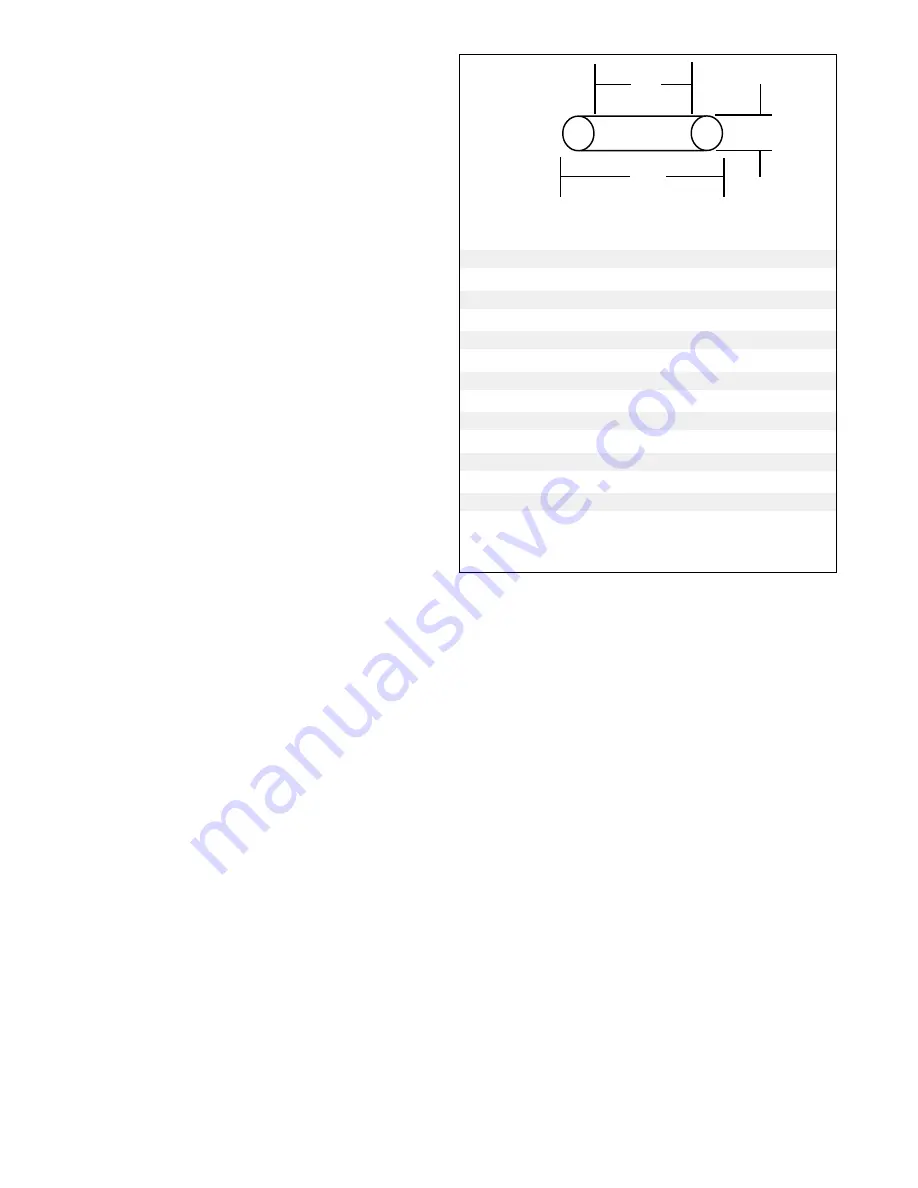
12
in place, install retaining ring(30) to secure it in the
piston(28). Make certain the retaining ring is fully seated
in its groove. Make sure the valve is straight, against
the exhaust seat and free to move.
6. Install both the large and small diameter o-rings(27 &
29) on the proportioning piston(28).
7. Install both the large and small diameter o-rings(25 &
26) on the blend back piston(24), then insert the small
diameter of the proportioning piston(28) into the small
diameter end of the blend back piston(24).
8. Carefully insert the assembled proportioning and blend
back pistons(24 & 28) into the bore in the cover(2). Do
not cut or pinch the o-rings.
9. With the bore of the cover facing up, install the spring
cage(23) in the blend back piston(24) so that its flat
side rests against the blend back piston. The concave
side of the spring cage should face toward the spring(22)
which is installed next.
10. Install the spring(22) in the cage(23) so that its coils are
within the I.D. of the cage.
11. Install the small and large diameter o-rings(44 & 37) on
the inlet seat(36) then insert the inlet seat into the bore
in the cover(2).
12. Install the small and large diameter o-rings(21 & 20) on
the check valve seat(16).
13. Install the spring(19) on the inlet seat(36) so that the
small diameter fits over and around the air passage
through the center of the inlet seat.
14. Install the check valve(17) and valve guide(18) in the
check valve seat(16). Note; The check valve must be
installed so that the “top hat” portion fits into the valve
seat(16). Install the valve guide(18) so that its flange
contains (surrounds) the coils of the large end of the
spring(19), when the valve seat(16) is installed in the
cover(2). Use a small amount grease to hold these parts
in the valve seat(16).
15. Install the assembled valve seat(16) with the check valve
and valve guide(17 & 18) into the cover(2) bore and while
holding it in place install the retaining ring(15). Make
certain the retaining ring is fully seated in its groove.
16. Install the valve retainer(8) on the inlet and exhaust
valve(9) so that the flange of the retainer(8) surrounds
the rubber portion of the valve. Install the inlet and exhaust
valve in the body(1).
17. Install the inlet and exhaust valve return spring(7) in the
body(1).
18. Install the large and small diameter o-rings(5 & 6) in the
exhaust cover(4), then install the exhaust cover in the
body(1) taking care not to damage the o-rings. Hold the
exhaust cover in place.
19. While depressing the exhaust cover(4), install the
retaining ring(3) in the body(1). Make certain the
retainer(3) is fully seated in its groove in the body.
20. If the valve was equipped with a relay piston return
spring(14), install the spring in the body, large diameter
first.
21. Using lubricant to hold them in place, install the large
and small sealing rings(11 & 35) on the cover(2).
22. Install the o-ring(13) on the relay piston(12), then install
the piston in the body(1).
23. Note the relationship marks made prior to disassembly,
then install the cover(2) on the body(1). Secure the
cover(2) on the body(1) using the two, short cap
screws(40). Again, noting the relationship marks, secure
the bracket(41) on the cover(2) and body(1) and using
the two long cap screws(10), washers(45 and 46) and
two nuts and washers(43). Torque the four cap screws
to 120 to 150 lb. in.
24. Install the two cap screws(42) that secure the bracket(41)
to the cover(2) and torque to 180 - 220 pound inches.
25. Noting the relationship marks made during disassembly,
secure the controller(39) to the cover(2) using the four
cap screws(38). Torque the four cap screws to 50-80
pound inches.
26. Install all air line fittings and plugs making certain thread
sealing material does not enter the valve.
27. Install the rebuilt valve on the vehicle and perform the
OPERATION AND LEAKAGE TESTS before placing the
vehicle in service.
O-Ring Identification
Key
Description
Qty.
I.D.
O.D.
W
5
O-Ring
1
0.862
1.068
0.103
6
O-Ring
1
1.424
1.63
0.103
11
O-Ring
1
3.487
3.693
0.103
13
O-Ring
1
3.234
3.512
0.139
20
O-Ring
1
1.362
1.568
0.103
21
O-Ring
1
1.114
1.254
0.07
25
O-Ring
1
1.112
1.318
0.103
26
O-Ring
1
0.737
0.943
0.103
27
O-Ring
1
0.412
0.552
0.07
29
O-Ring
1
0.739
0.879
0.07
31
O-Ring
1
0.489
0.629
0.07
37
O-Ring
1
1.356
1.496
0.07
44
O-Ring
1
1.176
1.316
0.07
SECTIONAL SIDE
VIEW OF HOW AN
O-RING IS
MEASURED.
1234
1234
1234
1234
1234
1234
12345
12345
12345
12345
12345
I.D.”
W
O.D.”
FIGURE 14 - O-RING IDENTIFICATION CHART
O-rings available in maintenance kit piece no. 109359.
BW1791 © 2004 Bendix Commercial Vehicle Systems LLC All rights reserved. 6/2004 Printed in U.S.A.