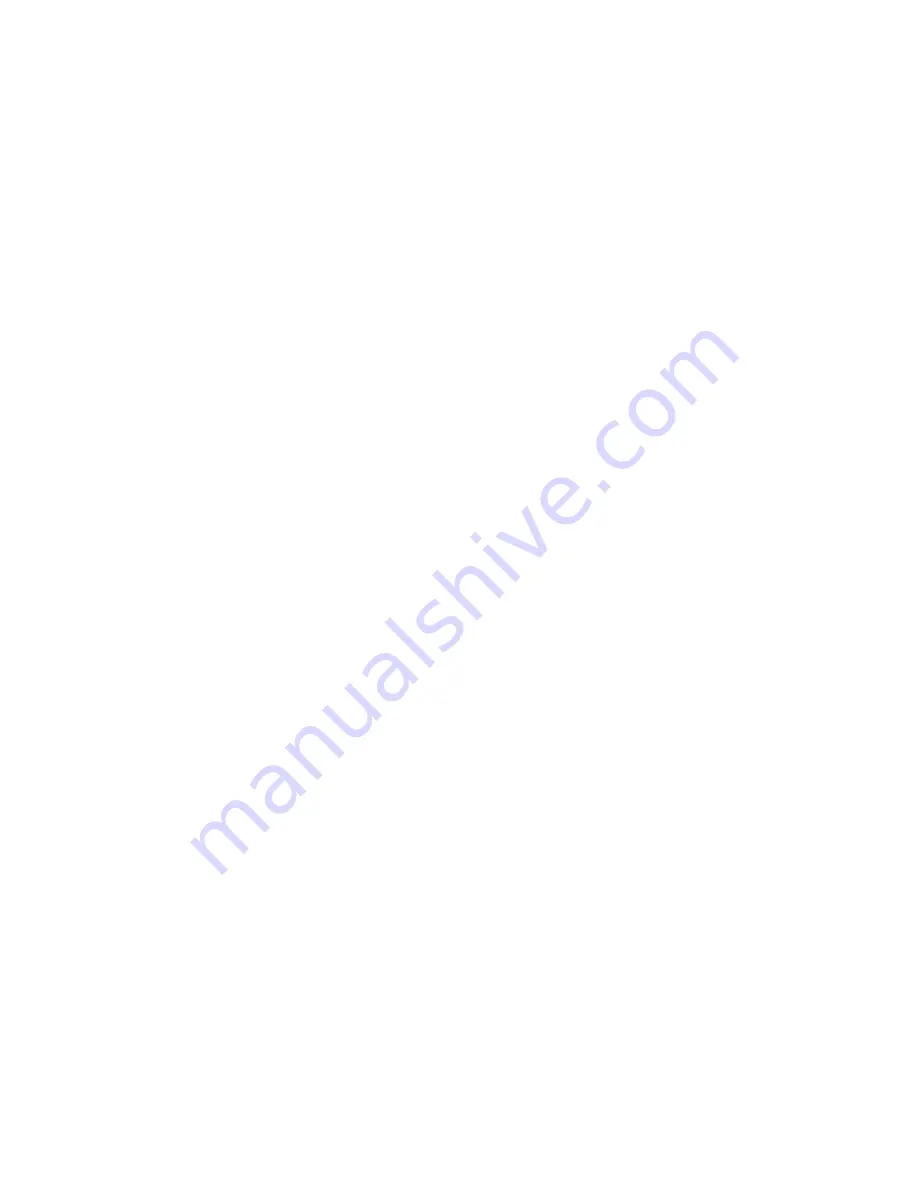
7
9. Components with stripped threads or damaged
parts should be replaced rather than repaired. Do
not attempt repairs requiring machining or welding
unless specifically stated and approved by the
vehicle and component manufacturer.
10. Prior to returning the vehicle to service, make
certain all components and systems are restored
to their proper operating condition.
11. For vehicles with Antilock Traction Control (ATC),
the ATC function must be disabled (ATC indicator
lamp should be ON) prior to performing any
vehicle maintenance where one or more wheels
on a drive axle are lifted off the ground and
moving.
OPERATION & LEAKAGE TESTS
GENERAL
A change in vehicle braking characteristics or a low pressure
warning may indicate a malfunction in one or the other brake
circuit, and although the vehicle air brake system may
continue to function, the vehicle should not be operated until
the necessary repairs have been made and both braking
circuits, including the pneumatic and mechanical devices
are operating normally. Always check the vehicle brake
system for proper operation after performing brake work and
before returning the vehicle to service.
OPERATION TEST
1. Apply and release the brakes several times and check
for prompt application and release at each wheel. If a
prompt reaction is noted at some, but not all wheels,
test the antilock modulator between the ATR-1
™
valve
and the brake chamber for proper operation. If a sluggish
response is noted at all wheels, inspect for a kinked or
obstructed air line leading to or from the ATR-1
™
valve. If
a complete release of the brakes is noted at some, but
not all wheels, test the antilock modulator between the
ATR-1
™
valve and the brake chamber for proper operation.
If an incomplete release is noted at all wheels, inspect
for a kinked or obstructed air line leading to or from the
ATR-1
™
valve.
Note: The ATR-1
™
valve’s differential pressure can be
checked by applying 10 psi to the service port and noting
the pressure registered at the delivery port. Subtract
delivery port pressure from the 10 psi service pressure
to obtain the differential. Compare the measured
differential with the pressure specified for the ATR-1
™
valve’s part number (see the l.D. washer also for the
differential). NOTE: For ATR-1
™
valves not incorporating
a relay piston return spring(14) the measured differential
should be approximately 4 psi. When a spring is in use,
the differential will be higher.
2. Disconnect the ATR-1
™
valve’s two pin solenoid connector
from the controller wire harness. Apply the probes of a
volt-ohm meter to the connector leading to the solenoid
and note the resistance of the solenoid is between 10
and 12 ohms. If resistance other than this is noted,
replace the ATR-1
™
valve.
3. Apply and remove vehicle power (12 vdc) to the two pin
connector half leading to the ATR-1
™
valve’s (solenoid)
while observing the brake chambers. Note that a brake
application is made and held while power is applied to
the ATR-1
™
valve’s solenoid and that it is released when
power is removed.
LEAKAGE TESTS
1. Build the air system pressure to governor cutout. Apply
a soap solution to the exhaust port. The leakage noted
should not exceed a 1” bubble in less than 3 seconds.
2. Make and hold a full brake application and apply a soap
solution to the exhaust port and around the cover where
it joins the body. The leakage noted should not exceed
a 1” bubble in less than 3 seconds at the exhaust port.
If the ATR-1
™
valve fails to function as described, or
leakage is excessive, it should be replaced with a new
or genuine Bendix remanufactured unit or repaired using
a genuine Bendix maintenance kit piece number 109368,
available at any authorized parts outlet.
VEHICLE PREPARATION
1. Park the vehicle on a level surface and block the wheels
and/or hold the vehicle by means other than the air
brakes.
2. Drain the air pressure from all vehicle reservoirs.
REMOVAL
1. Identify and mark or label all electrical wiring harnesses
and air lines and their respective connections on the
assembly to facilitate ease of installation.
2. Disconnect the air lines and wire harnesses.
3. Remove the controller and valve assembly from the
vehicle.
INSTALLATION
1. Install the assembled unit on the vehicle.
2. Reconnect all air lines and wire harnesses to the unit
using the identification made during REMOVAL step 1.
3. After installing the unit, perform the OPERATION &
LEAKAGE TESTS for the air valve before placing the
vehicle in service.