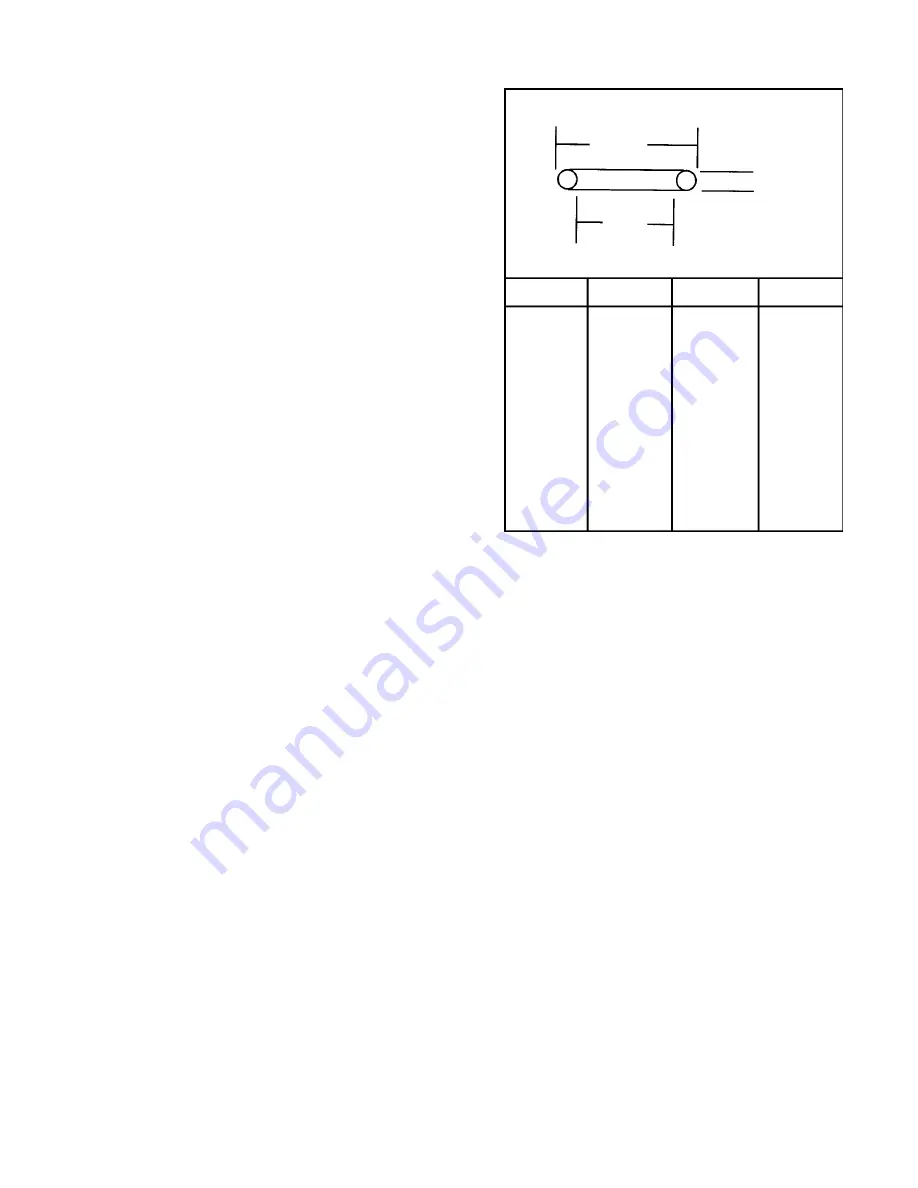
11
5. Carefully insert the assembled valve (33) and seat (34)
into the proportioning piston (30), making certain that
the coils of the valve spring (32) rest on the four tabs of
the valve (33). While holding the seat (34) in place, install
the retaining ring (36) to secure it in the piston (30).
Make certain the retaining ring is fully seated in its
groove.
6. Install both the large and small diameter o-rings (31 &
29) on the proportioning piston (30).
7. Install both the large and small diameter o-rings (27 &
28) on the blend back piston (26), then insert the small
diameter of the proportioning piston (30) into the small
diameter end of the blend back piston (26).
8. Carefully insert the assembled proportioning and blend
back pistons (30 & 26) into the cover (4).
9. Install the spring cage (25) in the blend back piston (26)
so that it’s flat side rests against the blend back piston.
10. Install the spring (24) in the cage (25) so that its coils
are within the I.D. of the cage.
11. Insert the service piston (23) in the cover (4) so that the
coils of the spring (24) are contained within the piston
and the six protruding posts of the piston are visible
after the piston is in the cover.
12. Install the o-ring (22) on the exhaust piston (21) then
install the exhaust piston (21) in the cover (4). Refer to
the figure and make certain that the exhaust piston (21)
is installed with its concave surface away from the
service piston (23).
14. While holding the exhaust piston (21) in the cover (4),
install the retaining ring (20), making certain it is fully
seated in its groove.
15. Install the exhaust diaphragm (39) using its screw (37)
and washer (38) to retain it. Torque the screw to 8-15
pound inches.
16. Install the valve retainer (15) on the inlet and exhaust
valve (16) so that the flange of the retainer (15)
surrounds the rubber portion of the valve. Install the
inlet and exhaust valve in the body (9).
17. Install the inlet and exhaust valve return spring (14) in
the body (9).
18. Install the large and small diameter o-rings (13 & 12) in
the cover (11), then install the exhaust cover in the body
(9) taking care not to damage the o-rings. Hold the
exhaust cover in place.
19. While depressing the exhaust cover (11), install the
retaining ring (10) in the body (9). Make certain the
retainer (10) is fully seated in its groove in the body.
20. If the AR-2
™
valve was equipped with a relay piston return
spring, install the spring in the body, large diameter first.
21. Using lubricant to hold them in place, install the large
diameter sealing ring (19) on the cover (4) and the
small diameter sealing ring (40) on the body (9).
22. Install the o-ring (18) on the relay piston (17), then install
the piston in the body (9).
23. After noting the relationship marks made prior to
disassembly, install the cover (4) on the body (9). Secure
the cover to the body using the two shortest cap screws
and lock washers (7). Make certain the sealing rings
(19 & 40) remain in place. Torque the cap screws to
120-150 pound inches.
24. Secure the mounting bracket (6) to the cover (4) using
the cap screws and lock washers (5), and torque the
cap screws to 180-220 pound inches. Then secure the
mounting bracket (6) to the body (9) and cover (4) using
the two longest cap screws and lock washers (7) and
nuts (8) and torque the cap screws to 120-150 pound
inches.
25. Install all air line fittings and plugs making certain thread
sealing material does not enter the valve.
26. Install the AR-2
™
valve on the vehicle and perform the
Operation and Leakage Tests before returning the vehicle
to service.
O.D.
W
I.D.
KEY NO.
I.D.
O.D.
W
12
.862"
1.068"
.103"
13
1.424"
1.630"
.103"
19
3.487"
3.693"
.103"
18
3.234"
3.512"
.139"
22
1.356"
1.496"
.070"
27
1.112"
1.318"
.103"
28
.737"
.943"
.103"
29
.412"
.552"
.070"
31
.739"
.879"
.070"
35
.489"
.629"
.070"
O-RING IDENTIFICATION CHART