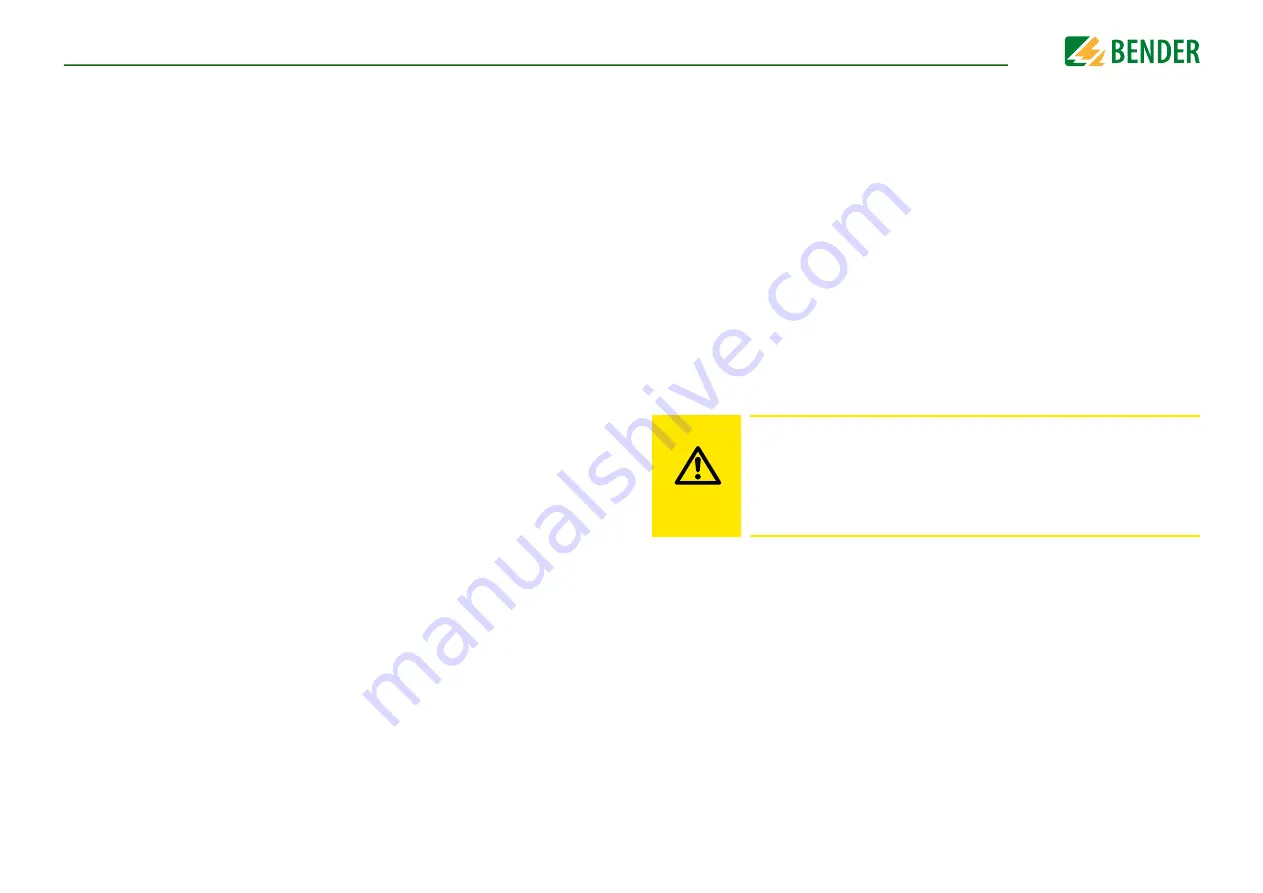
Function
Function
iso685-D-P_D00170_00_M_XXDE/06.2016
13
The ISOMETER® is able to measure the insulation resistance reliably and precisely in all
common IT systems (unearthed systems). Due to various applications, system types, op-
erating conditions, application of variable-speed drives, high system leakage capacitanc-
es etc., the measurement technique must be able to meet varying requirements in order
to ensure an optimised response time and an optimised relative uncertainty. Different
measurement profiles which can be selected from a setup menu allow optimum adapta-
tion of the measurement technique to the specific application.
If the preset response value falls below the value of alarm 1 and/or alarm 2, the associated
alarm relays switch, the LEDs ALARM 1 or ALARM 2 light and the measured value is shown
on the LC display (in case of insulation faults in DC systems, a trend graph for the faulty
conductor L+/L- is displayed). If the fault memory is activated, the fault message will be
stored. Pressing the RESET button resets the insulation fault message, provided that the
insulation resistance is at least 25 % above the preset response value. As additional Infor-
mation, the quality of the measuring signal and the time required to update the meas-
ured value are shown on the display. A poor signal quality (1-2 bars) may be an indication
that the wrong measurement profile has been selected.
The ISOMETER® has an internal system isolating switch, which makes it possible to oper-
ate several ISOMETER®s in coupled IT systems. For this purpose, the ISOMETER®s are con-
nected via an Ethernet bus. The integrated ISOnet function ensures that only one
ISOMETER® is actively measuring at a time, while the other devices are completely isolat-
ed from the system and waiting in standby mode for measuring permission.
3.4 Insulation fault location
An additional function of the ISOMETER® in combination with the EDS is the selective in-
sulation fault location. Therefore, the ISOMETER® generates a periodic locating current af-
ter the values has fallen below the set response value
R
an2
(LED ALARM 2). Thereby, the
system conductors are alternately connected to earth via a defined resistance. The result-
ing locating current depends on the size of the existing insulation fault and the system
voltage. It is limited by the ISOMETER® depending on the settings. The insulation fault is
selectively located by means of the EDS and the measuring current transformer connect-
ed to it. The locating current flows from the locating current injector via the live lines to
the insulation fault position taking the shortest way. From there, it flows through the in-
sulation fault and the conductor PE back to the ISOMETER®. This locating current pulse is
detected by the measuring current transformer on the insulation fault path and signalled
by the connected EDS.
For the duration of the insulation fault location, the function of the insulation monitoring
device is deactivated. If during the insulation fault location the locating current falls be-
low the value measurable by the EDS, the insulation fault location is ended by the
ISOMETER®.
3.5 Interfaces
• Communication protocol Modbus TCP
• BCOM for Bender device communication via Ethernet
• BS bus for communication of Bender devices (RS-485)
• BB bus for communication of Bender devices (Bender-internal device bus)
• Integrated web server for reading out measured values and for parameter setting
Risk of malfunctions due to excessive locating current on sensitive
system parts!
The locating current flowing between the IT system and earth can cause
controller faults in sensitive parts of the system, such as the PLC or relay.
Ensure that the level of the locating current is compatible with the system
to be monitored.
CAUTION