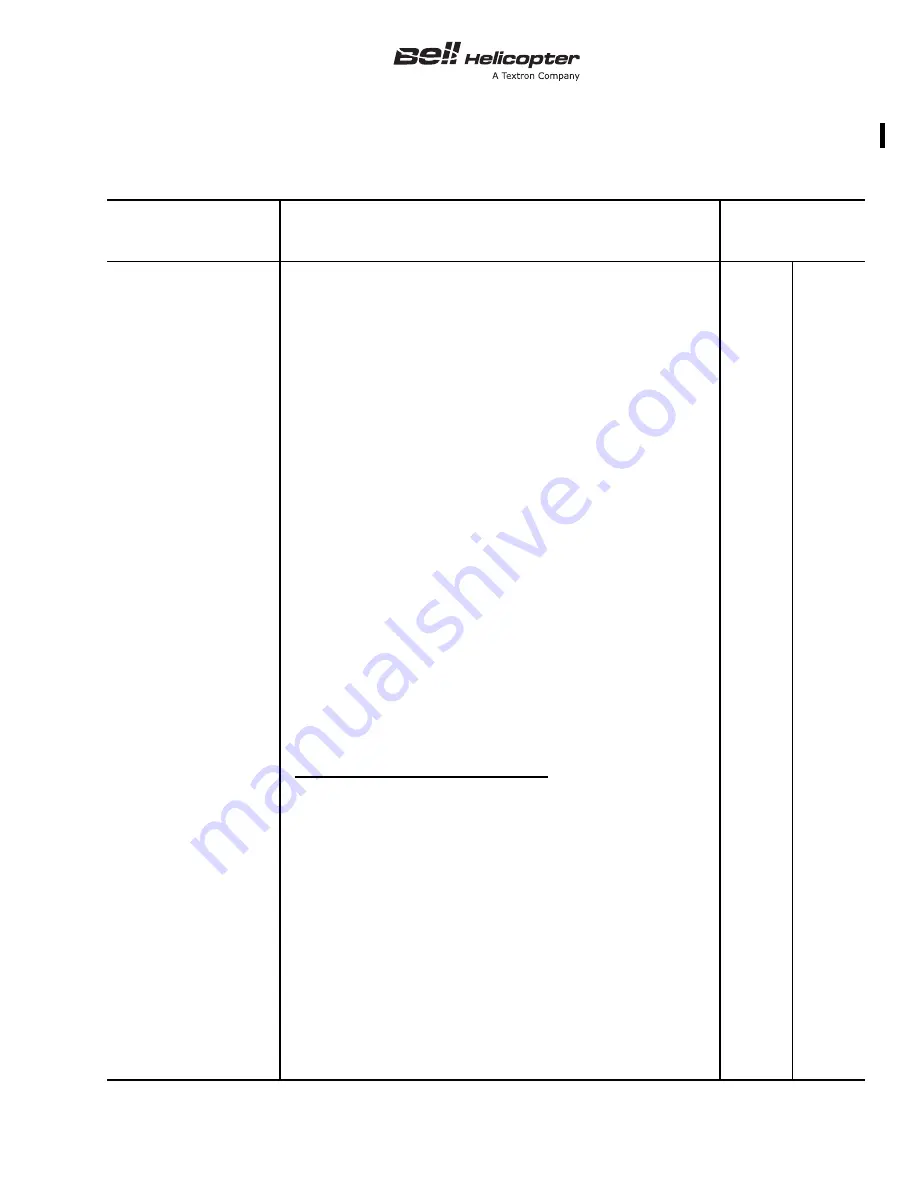
BHT-205A1-MM-1
5-00-00
Export Classification C, ECCN EAR99
SPECIAL INSPECTIONS
5-14.
EACH 8 HOURS OF COMPONENT OPERATION
DATA REFERENCE
INSPECTION TASK DESCRIPTION
INITIAL
MECH OTHER
DATE: __________________W.O. _____________________
FACILITY: __________________________________________
HELICOPTER S/N: ___________________________________
REGISTRY NO.: _____________________________________
TOTAL TIME:_______________________________________
SIGNATURE:_______________
_________________________
Accomplish inspection of fin spar caps 212-030-447-001 and
212-030-447-101 every 8 flight hours.
NOTE
Fin spar cap 212-030-447-117 can be identified by
the presence of decals that identify the cold-worked
holes.
This special inspection is not required if fin spar cap
212-030-447-117 has been installed as original equipment or in
accordance with TB 205-00-111.
FIN SPAR CAP 212-030-447-001/101
ASB 205-98-70
1.
Carry out 8 hour recurring inspection in accordance with
applicable section of ASB 205-98-70.
2.
Any discrepancies (cracks, corrosion, debonding, or other
damage) are to be reported to Product Support Engineering
before further flight.
5 JUL 2016 Rev. 9
Page 43/44
Содержание 205A-1
Страница 6: ......
Страница 12: ......
Страница 13: ......
Страница 14: ......
Страница 15: ......
Страница 16: ......
Страница 17: ......
Страница 18: ......
Страница 19: ......
Страница 20: ......
Страница 21: ......
Страница 22: ......
Страница 30: ......
Страница 32: ......
Страница 52: ......
Страница 56: ......
Страница 66: ......
Страница 72: ......
Страница 76: ......
Страница 78: ......
Страница 80: ......
Страница 82: ......
Страница 84: ......
Страница 86: ......
Страница 88: ......
Страница 92: ......
Страница 94: ......
Страница 96: ......
Страница 100: ......
Страница 108: ......
Страница 110: ......
Страница 114: ......
Страница 116: ......
Страница 122: ......
Страница 130: ......
Страница 132: ......
Страница 134: ......
Страница 138: ......
Страница 154: ......
Страница 156: ......