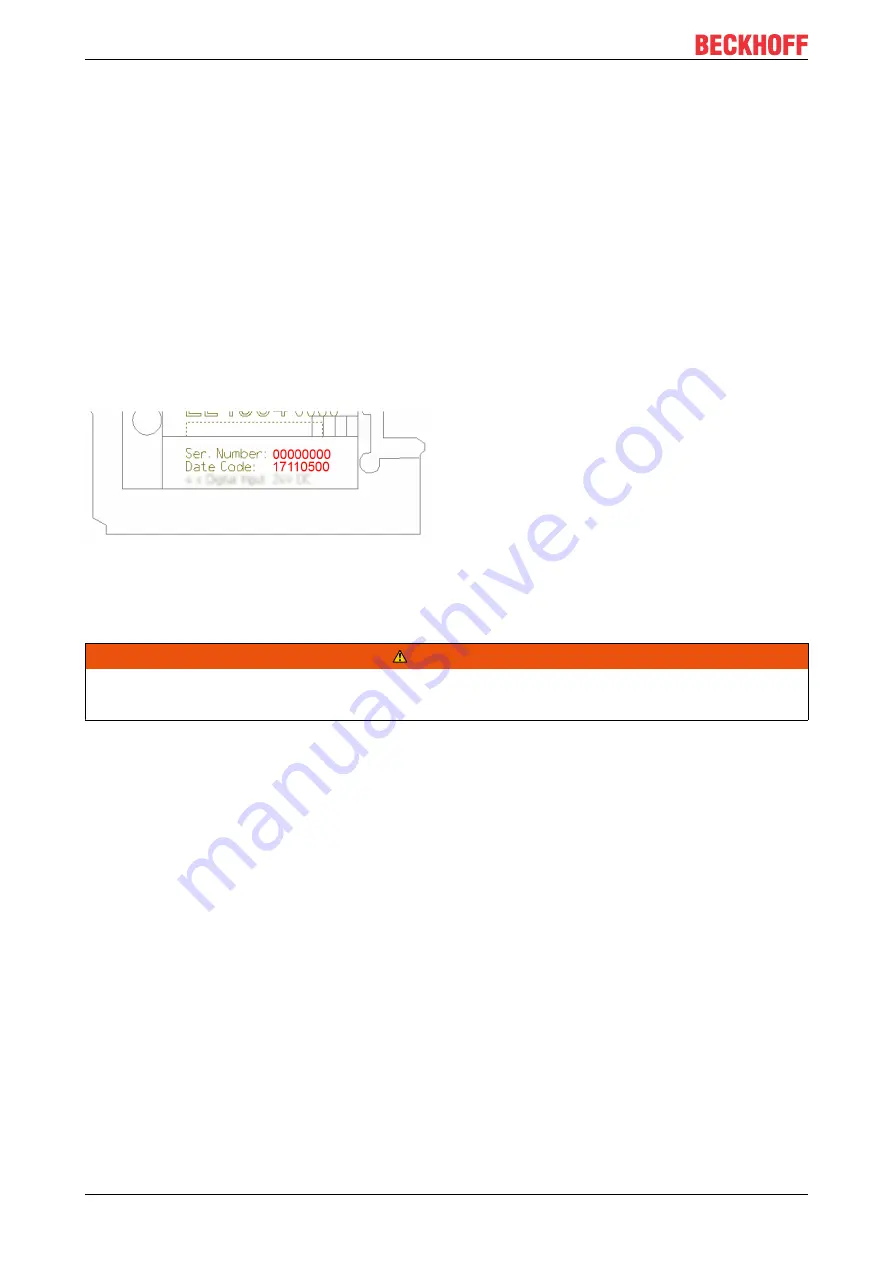
Operation
EL2912
48
Version: 1.0.0
4.7
Service life
The TwinSAFE terminals are designed for a service life of 20 years.
Due to the high diagnostic coverage within the lifecycle no special proof tests are required.
The TwinSAFE terminals bear a date code, which is composed as follows:
Date code: CW YY SW HW
Legend:
CW: Calendar week of manufacture
YY: Year of manufacture
SW: Software version
HW: Hardware version
Sample: Date Code 17 11 05 00
Calendar week: 17
Year: 2011
Software version: 05
Hardware version: 00
In addition the TwinSAFE terminals bear a unique serial number.
Fig. 34: Unique serial number of a TwinSAFE terminal
4.8
Decommissioning
WARNING
Risk of electric shock!
Bring the bus system into a safe, de-energized state before starting disassembly of the devices!
Disposal
In order to dispose of the device, it must be removed.
In accordance with the WEEE Directive 2012/19/EU, Beckhoff takes back old devices and accessories in
Germany for proper disposal. Transport costs will be borne by the sender.
Return the old devices with the note "for disposal" to:
Beckhoff Automation GmbH & Co. KG
Service Department
Stahlstrasse 31
D-33415 Verl
Observe the applicable national laws and guidelines for disposal!
• Housing components (polycarbonate, polyamide (PA6.6)) are suitable for plastic recycling.
• Metal parts can be sent for metal recycling.
• Electronic parts such as circuit boards must be disposed of in accordance with national electronics
scrap regulations.