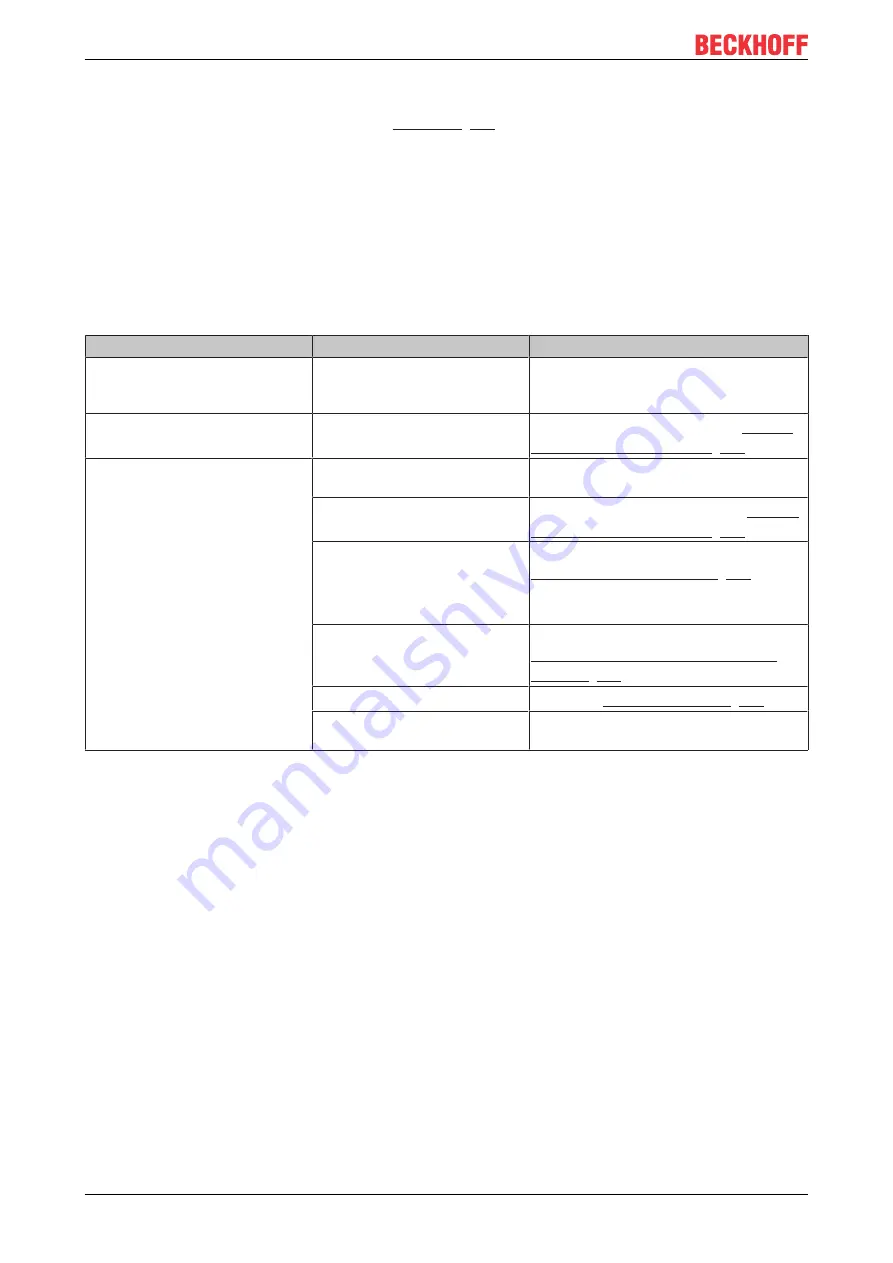
Commissioning
EP7402-0057
34
Version: 1.3
Possible results of the test run
• If the motor rotates continuously: skip to
• If the motor does not rotate continuously:
◦ Set the output variable "Enable" to 0
◦ Check the status bits in the input variable "Device Diag".
◦ Evaluate the status bits with the help of the table below.
◦ Set the output variable "Reset" to 1. (this resets the status bits)
◦ Set the output variable "Reset" to 0.
◦ Repeat the test run: to do this, set the output variable "Enable" to 1.
Set bit in "Device Diag"
Possible reasons
Solution
(none)
The output variable "Velocity" is
smaller than the parameter
8020:09 "start velocity".
Check the calculations.
"Channel 1 motor overload I2T
error"
The output current is too high.
Reduce the value of parameter
"Channel 1 commutation error"
The conveyor roller is loaded
1)
Remove any load from the conveyor
roller.
The output current is too low.
Increase the value of parameter
"Rampup velocity" is too high
1)
Check the calculation of the parameter
If the calculations are correct, reduce the
value of this parameter.
"Rampup needed switchover
events" is too low.
Increase the value of parameter
8023:21 "Rampup needed switchover
events" [
.
Incorrect motor parameters
The motor is too weak
1)
Insert a gear unit and recalculate all
parameters.
1)
Especially likely when the motor makes a sound with ascending pitch.