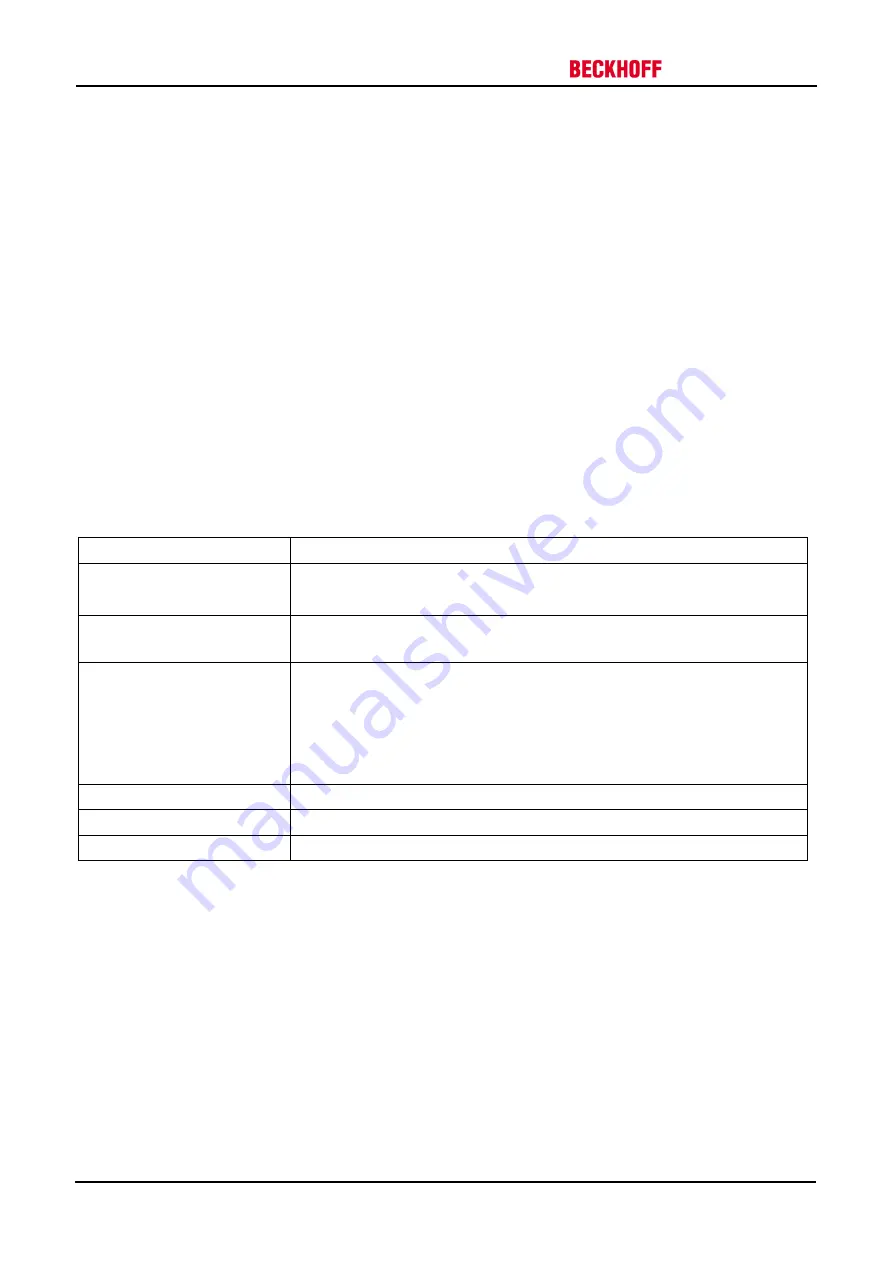
6 Technical description
Drive Technology
12 Version:
1.4
AM3100
6 Technical
description
6.1
Design of the motors
The synchronous servomotors of the AM3100 series are brushless three-phase motors for demanding servo-
applications. In conjunction with our digital servo terminal they are particularly suitable for positioning tasks in
industrial robots, machine tools, actuators etc. with demanding requirements in terms of dynamics and stability.
The servomotors are equipped with permanent magnets in the rotor. This advanced neodymium magnetic
material makes a significant contribution to the motors' exceptional dynamic properties. A three-phase winding
is housed in the stator, and this is powered by the servo drive. The motor has no brushes, the commutation
being implemented electronically in the servo drive.
The motors normally have an integrated resolver to provide feedback. Beckhoff servo drives analyse the
resolver position of the rotor and supply the motors with sine currents.
The motors are available with or without built-in holding brake which is free from backlash. The brake cannot be
retrofitted.
The motors have a matt black coating (similar to RAL 9005). The finish is not resistant against solvents (e.g.
trichlorethylene, thinners or similar).
6.2
General technical data
Climate category
2K3 according to EN 50178
Ambient temperature
(at rated values)
0 - +40 °C for site altitudes up to 1000 m amsl
It is vital to consult our applications department for ambient temperatures
above 40 °C and encapsulated installation of the motors.
Permissible humidity
(at rated values)
95% relative humidity, non-condensing
Power derating
(currents and torques)
For site altitudes above 1000 m amsl and 40 °C
6% at 2000 m amsl
17% at 3000m amsl
30% at 4000m amsl
55% at 5000m amsl
No derating for site altitudes above 1000 m amsl with temperature
reduction of 10K / 1000m
Ball bearing service life
=20,000 operating hours
Technical data
→
see Section 10
Storage and transport data
→
see Section 4