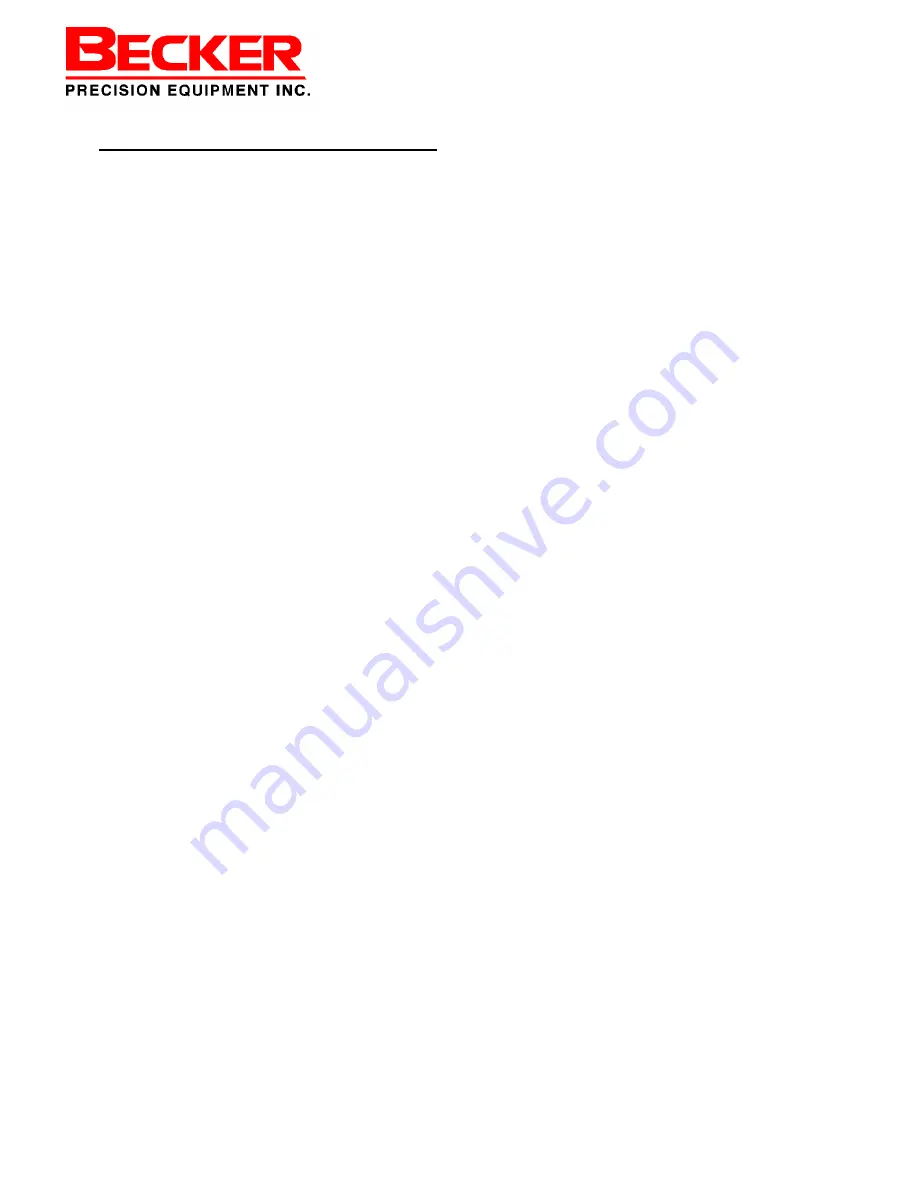
Changing Action of Positioner
To change the positioner from open on in-
creasing signal to close on increasing sig-
nal, or vice versa, the following parts kits
must be ordered:
To change
open on increasing
to
close on
increasing
: Part #25-1444 plus an Exten-
sion Rod (item #13 in drawing 35-0516,
see
Table 4
). The serial number of the ac-
tuator must be specified. The exact part
number of the extension rod will vary
based on the actuator stroke.
To change
close on increasing
to
open on
increasing
: Part #25-1289.
Note:
If con-
verting a
close on increasing signal
posi-
tioner to
open on increasing signal
, the
wide end of the tube (item #9) may be
shortened by 11/16" with a hack saw in
place of ordering part #25-1289.
The stroke length of the actuator cylinder
MUST be specified when ordering the
above part numbers. If the actuator serial
number cannot be found, the stroke length
can be found in the regulator model num-
ber. The stroke length is the first letter af-
ter the "H" in the model number. For ex-
ample model 10H12L6FG-SR-S-HSB-
40/35-100-O has a stroke length of "L", or
12 inches ["L" is the 12th letter in the al-
phabet]).
Refer to the drawings 35-0515 and 35-
0516 in the Appendix for the following:
1.
Disconnect all supply lines, instrument
line, and output line from the posi-
tioner.
2.
Remove the range spring (item #4) at
both ends and those items connecting
it to the rod (item #23) and the posi-
3. Remove the positioner from the
bracket (item #18). The tubing and
fittings on each side of the positioner
must be taken off and installed in the
opposite corner from their original po-
sition (see piping schematic provided
by Becker Precision Equipment) then
reattached to the positioner. This will
allow the positioner to maintain the
actuator failure mode when the posi-
tioner is turned upside down.
4.
Move the bracket assembly (item
#18), tube assembly (items #16 and
#17), and cover plate (item #11) to
the positions shown on the desired
drawing.
5.
Install the positioner in the opposite
of its original position (upside down if
it was right side up, right side up if it
was upside down).
6.
Using parts from the factory kit, as-
semble the spring and surrounding
hardware according to the drawing of
the desired configuration. (Note: all
original parts may not be used when
converting from
close on increasing
to
open on increasing
).
7.
The entire bracket assembly (item
#18) or the outer angle may need to
be turned upside down to accommo-
date the new spring height.
8.
Reconnect the supply, instrument,
and output lines according to piping
schematic supplied.
Note:
The flow direction must be main-
tained through the positioner bodies
when re-piping. (I.e. the flow [supply or
exhaust] moves from P1 to P2 and P3 to
HPP-4
12
September 1999
HPP-4 Positioner
Positioner Action