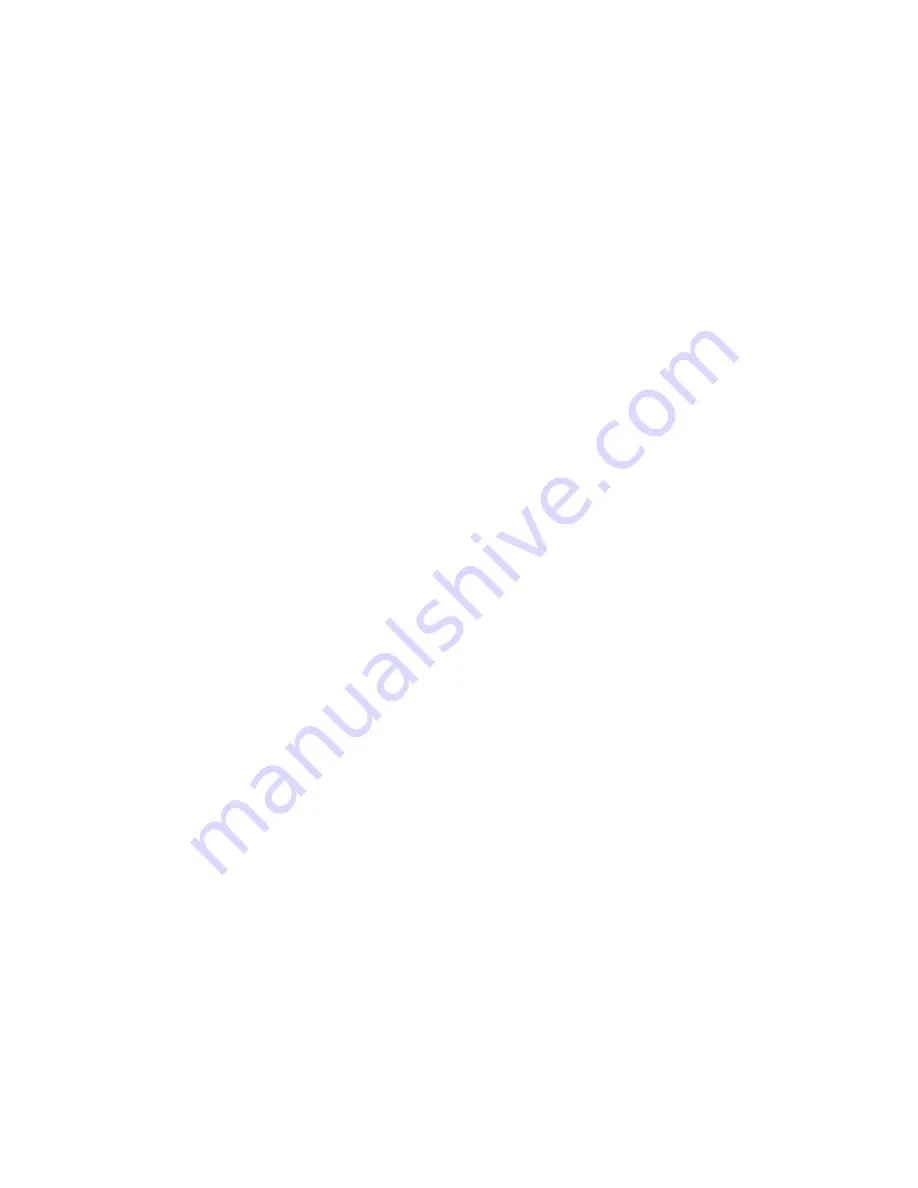
Page 4
nuts (2 - off) and fully tighten.
Stub pipe. Braze to downdrop pipe.
Using the approved jointing technique as detailed in the
contract specification, braze stub pipe to downdrop pipe.
With HTM 2022, HTM02-01 installations the copper stub
pipe is joined using the fluxless brazing technique with
Oxygen-free nitrogen purge.
Care should be taken when working in confined spaces,
precautions should be taken to avoid excessive build up of
nitrogen.
Note...
If the stub pipe has been reduced in length by any more than
100mm the plastic backplate must be protected against
contact with the brazing flame to avoid damage occurring.
Proprietary reusable heat shield compounds are available for
this purpose.
Terminal unit. Blank.
Fit blanking kit assembly Part No. 1825190 to terminal unit.
Note...
This will completely seal off the assembly ready for pipeline
carcass pressure testing.
Plaster box. Fit.
Locate plaster box over backplate and press into position.
Terminal unit. Pressure check.
When all first fix terminal units on a specific distribution
system have been installed, carry out pipeline carcass
pressure testing in accordance with the commissioning
procedure.
Plaster shield. Fit.
Locate plaster shield into plaster box and press into position.
Installation procedure - Bed head installation
Bed head trunking must provide suitable mounting studs to
enable the terminal unit backplate to be firmly secured. The
procedure to install a BEACONMEDÆS AGS terminal unit first
fix assembly within bed head trunking is as follows: -
Distribution system. Purge.
Using Medical quality air, purge associated distribution
system to remove all particulate matter prior to fitting
terminal unit.
Terminal unit. Locate pipe run.
Temporarily locate terminal unit backplate over securing
studs and align pipework. Establish necessary pipe run
layout and mark copper stub pipe for length required. Re-
move terminal unit assembly.
Copper stub pipe. Cut to length.
Using a wheel cutter, cut copper stub pipe to required
length. Ensure that ends are square, free from burrs and
re-round as necessary. Ensure that component is clean and
blow through as necessary to remove any particles.
Terminal unit. Fit.
Using any necessary copper pipe fittings, align copper stub
pipe with distribution system layout. Locate terminal unit
backplate over securing studs. Fit nuts (2 - off) and tighten.
Stub pipe. Braze to distribution system.
Using the approved jointing technique as detailed as
detailed in the contract specification, braze stub pipe to
distribution system and any fittings used. Care must be
taken to prevent heat damage to the terminal unit, bed head
trunking and any associated structure, electrical wiring etc.
Proprietary reusable heat shield compounds are available for
this purpose. With HTM 2022, HTM02-01 installations the
copper stub pipe is joined using the fluxless brazing
technique with Oxygen-free Nitrogen purge.
Care should be taken when working in confined spaces,
precautions should be taken to avoid excessive build up of
nitrogen.
Terminal unit. Blank.
Fit blanking kit assembly Part No. 1825190 to terminal unit.
Note...
This will completely seal off the assembly ready for pipeline
carcass pressure testing.
Terminal unit. Pressure check.
When all first fix terminal units on a specific distribution
system have been installed, carry out pipeline carcass
pressure testing in accordance with the commissioning
procedure.
Installation of Pendant Units
General requirements.
Pendant/Boom mounted AGS terminal units are installed in
the location and the quantity detailed in the contract
specification, however the following requirements should be
met unless otherwise stated: -
Terminal units should be securely fastened to a mounting
plate contained within the pendant.
The construction of the pendant should provide for
segregation of gases and electric’s, and provided with