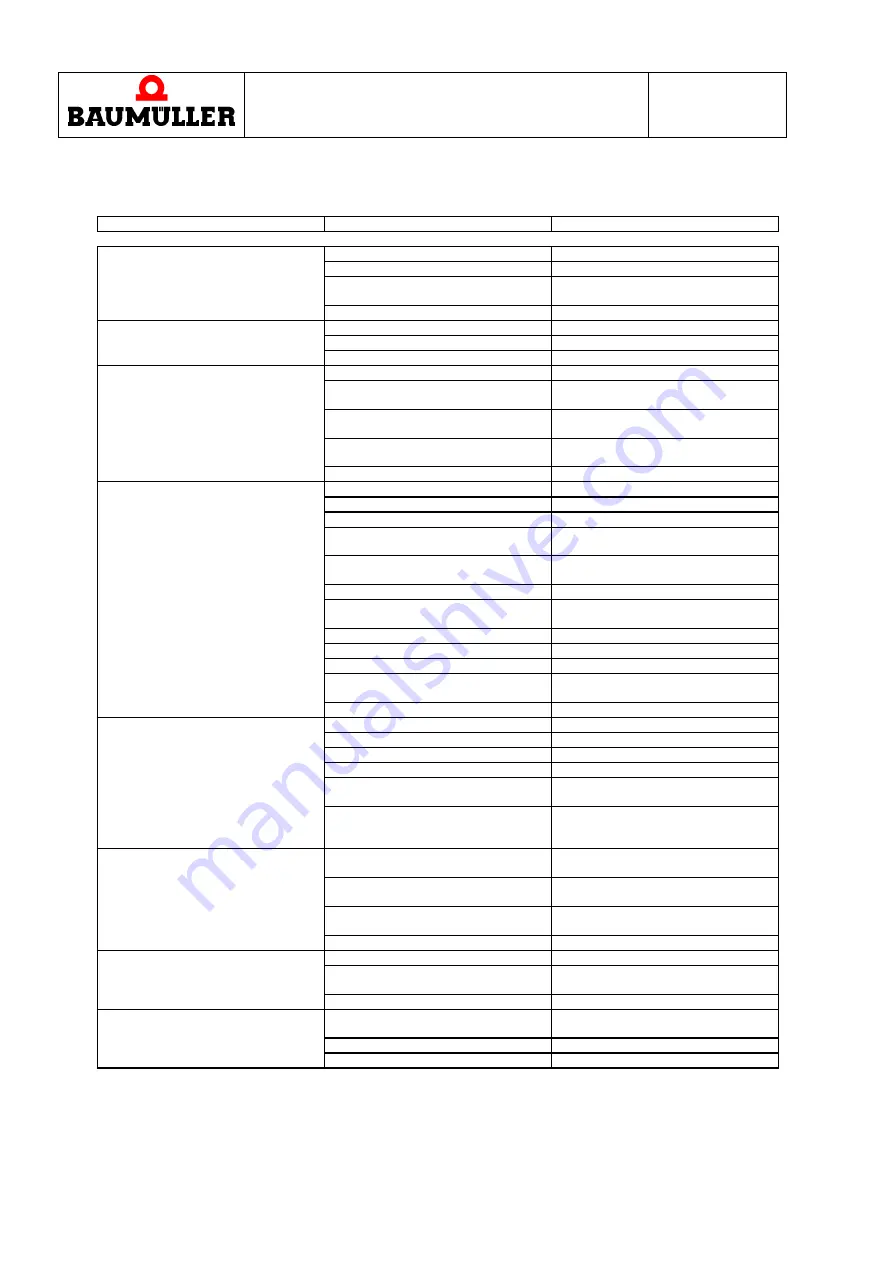
Edition: 11/2007
Technical Instructions
Commissioning and Maintenance Guide
TAM 00 526
Page
12
/ 18
3.5 Operating Disturbances
Error
Possible Cause
Removing the Source of the Error
Motor doesn't start
Supply lead interrupted Check
connections
Setting of brush yoke wrong
Adjust neutral zone
Current limiting doesn't respond
Loading too high or increase current
limiting
Brake doesn't release
Check brake connection
Motor speed drops when under load
Overloading
Carry out performance measurement
Voltage drops
Adjust neutral zone
Setting of brush yoke wrong
Adjust neutral zone
Motor gets too hot
Overloading
Carry out performance measurement
Insufficient cooling
Ensure that the cooling air can enter
without hindrance
Separately driven fan not running
Check connection of separately driven
fan
Current ripple too great
Check form factor, if necessary connect
armature choke on input side
Ambient temperature too high
Reduce performance
Severe brush sparking
Overloading
Carry out performance measurement
Setting of brush yoke wrong
Adjust neutral zone
Commutator surface very dirty
Clean commutator
Commutator out-of-round or with flat
points
Have commutator diameter-turned by
specialists
Lamellar insulation protruding
Have specialists scrape out insulation
grooves and remove sharp edges
Brushes worn out
Insert new brushes
Current ripple too great
Check form factor, if necessary connect
armature choke on input side
Switching error in a section of coil
Have experts carry out checking
Carbon brush sticks in holder
Ensure easy running
Vibrations on the drive
Remove possible unbalance
Unsuitable brush quality
Consult the manufacturer, stating the
technical data and environmental factors
Damage to coil
Get damage removed by specialists
Brush life too short
Current ripple too great
Check form factor
Connect armature choke on input side
Overloading
Carry
out
performance measurement
Current loading of carbon brush too low
Use genuine carbon brushes
Commutator surface affected
Find out the cause (dust, oil fumes, chemi-
cally active gases, etc.) and remove it
Brushes are of different or unsuitable
qualities
Fit the machines with suitable brushes
of consistent quality. Use genuine car-
bon brushes
Motor produces too much noise
Current ripple too great
Check form factor. Connect armature
choke on input side
Bearings warped, dirty or damaged
Realign the motor. Clean and grease the
bearings or replace them
Rotating parts unbalanced
Remove stimulation of vibration and
possible armature unbalance
Current convertor vibrates
Optimize current converter
Speed is unstable
Current convertor not set ideally
Optimize current converter
Large differences in loading
Increase current limiting or use a more
efficient device or motor
Tachometer signal not constant
Check tachometer
Motor accelerates uncontrollably
Error in speed feedback, e.g. tachome-
ter connected wrongly
Connect correct polarity
Tachometer carbon brushes worn-out
Replace carbon brushes
Tachometer lead interrupted
Lay a new tachometer lead