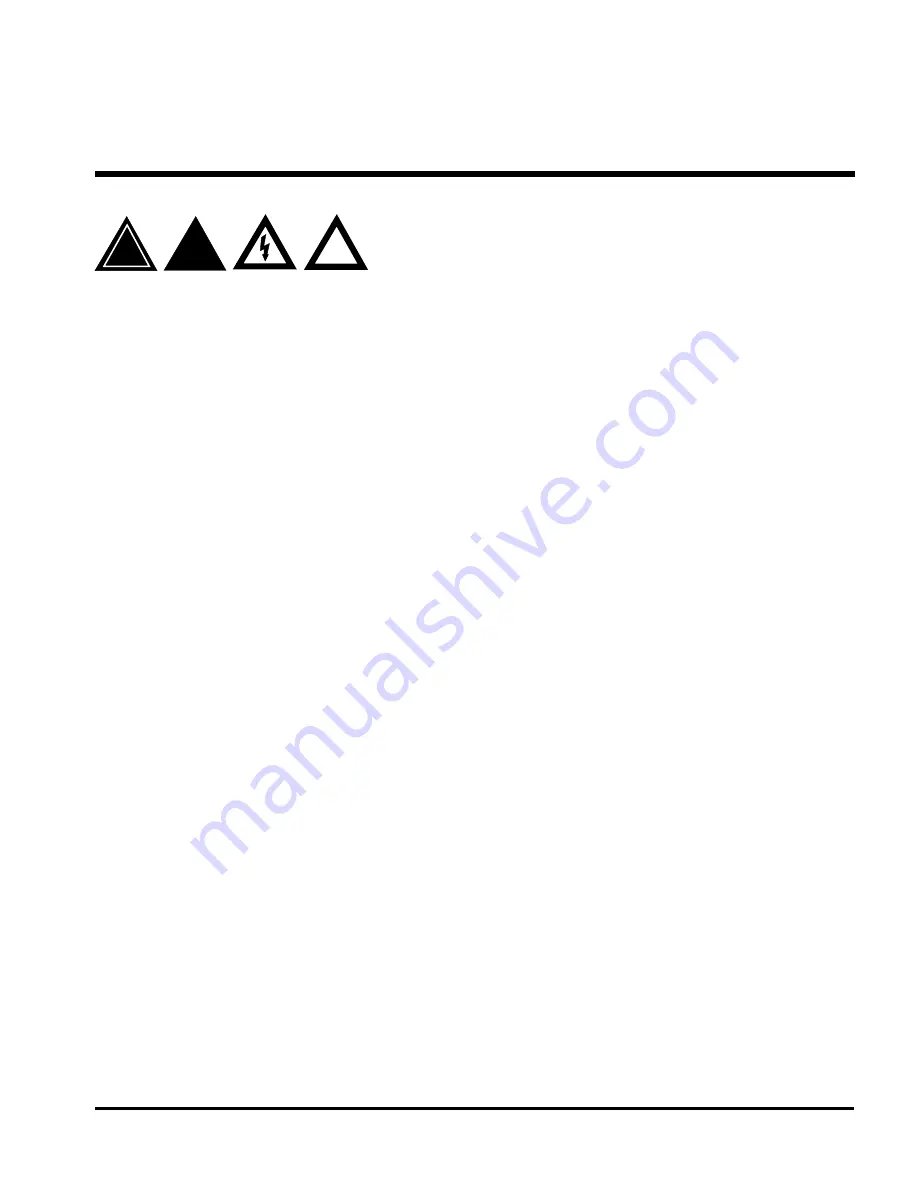
11
V
alue
S
erieS
V-710iJ M
anual
3
Preparing for Operation
!
!
!
When performing initial feeder adjustments
prior to operation, always make sure you turn
Off the main power switch and disconnect all
equipment from the electrical power source.
Failure to do so can expose you to a potential
startup and moving parts which can cause
serious injury.
Do not attempt to make any adjustments while
the feeder and machine of application are
running. Failure to do so can expose you to
moving parts which can cause serious injury.
Do not wear loose clothing when operating the
feeder.
Avoid making adjustments with loose or
unsecured parts. This can potentially damage
parts.
Once the Streamfeeder V-710IJ Universal Friction Feeder is installed
on your host system, you are then ready to prepare the machine for
operation. To do so, you must perform several adjustments with the
material you are going to be feeding. And, you must do a test run with
this material to verify that it is set correctly before you begin cycling
the feeder.
You will have to perform this procedure for material you
plan to feed.
The adjustments you must make (in order) are as follows:
1: Gate assembly adjustment
2: Side guides setting
3: Back wedge adjustment
4: Verifying proper installation
Leading edge
should be
2/3
into
transfer section
Содержание Streamfeeder V-710IJ
Страница 1: ...Manual Value Series V 710IJ ...
Страница 24: ...18 Value Series V 710IJ Manual Notes ...
Страница 28: ...22 Value Series V 710IJ Manual Notes ...
Страница 36: ...30 Value Series V 710IJ Manual Notes ...
Страница 37: ...31 Value Series V 710IJ Manual 7 Mechanical Components ...
Страница 41: ...35 Value Series V 710IJ Manual ...
Страница 43: ...37 Value Series V 710IJ Manual ...
Страница 45: ...39 Value Series V 710IJ Manual ...
Страница 49: ...43 Value Series V 710IJ Manual ...
Страница 51: ...45 Value Series V 710IJ Manual ...
Страница 52: ...46 Value Series V 710IJ Manual 8 Electrical Components ...
Страница 53: ...47 Value Series V 710IJ Manual ...
Страница 54: ...48 Value Series V 710IJ Manual ...
Страница 55: ...49 Value Series V 710IJ Manual ...
Страница 56: ...50 Value Series V 710IJ Manual Notes ...
Страница 57: ......
Страница 58: ... 2009 Thiele Technologies Inc Streamfeeder Printed in the USA ...