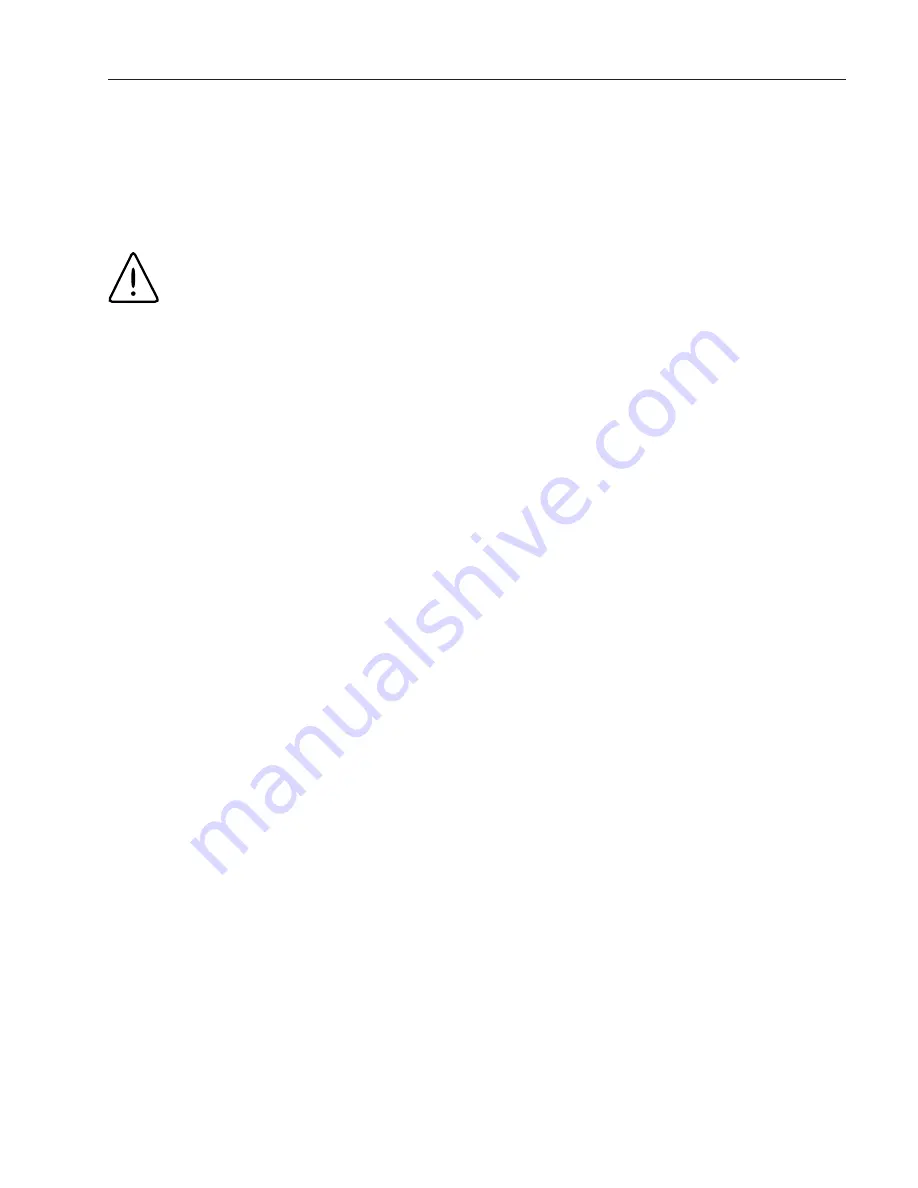
Warning
This warning is presented for compliance with Califor-
nia Proposition 65 and other regulatory agencies and
only applies to the insulation in this product. This prod-
uct contains refractory ceramic, refractory ceramic fiber
or fiberglass insulation, which can produce respirable
dust or fibers during disassembly. Dust or fibers can
cause irritation and can aggravate preexisting respira-
tory diseases. Refractory ceramic and refractory
ceramic
fibers (after reaching 1000°C) contain crystalline silica,
which can cause lung damage (silicosis). The Interna-
tional Agency for Research on Cancer (IARC) has clas-
sified refractory ceramic fiber and fiberglass as possi-
bly carcinogenic (Group 2B), and crystalline silica as
carcinogenic to humans (Group 1).
The insulating materials can be located in the door, the
hearth collar, in the chamber of the product or under
the hot plate top. Tests performed by the manufacturer
indicate that there is no risk of exposure to dust or re-
spirable fibers resulting from operation of this product
under normal conditions. However, there may be a risk
of exposure to respirable dust or fibers when repairing
or maintaining the insulating materials, or when other-
wise disturbing them in a manner which causes
release of dust or fibers. By using proper handling pro-
cedures and protective equipment you can work safely
with these insulating materials and minimize any expo-
sure.
Refer to the appropriate Material Safety Data Sheets
(MSDS) for information regarding proper handling and
recommended protective equipment. For additional
MSDS copies, or additional information concerning the
handling of refractory ceramic products, please contact
the Customer Service Department at Barnstead
International at 1-800-553-0039.
To avoid premature burnout of a replacement heating
element, be sure that the insulation tail supplied with
the replacement element is inserted between the two
legs of the element as shown in the drawing. Also be
sure that the heating element projects sufficiently into
the chamber. Insert element until welded portion
(where large diameter meets small diameter) projects
approximately 1/4" into inside of furnace chamber.
35
Maintenance and Servicing
Warning
To avoid electrical shock, this furnace
must always be disconnected from the
electrical supply prior to maintenance and
servicing. Do not clean clean furnace
without proper eye protection. Refer serv-
icing to qualified personnel.