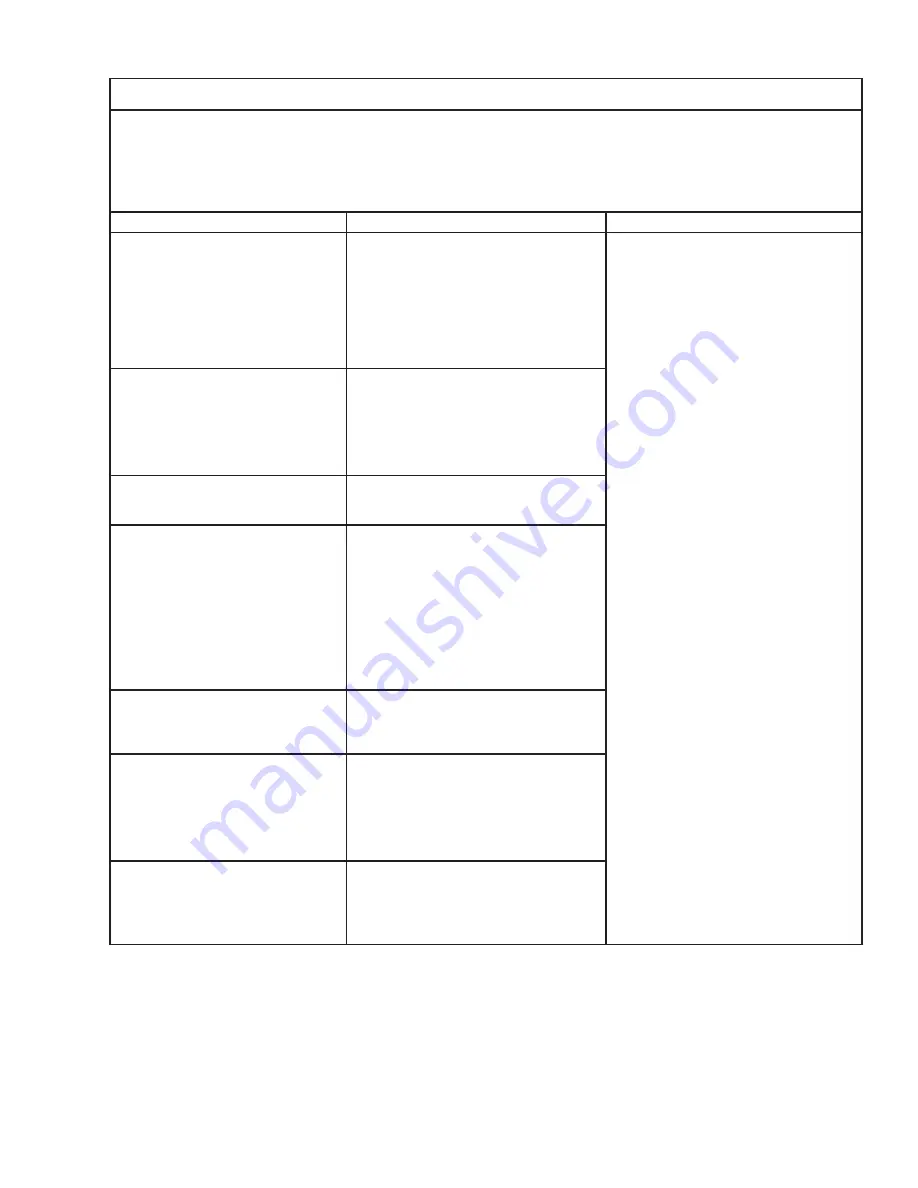
13
TROUBLE SHOOTING
CAUTION !
Always disconnect the pump from the electrical power source before handling.
If the system fails to operate properly, carefully read instructions and perform maintenance recommendations.
If operating problems persist, the following chart may be of assistance in identifying and correcting them:
MATCH “CAUSE” NUMBER WITH CORRELATING “CORRECTION” NUMBER
.
NOTE:
Not all problems and corrections will apply to each pump model.
PROBLEM
CAUSE
CORRECTION
Pump will not run
1.
Poor electrical connection, blown fuse,
tripped breaker or other interruption of power,
improper power supply.
2.
Motor or switch inoperative (to isolate
cause, go to manual operation of pump).
2a.
Float movement restricted.
2b. Switch will not activate pump or is defec-
tive.
3.
Insuf
fi
cient liquid level.
1. Check all electrical connections for
security. Have electrician measure current
in motor leads, if current is within ±20%
of locked rotor Amps, impeller is probably
locked. If current is 0, overload may be
tripped. Remove power, allow pump to cool,
then recheck current.
2a. Reposition pump or clean basin as
required to provide adequate clearance for
fl
oat.
2b. Disconnect level control. Set ohmmeter
for a low range, such as 100 ohms full scale
and connect to level control leads. Actuate
level control manually and check to see that
ohmmeter shows zero ohms for closed switch
and full scale for open switch. (Float Switch).
2c. Check winding insulation (Megger Test)
and winding resistance. If check is outside
of range, dry and recheck. If still defective,
replace per service instructions.
3. Make sure liquid level is at least equal to
suggested turn-on point.
4. Recheck all sizing calculations to
determine proper pump size.
5. Check discharge line for restrictions,
including ice if line passes through or into
cold areas.
6. Remove and examine check valve for
proper installation and freedom of operation.
7. Open valve.
8. Check cutter for freedom of operation,
security and condition. Clean cutter and inlet
of any obstruction.
9. Loosen union slightly to allow trapped air
to escape.Verify that turn-off level of switch
is set so that the suction is always
fl
ooded.
Clean vent hole.
10. Check rotation. If power supply is three
phase, reverse any two of three power supply
leads to ensure proper impeller rotation.
11. Repair
fi
xtures as required to eliminate
leakage.
12. Check pump temperature limits &
fl
uid
temperature.
13. Replace portion of discharge pipe with
fl
exible connector.
14. Turn to automatic position.
15. Check for leaks around basin inlet and
outlets.
Pump will not turn off
2a.
Float movement restricted.
2b.
Switch will not activate pump or is defec-
tive.
4.
Excessive in
fl
ow or pump not properly sized
for application.
9.
Pump may be airlocked.
14.
H-O-A switch on panel is in “HAND” position
Pump hums but does not run
1.
Incorrect voltage
8.
Impeller jammed or loose on shaft, worn or
damaged, impeller cavity or inlet plugged.
Pump delivers insuf
fi
cient capacity
1.
Incorrect voltage.
4.
Excessive in
fl
ow or pump not properly sized
for application.
5.
Discharge restricted.
6.
Check valve stuck closed or installed
backwards.
7.
Shut-off valve closed.
8.
Impeller jammed or loose on shaft, worn or
damaged, impeller cavity or inlet plugged.
9.
Pump may be airlocked.
10.
Pump stator damaged/torn.
Pump cycles too frequently or runs
periodically when
fi
xtures are not in use
6. Check valve stuck closed or installed
backwards.
11. Fixtures are leaking.
15. Ground water entering basin.
Pump shuts off and turns on indepen-
dent of switch, (trips thermal overload
protector).
CAUTION!
Pump may start
unexpectedly. Disconnect power supply.
1. Incorrect voltage.
4. Excessive in
fl
ow or pump not properly sized
for application.
8. Impeller jammed or loose on shaft, worn or
damaged, impeller cavity or inlet plugged
12. Excessive water temperature (Internal
protection only).
Pump operates noisily or vibrates
excessively
2c. Worn bearings, motor shaft bent
8. Debris in impeller cavity or brocken impeller.
10. Pump running backwards.
13. Piping attachments to buiding structure too
rigid or too loose.